Сущность обработки металлов давлением
Обновлено: 20.09.2024
Если при упругих деформациях деформируемое тело полностью восстанавливает исходную форму и размеры после снятия внешних сил, то при пластических деформациях изменение формы и размеров, вызванное действием внешних сил, сохраняется и после прекращения действия этих сил. Упругая деформация характеризуется смещением атомов относительно друг друга на величину, меньшую межатомных расстояний, а после снятия внешних сил атомы возвращаются в исходное положение. При пластических деформациях атомы смещаются относительно друг друга на величины, большие межатомных расстояний, и после снятия внешних сил не возвращаются в свое исходное положение, а занимают новые положения равновесия.
Величина пластической деформации не безгранична, при определенных ее значениях может начаться разрушение металла.
На величину пластической деформации, которую можно достичь без разрушения, оказывают влияние многие факторы, основные из них: механические свойства металла, температурно - скоростные условия деформирования и схема напряженного состояния. Последний фактор оказывает большое влияние на значение предельной деформации. Наибольшая предельная деформация. достигается при отсутствии растягивающих напряжений и увеличении сжимающих. В условиях всестороннего сжатия даже хрупкие материалы типа мрамора могут получать пластические деформации. В настоящее время установлено, что все современные сверхтвердые материалы при всестороннем сжатии под давлением свыше 60тыс.МПА становятся пластическими. Внешние условия (давление) способны воздействовать не только на пластичность, но и на прочность, а также и на другие свойства. Так, хрупкий молибден, подвергнутый гидропрессованию, повышает свою прочность до 3 раз, пластичность - в 10 раз.
Вопросы для самопроверки
1.В чем отличие пластической деформации от упругой?
2.Какие факторы влияют на степень пластической деформации?
3.В каких случаях используется закон постоянства объема?
4.На что оказывает влияние закон наименьшего сопротивления?
5.Какое влияние оказывает холодная пластическая деформация на структуру металла и на механические показатели?
6.Что такое температура рекристаллизации?
7.Какие процессы происходят при горячей пластической деформации?
8.Отличие неполной горячей деформации от полной?
9. Преимущества обработки металлов давлением по сравнению с другими технологическими процессами?
Существенные преимущества обработки металлов давлением по сравнению с обработкой резанием - возможность значительного уменьшения отхода металла, а также повышения производительности труда, поскольку в результате однократного приложения усилия можно значительно изменить форму и размеры деформируемой заготовки. Кроме того, пластическая деформация сопровождается изменением физико-механических свойств металла заготовки, что можно использовать для получения деталей с наилучшими эксплуатационными свойствами (прочностью, жесткостью, высокой износостойкостью и т.д.) при наименьшей их массе. Эти и другие преимущества обработки металлов давлением (отмеченные ниже) способствуют неуклонному росту ее удельного веса в металлообработке. Совершенствование технологических процессов обработки металлов давлением, а также применяемого оборудования позволяет расширять номенклатуру деталей, изготовляемых обработкой давлением, увеличивать диапазон деталей по массе и размерам, а также повышать точность размеров полуфабрикатов, получаемых обработкой металлов давлением,
В основе обработки металлов давлением лежит процесс пластической деформации, при котором изменяется форма без изменения массы. Вес расчеты размеров и формы тела при обработке давлением основаны на законе постоянства объема, суть которого заключается в том, что объем тела до и после пластической деформации принимается неизменным: V1 - V2 = const (V1, и V2 - до и после деформации).
Изменение формы тела может происходить в направлении трех главных осей; при этом каждая точка стремится перемещаться в том направлении, в котором создается наименьшее сопротивление ее перемещению. Это положение в теории обработки металлов давлением носит название закона наименьшего сопротивления.
При свободном формоизменении тела в различных направлениях наибольшая деформация происходит в том направлении, в котором большинство перемещающихся точек встречает наименьшее сопротивление своему перемещению.
Так, например, если при прокатке в двух валках с поперечными насечками течение металла вдоль оси прокатки сдерживается, а в поперечном направлении увеличивается, то при круговых насечках будет наблюдаться обратное явление.
Другим примером действия закона наименьшего сопротивления может служить превращение квадратного сечения (или любого другого) образца при его осаживании в круговое. Это правило наименьшего периметра при осаживании.
Законы постоянства объема и наименьшего сопротивления распространяются на все способы обработки металлов давлением.
Влияние обработки давлением на структуру и свойства металла
В зависимости от температурно-скоростных условий деформирования различают холодную и горячую деформацию.
Холодная деформация характеризуется изменением формы зерен, которые вытягиваются в направлении наиболее интенсивного течения металла. При холодной деформации формоизменение сопровождается изменением механических и физико-химических свойств металла. Это явление называют упрочнением (наклепом). Изменение механических свойств состоит в том, что при холодной пластической деформации по мере ее увеличения возрастают характеристики прочности, в то время как характеристики пластичности снижаются. Металл становится более твердым, но менее пластичным. Упрочнение возникает вследствии поворота плоскостей скольжения, увеличения искажений кристаллической решетки в процессе холодного деформирования ( накопление дислокаций у границ зерен ).
Изменения, внесенные холодной деформацией в структуру и свойства металла, не необратимы. Они могут быть устранены, например, с помощью термической обработки (отжигом). В этом случае происходит внутренняя перестройка, при которой за счет дополнительной тепловой энергии, увеличивающей подвижность атомов, в твердом металле без фазовых превращений из множества центров растут новые зерна, заменяющие собой вытянутые, деформированные зерна. Так как в равномерном температурном поле скорость роста зерен по всем направлениям одинакова, то новые зерна, появившиеся взамен деформированных, имеют примерно одинаковые размеры по всем направлениям.
Явления зарождения и роста новых равноосных зерен взамен деформированных, вытянутых, происходящее при определенных температурах, называется рекристаллизацией. Для чистых металлов рекристаллизация начинается при абсолютной температуре, равной 0,4 абсолютной температуры плавления металла. Рекристаллизация протекает с определенной скоростью, причем время, требуемое для рекристаллизации, тем меньше, чем выше температура нагрева деформированной заготовки.
При температурах ниже температуры начала рекристаллизации, наблюдается явление, называемое возвратом. При возврате (отдыхе) форма и размеры деформированных, вытянутых зерен не изменяются, но частично снимаются остаточные напряжения. Эти напряжения возникают из-за неоднородного нагрева или охлаждения (при литье и обработке давлением), неоднородности распределения деформаций при пластическом деформировании и т.д. Остаточные напряжения создают системы взаимно уравновешивающихся сил и находятся в заготовке, не нагруженной внешними силами. Снятие остаточных напряжений при возврате почти не изменяет механических свойств металла, но влияет на некоторые его физико-химические свойства. 'Гак, например, в результате возврата значительно повышается электрическая проводимость, сопротивление коррозии холоднодеформированного металла.
Формоизменение заготовки при температуре выше температуры рекристаллизации сопровождается одновременным протеканием упрочнения и рекристаллизации.
Горячей деформацией называют деформацию, характеризующуюся таким соотношением скоростей деформирования и рекристаллизации, при котором рекристаллизация успевает произойти во всем объеме заготовки и микроструктура после обработки давлением оказывается равноосной, без следов упрочнения. Чтобы обеспечить условия протекания горячей деформации, приходится с увеличением ее скорости повышать температуру нагрева заготовки (для увеличения скорости рекристаллизации). Если металл по окончании деформации имеет структуру, не полностью рекристаллизованную, со следами упрочнения, то такая деформация называется неполной горячей деформацией. Неполная горячая деформация приводит к получению неоднородной структуры, снижению механических свойств и пластичности, поэтому обычно нежелательна.
При горячей деформации сопротивление деформированию примерно в 10 раз меньше, чем при холодной деформации, а отсутствие упрочнения приводит к тому, что сопротивление деформированию (предел текучести) незначительно изменяется в процессе обработки давлением. Этим обстоятельством объясняется в основном то, что горячую обработку применяют для изготовления крупных деталей, так как при этом требуются меньшие усилия деформирования (менее мощное оборудование).
Следует учитывать, что при обработке давлением заготовок-малых размеров (малой толщины) трудно выдержать необходимые температурные условия ввиду быстрого их охлаждения на воздухе и от контакта с более холодным инструментом.
При горячей деформации пластичность металла выше, чем при холодной деформации. Поэтому горячую деформацию целесообразно применять при обработке труднодеформируемых, малопластичных металлов и сплавов, а также заготовок из литого металла (слитков). В то же время при горячей деформации окисление заготовки более интенсивно (на поверхности образуется слой окалины), что ухудшает качество поверхности и точность получаемых размеров.
Холодная деформация без нагрева заготовки позволяет получать большую точность размеров и лучшее качество поверхности по сравнению с обработкой давлением при достаточно высоких температурах. Отметим, что обработка давлением без специального нагрева заготовки позволяет сократить продолжительность технологического цикла, облегчает использование средств механизации и автоматизации и повышает производительность труда.
Влияние холодной деформации на свойства металла можно использовать для получения наилучших эксплуатационных свойств деталей, а управление изменением свойств в требуемом направлении и на желаемую величину может быть достигнуто выбором рационального сочетания холодной и горячей деформации, а также числа и режимов термических обработок в процессе изготовления детали.
Исходной заготовкой для начальных процессов обработки металлов давлением (прокатки, прессования) является слиток. Кристаллическое строение слитка неоднородно (кристаллиты различных размеров и форм), кроме того, в нем имеется пористость, газовые пузыри и т.п. Обработка давлением слитка при нагреве его до достаточно высоких температур приводит к деформации кристаллитов и частичной заварке пор и раковин. Таким образом, при обработке давлением слитка может увеличиться и плотность металла.
В результате деформации кристаллитов и последующей рекристаллизации металл получает мелкозернистое строение, т.е. размеры зерен после рекристаллизации исчисляются в сотых или десятых долях миллиметра, причем эти размеры примерно одинаковы по всем направлениям (равноосная структура).
Если слиток загрязнен неметаллическими включениями, обычно распологающимися по границам кристаллитов, то в результате обработки давлением неметаллические включения вытягиваются в виде волокон по направлению наиболее интенсивного течения металла.
Полученные в результате обработки давлением литого металла волокнистая макроструктура не может быть разрушена ни термической обработкой, ни последующей обработкой давлением. Последняя в зависимости от характера деформирования может изменить лишь направление и форму волокон макроструктуры.
Металл с явно выраженной волокнистой макроструктурой характеризуется анизотропией (векториальностью) механических свойств. При этом характеристики прочности (предел текучести, временное сопротивление и др.) в разных направлениях отличаются незначительно, а характеристики пластичности (относительное удлинение, ударная вязкость и др.) вдоль волокон выше, чем поперек их.
Так как направление волокон зависит от характера деформирования заготовки, то в готовой детали желательно получить такое расположение волокон, при котором она имела бы наилучшие свойства. При этом общие рекомендации следующие; необходимо, чтобы наибольшие растягивающие напряжения, возникающие в деталях в процессе работы, были направлены вдоль волокон, а если какой-либо элемент этой детали работает на срез, то желательно, чтобы перерезывающие силы действовали поперек волокон; необходимо чтобы волокна подходили к наружным поверхностям детали по касательной и не перерезались наружными поверхностями детали.
Выполнение этих требований не только повышает надежность детали (в том числе и при динамическом нагружении), но и улучшает другие эксплуатационные характеристики, например сопротивление истиранию.
Возможность воздействия обработкой давлением на расположение волокон, а следовательно, и на свойства деталей можно иллюстрировать следующим примером. В зубчатом колесе, изготовленном резанием из прутка (рис 4.1,б), растягивающие напряжения, возникающие при изгибе зуба 1 действием сопряженного колеса, направлены поперек волокон, что понижает их надежность. При горячей штамповке зубчатого колеса из полосы (рис 4.1,в) волокна по-разному ориентированы в различных зубьях относительно наибольших растягивающих напряжений: в зубе 1 -вдоль волокон, а в зубе 2 - поперек. Следовательно, зубья оказываются неравнопрочными.
При изготовлении зубчатого колеса осадкой (рис.4.1,г) из отрезка прутка круглого сечения волокна получают почти радиальное направление. В этом случае все зубья равнопрочны, а наибольшие растягивающие напряжения, возникающие при изгибе, направлены почти вдоль волокон.
Обработки материалов давлением
Обработкой давлением называются процессы получения заготовок или деталей машин силовым воздействием инструмента на исходную заготовку из исходного материала.
Пластическое деформирование при обработке давлением, состоящее в преобразовании заготовки простой формы в деталь более сложной формы того же объема, относится к малоотходной технологии. Обработкой давлением получают не только заданную форму и размеры, но и обеспечивают требуемое качество металла, надежность работы изделия.
Существенные преимущества обработки металлов давлением по сравнению с обработкой резанием - возможность значительного уменьшения отхода металла, а также повышения производительности труда, поскольку в результате однократного приложения усилия можно значительно изменить форму и размеры деформируемой заготовки. Кроме того, пластическая деформация сопровождается изменением физико-механических свойств металла заготовки, что можно использовать для получения деталей с наилучшими эксплуатационными свойствами (прочностью, жесткостью, высокой износостойкостью и т. д.) при наименьшей их массе. Эти преимущества обработки металлов давлением способствуют неуклонному росту ее удельного веса в металлообработке.
Классификация технологических процессов
обработки металлов давлением
Процессы обработки металлов давлением по назначению делят на два вида:
1. Для получения заготовок постоянного поперечного сечения по длине (прутков, проволоки, лент, листов). Такие заготовки используются в строительных конструкциях или в качестве заготовок для обработки резанием или давлением. Основные разновидности таких процессов – прокатка, прессование и волочение.
2. Для получения деталей или заготовок (полуфабрикатов), имеющих приближенно формы и размеры готовых деталей. Основные разновидности таких процессов – ковка и штамповка.
Пластическое деформирование в обработке металлов давлением осуществляется при различных схемах напряженного и деформированного состояний, при этом исходная заготовка может быть объемным телом, прутком, листом.
По назначению процессы обработки металлов давлением группируют следующим образом:
– для получения изделий постоянного поперечного сечения по длине (прутков, проволоки, лент, листов), применяемых в строительных конструкциях или в качестве заготовок для последующего изготовления деталей – прокатка, волочение, прессование;
– для получения деталей или заготовок, имеющих формы и размеры, приближенные к размерам и формам готовых деталей, требующих механической обработки для придания им окончательных размеров и заданного качества поверхности – ковка, штамповка.
Основными схемами деформирования объемной заготовки являются:
– сжатие между плоскостями инструмента – ковка;
– ротационное обжатие вращающимися валками – прокатка;
– затекание металла в полость инструмента – штамповка;
– выдавливание металла из полости инструмента – прессование;
– вытягивание металла из полости инструмента – волочение.
Характер пластической деформации зависит от соотношения процессов упрочнения и разупрочнения. Губкиным С.И. предложено различать следующие виды деформации и, соответственно, виды обработки давлением.
Горячая деформация – деформация, после которой металл не получает упрочнения. Рекристаллизация успевает пройти полностью, новые равноосные зерна полностью заменяют деформированные зерна, искажения кристаллической решетки отсутствуют. Деформация имеет место при температурах выше температуры начала рекристаллизации.
Неполная горячая деформация характеризуется незавершенностью процесса рекристаллизации, которая не успевает закончиться, так как скорость ее недостаточна по сравнению со скоростью деформации. Часть зерен остается деформированными и металл упрочняется. Возникают значительные остаточные напряжения, которые могут привести к разрушению. Такая деформация наиболее вероятна при температуре, незначительно превышающей температуру начала рекристаллизации. Ее следует избегать при обработке давлением.
При неполной холодной деформации рекристаллизация не происходит, но протекают процессы возврата. Температура деформации несколько выше температуры возврата, а скорость деформации меньше скорости возврата. Остаточные напряжения в значительной мере снимаются, интенсивность упрочнения снижается.
При холодной деформации разупрочняющие процессы не происходят. Температура холодной деформации ниже температуры начала возврата.
Холодная и горячая деформации не связаны с деформацией с нагревом или без нагрева, а зависят только от протекания процессов упрочнения и разупрочнения. Поэтому, например, деформация свинца, олова, кадмия и некоторых других металлов при комнатной температуре является с этой точки зрения горячей деформацией.
Общие сведения об обработке металлов давлением
1. Обработка давлением основана на способности металлов необратимо изменять свою форму без разрушения под действием внешних сил. Она обеспечивает получение заготовок для производства деталей, а в некоторых случаях и самих деталей требуемых форм и размеров с необходимыми механическими и физическими свойствами.
Обработка давлением – прогрессивный, экономичный и высокопроизводительный способ металлообработки, развивающийся в направлении максимального приближения форм и размеров заготовки к форме и размерам детали, что обеспечивает лучшее использование металла, сокращение трудоёмкости последующей обработки резанием и уменьшением себестоимости продукции.
При производстве металлических изделий широко применяют обработку металлов давлением как в горячем состоянии, так и в холодном. Основными способами обработки металлов давлением являются прокатка, волочение, прессование, ковка и штамповка.
Прокатка – один из важных способов обработки давлением, которым обрабатывается более 75% выплавляемой стали.
Прокатка осуществляется захватом заготовки 2 (рис. 22, а) и деформации ее между вращающимися в разные стороны валками 1 прокатного стана; при этом толщина заготовки уменьшается, а длина и ширина увеличиваются. Валки имеют гладкую поверхность для прокатки листов или вырезанные ручьи, составляющие калибры, для получения круглой или квадратной полосы, рельсов и т. д.
Волочение – процесс, при котором заготовка 2 (рис. 22, б) протягивается на волочильном стане через отверстие инструмента 1, называемого волокой; при этом поперечное сечение заготовки уменьшается; а длина ее увеличивается.
Рис. 22 Схемы основных способов обработки металлов давлением:
а – прокатка; б – волочение; в – прессование; г – ковка; д – объемная штамповка; е – листовая штамповка
Прессование представляет собой выдавливание заготовки 4 (рис. 22, в), помещенной в специальный цилиндр – контейнер 3,через отверстие матрицы 5, удерживаемой матрицедержателем 6;выдавливание производят при помощи пресс – шайбы 2 и пуансона 1. В зависимости от формы и размеров отверстия матрицы получают разнообразные изделия.
Ковка металла заключается в обжатии заготовки 2 (рис. 22, г) между верхним 1 и нижним 3 бойками молота с применением разнообразного инструмента. Свободной ковкой получают поковки различных размеров простой или сложной формы на молотах или прессах.
Штамповка – процесс деформации металла в штампах, форма и размеры внутренней полости которых определяют форму и размеры получаемой поковки. Различают объемную и листовую штамповку.
При объемной штамповке (рис. 22, д) на горячештамповочных молотах и прессах заготовка 2 деформируется в штампе 1. Листовая штамповка (рис. 22, е) осуществляется на холодноштамповочных прессах. При помощи пуансона 1, прижима 2, матрицы 3 листовая заготовка 4 превращается в изделие.
2. Различают горячую и холодную обработки металлов давлением.
Горячая обработка металлов давлением характеризуется явлениями возврата и рекристаллизации, отсутствием упрочнения (наклёпа); механические и физико-химические свойства металла изменяются сравнительно мало. Пластическая деформация не создаёт полосчатости (неравномерности) микроструктуры, но приводит к образованию полосчатости макроструктуры у литых заготовок (слитков) или к изменению направления волокон макроструктуры (прядей неметаллических включений) при обработке металлов давлением заготовок, полученных прокаткой, прессованием и волочением. Полосчатость макроструктуры создаёт анизотропию механических свойств, при которой свойства материала вдоль волокон обычно лучше его свойств в поперечном направлении.
При холодной обработке металлов давлением процесс пластической деформации сопровождается упрочнением, которое изменяет механические и физико-химические характеристики металла, создаёт полосчатость микроструктуры и также изменяет направление волокон макроструктуры. При холодной обработке металлов давлением возникает текстура, создающая анизотропию не только механических, но и физико-химических свойств металла. Используя влияние обработки металлов давлением на свойства металла, можно изготавливать детали с наилучшими свойствами при минимальной массе.
Для получения заготовок обработкой давлением используют различные деформируемые материалы: углеродистые, легированные и высоколегированные стали, жаропрочные сплавы, сплавы на основе алюминия, меди, магния, титана, никеля и др.
Исходными заготовками для обработки металлов давлением являются плоские и круглые слитки разных размеров и массы из стали и цветных сплавов.
До обработки давлением слитки подвергают механической обработке, которая заключается в отрезке прибыльной и донной частей и очистке поверхности от литейных пороков.
Размеры и масса слитков зависят от их назначения. Цилиндрические слитки предназначаются для изготовления прутков, профилей и труб. Их получают главным образом методом непрерывного литья. Плоские слитки применяют для изготовления различных поковок, листов, лент, полос и т. п.
3. Существенные преимущества обработки металлов давлением по сравнению с литейным производством и обработкой резанием – возможность значительного уменьшения отхода металла, а также повышения производительности труда, поскольку в результате однократного приложения усилия можно значительно изменить форму и размеры деформируемой заготовки. Кроме того, пластическая деформация сопровождается изменением физико-механических свойств металла заготовки, что можно использовать для получения деталей с наилучшими эксплуатационными свойствами (прочностью, жесткостью, высокой износостойкостью и т. д.) при наименьшей их массе.
Эти и другие преимущества обработки металлов давлением (отмеченные ниже) способствуют неуклонному росту ее удельного веса в металлообработке. Совершенствование технологических процессов обработки металлов давлением, а также применяемого оборудования позволяет расширять номенклатуру деталей, изготовляемых обработкой давлением, увеличивать диапазон деталей по массе и размерам, а также повышать точность размеров полуфабрикатов, получаемых обработкой металлов давлением.
Обработка металлов давлением
Сущность обработки металла давлением состоит в целенаправленной пластической деформации, придающей ему определенные форму и размеры без разрушения или с разрушением, в ходе которой измельчается грубозернистая литая структура, устраняются пористость и рыхлость, улучшается металлургическое качество и создается благоприятная ориентировка вновь образовавшихся структурных составляющих металла.
Вследствие благоприятных структурных изменений, происходящих при обработке давлением, металл получает более высокий комплекс прочностных и пластических свойств по сравнению с литым. При горячей обработке давлением, когда металл обладает большой пластичностью при малой прочности, его зерна вытягиваются итрансформируются в волокна.
Волокнистое строение металла обеспечивает важные преимущества по сравнению с обычной зернистой структурой, поскольку прочность деформированного металла на разрыв вдоль волокон оказывается значительно выше, чем в поперечном направлении.
То же можно сказать и о сопротивлении срезающим нагрузкам: прочность на срез поперек волокон значительно выше, чем вдоль них. Зная характер нагружения отдельных элементов деталей в эксплуатационных условиях, можно еще при изготовлении заготовок придавать волокнам наивыгоднейшую ориентировку, отвечающую характеру нагружения соответствующих элементов деталей, и этим обеспечивать большой запас прочности деталей. Например, показанное на рис. 4.25, а изготовление зубчатого колеса из прутка где растягивающие напряжения, возникающие при изгибу зуба направлены поперек волокон, а следовательно прочность зубьев будет пониженной. Изготовленное зубчатое колесо осадкой рис. 4.25, б из отрезка прутка круглого сечения волокна получаются радиального направления. В этом случае все зубья будут равнопрочны, а растягивающие напряжения, возникающие в зубьях при изгибе направлены вдоль волокон. При этом возрастает не только прочность зубьев, но и увеличивается износостойкость.
Рис 4.25. Схемы макроструктуры зубчатых колес, изготовленных различными способами. |
4.3.1. Прокатка. Прокатка представляет собой процесс пластической деформации слитка или иной продолговатой металлической заготовки между двумя вращающимися валками, расстояние между рабочими поверхностями которых меньше высоты заготовки. Целью прокатки является получение разнообразной продукции, различающейся профилями и размерами поперечного сечения, а также балок, прутков и составляющей, так называемый сортамент проката. Сортамент стального проката включает (рис. 4.26):
Рис. 4.26. Профили сортового проката (а) и периодического профиля (б). |
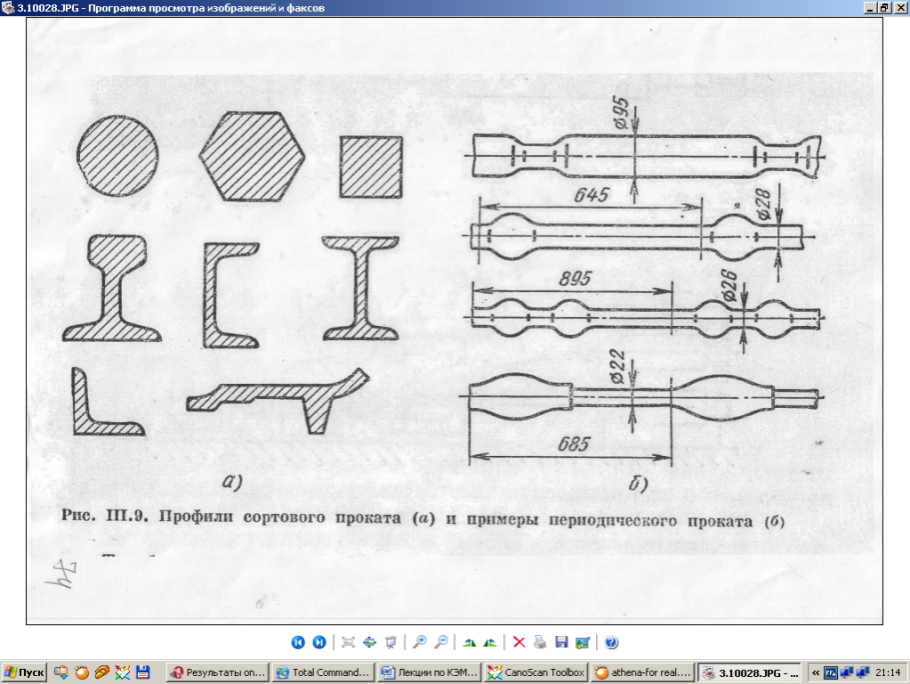
сортовой прокат простого и фасонного профиля. Простой профиль используется для порезки на заготовки, которые идут либо на дальнейшую обработку давлением – ковку или штамповку, либо на механическую обработку для изготовления различных деталей. Фасонный профиль (рис. 4.26, а)главным образом используется для различных строительных конструкций, включая железнодорожные пути;
периодический прокат (рис. 4.26, б) – прокат с периодически изменяющимся по длине профилем. Он используется в качестве заготовок для штамповки (например, заготовок шатунов автомобильных двигателей) или непосредственно для механической обработки.
специальный прокат включает в себя вагонные колеса, шпунтовые сваи, автоободья и т.д.;
трубы бесшовные различного диаметра с разной толщиной стенок, разнообразного назначения;
листовой прокат делится на толстолистовую сталь толщиной свыше 4 мм и тонколистовую 0,2-3,75 мм;
Существуют также специально разработанные сортаменты для выпуска проката из цветных металлов и сплавов – меди, алюминия, латуни, дюраля в виде листов, ленты, труб, прутков и других изделий. Важнейшей особенностью деформации металла при прокатке является получение волокнистой структуры металла с ориентировкой волокон вдоль направления прокатки, т. е. перпендикулярно осям вращения валков.
Это объясняется тем, что при сдавливании сечения заготовки между валками вытяжка металла в основном происходит в направлении наименьшего сопротивления, т. е. при выходе из валков. Деформации и вытяжке в поперечном направлении препятствуют трение о поверхности валков. Так как общая вытяжка металла заготовки складывается из вытяжек его отдельных зерен, то последние должны превратиться в волокна. Заготовка захватывается в рабочее пространство между валками и перемещается силами трения, возникающими между нею и валками (рис. 4.27).
Действительно, при подходе заготовки к валкам в точках первичного контакта возникают, с одной стороны, радиально ориентированные активные Р и равные им реактивные (действующие на заготовку) N силы, а с другой — силы трения Т, касательные к поверхности валков в точках упомянутого контакта. Каждая из сил трения равна произведению нормальной силы Nна коэффициент трения f, т. е. Т = Nf. Рассмотрим проекции сил N и Т на продольное (горизонтальное) направление X и вертикальное – Z. При этом заметим, что силы Nx выталкивают заготовку из рабочего пространства, а силы Тх – втягивают в него заготовку. Условием захвата заготовки валками и осуществления прокатки будет неравенство Тх>Nх. Но так как Тх·cosα=Nf ·cosα, а Nx=N·sinα, то условием прокатки будет Nfcosα >Nsinα. Разделив обе части неравенства на Ncosα, получим f>tgα, где α – угол захвата.
Таким образом, условием захвата заготовки валками и осуществление процесса прокатки является превышение коэффициента трения над тангенсом угла захвата.
Прокатка металлов осуществляется на прокатных станах (рис. 4.28, г).
Основными рабочими элементами прокатных станов являются валки, имеющие цилиндрическую форму. Валки размещаются в основной части прокатного стана – рабочей клети 4. Рабочая часть валка (рис. 4.28, а) называется бочкой 1. Опорная часть валка шейка 2, соединительная – треф 3. Бочки могут быть гладкими или ручьевыми (рис. 4.28, а и 4.28, б). Первые применяются для прокатки листов и лент, а вторые – для сортового металла. Ручьи представляют собой кольцевые вырезы на поверхности валка. Совпадающие ручьи верхнего и нижнего валков образуют калибры, с помощью которых сортовому прокату постепенно придаются требуемые профили (рис. 4.26, а, б).
Рис. 4.28. Инструмент и оборудование прокатки: а) гладкий волок: 1 – бочка валка; 2 – шейка; 3 – треф; б) ручьевой валок; в) открытый и закрытый калибры; г) схема прокатного стана: 4 – рабочая клеть; 5 – шпиндель; 6 – шестерная клеть; 7 – редуктор; 8 – электродвигатель.
Прокатные станы классифицируются по ряду признаков, основным из которых является род выпускаемой продукции. В связи с этим можно выделить следующие наиболее распространенные виды станов: для получения полупродукта из слитков блюмов и слябов; заготовительные; сортопрокатные для выпуска из блюмов сортового проката; из слябом листовые и полосовые станы горячей прокатки; трубопрокатные станы; станы холодной прокатки стали и цветных металлов (тонколистовые, лентопрокатные, фольгопрокатные и т.д.); деталепрокатные станы для выпуска специального или периодического проката.
Холодная прокатка ленты из алюминиевых сплавов АМц, Д, Д16 производится из горячекатаных листов толщиной около 6мм. Ленту толщиной до 0,5-0,6мм катают без промежуточного умягчающего отжига. Заготовками для холодной прокатки лент из меди и латуни Л62 служат свернутые в рулоны полосы толщиной 5-6мм, полученные горячей прокаткой из слитков. Отожженные и протравленные рулоны прокатываются на специальных станах до толщины 0,01-0,2мм в течение четырех-пяти операций холодной прокатки, чередующихся умягчающими отжигами и травлением для удаления окалины.
Тонкие листы и ленту из меди или латуни получают холодной прокатной из горячекатаных заготовок толщиной 10-15мм с предварительно удаленными фрезерованием поверхностными дефектами. Прокатку ведут до требуемой толщины в несколько обжатий, применяя промежуточные отжиги при 450-800°С для восстановления пластичности металла.
Для холодной прокатки предпочтительнее однофазные латуни с содержанием цинка менее 30%, как обладающие большим запасом пластичности. Для предотвращения налипания меди и латуни на стальные валки применяют жидкую смазку (трансформаторное масло, керосин, веретенное масло и т. д).
4.3.2. Ковка и штамповка. При ковке деформирование металла заготовки осуществляется путем целенаправленно наносимых ударов или нажатий. В зависимости от используемого оборудования ковка делится на свободную и ковку в штампах (штамповку).
Сущность свободной ковки заключается в том, что происходящая формообразующая пластическая деформация металла осуществляется специальным инструментом. Придание заготовке требуемых формы и размеров осуществляется за счет выполнения ряда ковочных операций.
Горячая объемная штамповка. При штамповке требуемые формы и размеры заготовки получаются в результате принудительной деформации металла в ручье специального приспособления - штампа (рис. 4.29). Различают объемную штамповку в открытых и закрытых штампах. В открытом штампе (рис. 4.29, а) по периферии ручьяна стыке нижней 1 и верхней 2 частей штампа выполняется заусенечная канавка 3 для выхода избыточного металла, образующего удаляемый после штамповки заусенец, а в закрытом штампе (рис. 4.29, б, в) нет заусенечной канавки для выхода металла.
Рис. 4.29. Схемы штамповки в открытых и закрытых штампах.
Несложные заготовки штампуются в одноручьевых штампах, а сложные - в многоручьевых, в которых при переходе от ручья к ручью поковка постепенно приобретает требуемые размеры и форму. Исходные заготовки для штамповки отрезаются от сортового проката. Ими могут служить изделия периодического проката. Перед штамповкой металл нагревается до определенной температуры, зависящей от рода металла с целью повышения, его пластичности и уменьшения усилий при обработке. Свободная ковка и штамповка производятся с помощью специальных ковочных или штамповочных молотов и прессов.
Вследствие интенсивной теплоотдачи в атмосферу и теплопередачи в стенки ручья штампа происходит быстрое охлаждение заготовки, что приводит к наклепу и охрупчиванию ее металла. Во избежание образования трещин это требует дополнительных промежуточных нагревов цветных заготовок. При штамповке латуни следует иметь в виду, что при температуре выше 680°С из нее интенсивно возгоняется цинк в виде порошка ZnO. Это влечет изменение се химического состава и прочностных характеристик. Следует также учитывать, что при горячей штамповке латуни более хрупкая при комнатной температуре β-фаза оказывается пластичнее α-фазы. Поэтому для горячей штамповки однофазных латуней следует выбирать марки с предельным для α-латуней содержанием цинка - до 39%. После нагрева в результате α→β-превращения их структура состоит из α+β- или только β-зерен и имеет более высокую пластичность, чем у латуней с меньшим содержанием пинка, не претерпевающих α→β-превращений.
Ковка и штамповка дюралюминия производится при температуре около 380°С со степенями деформации соответственно 3-5 и 2-3%.
С целью экономии металла при обработке давлением осваиваются и внедряются более рациональные ее виды.
Так, в прокатном производстве применяются так называемые облегченные, тонкостенные, сложные, фасонные и другие экономичные профили проката. Прокаткой получаются экономичные профильные заготовки и изделия: шары, валы, зубчатые колеса, сверла, винты, различные виды периодического проката (для экономии металла при штамповке). Для производства машиностроительных профилей применяют еще методы прессования, волочения, а из листового материала получают изделия вырубкой, вытяжкой, формовкой, а прокаткой – гнутые профили.
Обработка металлов давлением – ОМД: разновидности и особенности технологии
ОМД, или обработка металлов давлением, возможна благодаря тому, что такие материалы отличаются высокой пластичностью. В результате пластической деформации из металлической заготовки можно получить готовое изделие, форма и размеры которого соответствуют требуемым параметрам. Обработка металла давлением, которая может выполняться по различным технологиям, активно используется для выпуска продукции, применяемой в машиностроительной, авиационной, автомобилестроительной и других отраслях промышленности.
Обработка листового металла давлением на прокатном станке
Физика процесса обработки металлов давлением
Сущность обработки металлов давлением состоит в том, что их атомы такого материала при воздействии на них внешней нагрузки, величина которой превышает значение его предела упругости, могут занимать новые устойчивые положения в кристаллической решетке. Такое явление, которым сопровождается прессование металла, получило название пластической деформации. В процессе пластической деформации металла изменяются не только его механические, но и физико-химические характеристики.
В зависимости от условий, при которых происходит ОМД, она может быть холодной или горячей. Различия их состоят в следующем:
- Горячая обработка металла выполняется при температуре, которая выше температуры его рекристаллизации.
- Холодная обработка металлов, соответственно, осуществляется при температуре, находящейся ниже температуры, при которой они рекристаллизуются.
Ковка раскаленной заготовки на молоте – вид горячей обработки металла давлением
Виды обработки
Обрабатываемый давлением металл в зависимости от используемой технологии подвергается:
- прокатке;
- ковке;
- прессованию;
- волочению; ; ;
- обработке, выполняемой комбинированными способами.
Основные виды обработки металла давлением
Прокатка
Прокатка – это обработка давлением заготовок из металла, в ходе которой на них воздействуют прокатные валки. Целью такой операции, для выполнения которой необходимо использование специализированного оборудования, является не только уменьшение геометрических параметров поперечного сечения металлической детали, но и придание ей требуемой конфигурации.
Виды прокатных валков
На сегодняшний день прокатку металла выполняют по трем технологиям, для практической реализации которых необходимо соответствующее оборудование.
Это прокатка, являющаяся одним из самых популярных методов обработки по данной технологии. Сущность такого способа обработки металла давлением заключается в том, что заготовка, проходящая между двумя валками, вращающимися в противоположные стороны, обжимается до толщины, соответствующей зазору между этими рабочими элементами.
По такой технологии обрабатывают давлением металлические тела вращения: шары, цилиндры и др. Выполнение обработки данного типа не предполагает, что заготовка совершает поступательное движение.
Это технология, которая представляет собой нечто промежуточное между продольной и поперечной прокаткой. С ее помощью преимущественно обрабатываются полые металлические заготовки.
Виды прокатки металла
Ковка
Такая технологическая операция, как ковка, относится к высокотемпературным методам обработки давлением. Перед началом ковки металлическую деталь подвергают нагреву, величина которого зависит от марки металла, из которого она изготовлена.
Обрабатывать металл ковкой можно по нескольким методикам, к которым относятся:
- ковка, выполняемая на пневматическом, гидравлическом и паровоздушном оборудовании;
- штамповка;
- ковка, выполняемая вручную.
При машинной и ручной ковке, которую часто называют свободной, деталь, находясь в зоне обработки, ничем не ограничена и может принимать любое пространственное положение.
Ручная ковка используется в кузнечных мастерских при изготовлении небольшого количества изделий
Машины и технология обработки металлов давлением по методу штамповки предполагают, что заготовка предварительно помещается в матрицу штампа, которая препятствует ее свободному перемещению. В результате деталь принимает именно ту форму, которую имеет полость матрицы штампа.
К ковке, относящейся к основным видам обработки металлов давлением, обращаются преимущественно в единичном и мелкосерийном производстве. Разогретую деталь при выполнении такой операции располагают между ударными частями молота, которые называются бойками. При этом роль подкладных инструментов могут играть:
- обычный топор:
- обжимки различных типов;
- раскатка.
Прессование
При выполнении такой технологической операции, как прессование, металл вытесняется из полости матрицы через специальное отверстие в ней. При этом усилие, которое необходимо для осуществления такого выдавливания, создается мощным прессом. Прессованию преимущественно подвергают детали, которые изготовлены из металлов, отличающихся высокой хрупкостью. Методом прессования получают изделия с полым или сплошным профилем из сплавов на основе титана, меди, алюминия и магния.
Прессование в зависимости от материала изготовления обрабатываемого изделия может выполняться в холодном или горячем состоянии. Предварительному нагреву перед прессованием не подвергают детали, которые изготовлены из пластичных металлов, таких как чистый алюминий, олово, медь и др. Соответственно, более хрупкие металлы, в химическом составе которых содержится никель, титан и др., подвергаются прессованию только после предварительного нагрева как самой заготовки, так и используемого инструмента.
Установка холодного прессования изделий из листового металла
Прессование, которое может выполняться на оборудовании со сменной матрицей, позволяет изготавливать металлические детали различной формы и размеров. Это могут быть изделия с наружными или внутренними ребрами жесткости, с постоянным или разным в различных частях детали профилем.
Волочение
Основным инструментом, при помощи которого выполняется такая технологическая операция, как волочение, является фильера, называемая также волокой. В процессе волочения круглая или фасонная металлическая заготовка протягивается через отверстие в фильере, в результате чего и формируется изделие с требуемым профилем поперечного сечения. Наиболее ярким примером использования такой технологии является процесс производства проволоки, который предполагает, что заготовка большого диаметра последовательно протягивается через целый ряд фильер, в итоге превращаясь в проволоку требуемого диаметра.
Технологические процессы получения проволоки методом волочения
Классифицируется волочение по целому ряду параметров. Так, оно может быть:
- сухим (если выполняется с применением мыльной стружки);
- мокрым (если для его выполнения используется мыльная эмульсия).
По степени чистоты формируемой поверхности волочение может быть:
Линия волочения медной проволоки
По кратности переходов волочение бывает:
- однократным, выполняемым за один проход;
- многократным, выполняемым за несколько проходов, в результате которых размеры поперечного сечения обрабатываемой заготовки уменьшается постепенно.
По температурному режиму этот вид обработки металла давлением может быть:
Объемная штамповка
Сущность такого способа обработки металла давлением, как объемная штамповка, состоит в том, что получение изделия требуемой конфигурации осуществляется при помощи штампа. Внутренняя полость, которая сформирована конструктивными элементами штампа, ограничивает течение металла в ненужном направлении.
В зависимости от конструктивного исполнения штампы могут быть открытыми и закрытыми. В открытых штампах, применение которых позволяет не придерживаться точного веса обрабатываемой заготовки, предусмотрен специальный зазор между их подвижными частями, в который может выдавливаться избыток металла. Между тем использование штампов открытого типа вынуждает специалистов заниматься удалением облоя, образующегося по контуру готового изделия в процессе его формирования.
Особенностью горячей штамповки металла является воздействие высокой температуры, вследствие чего заготовка деформируется, принимая форму штампа
Между конструктивными элементами штампов закрытого типа такой зазор отсутствует, и формирование готового изделия происходит в замкнутом пространстве. Для того чтобы обрабатывать металлическую заготовку при помощи такого штампа, ее вес и объем должны быть точно рассчитаны.
Листовая штамповка
При помощи листовой штамповки готовые изделия получают из листового металла. В зависимости от того, какого результата необходимо добиться в процессе выполнения такой технологической операции, различают штамповку:
- разделительную (отрезка, вырубка и пробивка);
- формообразующую (гибка, вытяжка, раздача, отбортовка, чеканка и др.).
Для выполнения листовой штамповки используют гидравлические или кривошипно-шатунные прессы, рабочими органами которых являются штампы, состоящие из матрицы и пунсона.
Примеры изделий, изготовленных методом листовой штамповки
Качество готового изделия, которое обеспечивает листовая штамповка, позволяет не подвергать его последующей механической обработке. Для того чтобы обеспечить это качество, матрица и пунсон должны быть хорошо разработаны и изготовлены с высокой степенью точности.
Листовая штамповка – это одна из наиболее распространенных методик ОМД, которая активно применяется почти во всех отраслях промышленности. По такой технологии, в частности, производят как мельчайшие детали радиоэлектронных устройств, так и массивные кузова автотранспортных средств.
Получить более полное представление о способах обработки металла давлением, позволяет видео, демонстрирующее их в мельчайших подробностях.
Читайте также: