Импульсная сварка нет дуги
Обновлено: 16.05.2024
«Сварка – процесс создания неразъёмного соединения в результате расплавления кромок, образования общей сварочной ванны и последующей её кристаллизации» - так звучит определение хорошо известного многим сварочного процесса.
Как известно, сварка в своём нынешнем виде была изобретена в 30-е – 40-е годы прошлого века. За столь долгий срок некогда простой процесс обрёл вид сложной технологической операции, на смену неплавящемуся угольному электроду пришла расходуемая сварочная проволока, трансформаторы уступили место электронике и инверторам, а качество соединений повысилось за счёт применения различной газовой и порошковой защиты.
В последнее время наибольшее распространение получила полуавтоматическая сварка плавящейся проволокой в среде защитных газов благодаря простоте использования, обширному диапазону свариваемых материалов и толщин, невысокой цене на оборудование при его малых габаритах и возможности автоматизации и роботизации. Многие сварщики как частники, мелкие конторки так и рабочие промышленных гигантов государственного масштаба остановили свой выбор именно на полуавтоматах, подчёркивая повышенный КПД (в сравнении с применяемой ранее ручной дуговой сваркой плавящимся электродом), неприхотливость в работе и значительное сокращение дефектов шва на выходе изделий.
Прогресс не стоит на месте, а значит и без того простые в применении аппараты для полуавтоматической сварки с каждым годом приобретают всё новые технологии по улучшению сварочного процесса и предотвращению возникновения дефектов и напряжений в сварочном шве.
Одной из таких технологий является возможность импульсной сварки.
Процесс создания сплошных сварных швов посредством расплавления металла с управляемым переносом «один импульс – одна капля» получил название импульсной сварки.
Используя импульсную дугу в виде источника тепла, можно существенно расширить возможности традиционной сварки в защитной газовой среде.
Импульсная MIG/MAG сварка представляет собой вариант обычного процесса сварки MIG/MAG, в котором ток пульсирует с частотой. Некоторые современные аппараты позволяют регулировать частоту импульса. Поскольку скорость подачи электродной проволоки не равна скорости её плавления, был введён дополнительный импульс для контроля переноса металла при работе на малых токах путем наложения импульсов высокого тока короткой длительности. Цикл состоит из применения многократного импульсного тока в течение постоянного фонового тока, что обеспечивает образование капли на конце электрода.
Электродинамические силы, резко увеличиваясь, сужают шейку капли, сбрасывая ее в сварочную ванну. В данном случае можно применять как одиночные, так и целую группу импульсов.
Стабильность всего MIG/MAG процесса напрямую зависит от соотношения длительности и величины импульсов и пауз между ними.
Методом подбора тока импульса и дуги можно ускорить плавку проволоки электрода, способствовать изменению формы и размеров сварочного шва. Наконец, можно уменьшить нижний предел сварочного тока, который отвечает за стабильность горения дуги.
Управляемый перенос металла помогает улучшить качество сварки. Данный метод является одним из самых лучших и эффективных. Во время осуществления импульсной сварки разбрызгивания совершенно отсутствуют, не образуются несплавления.
По сравнению со сваркой неплавящимся электродом импульсная сварка позволяет в 3—8 раз повысить производительность процесса и значительно снизить сварочные деформации при практически одинаковом качестве сварных соединений. Импульсная сварка может применяться для конструкций ответственного назначения из разных марок сталей, алюминиевых, медных, никелевых сплавов и титана толщиной от 1 до 50 мм при выполнении швов во всех пространственных положениях. Благодаря высокой пространственной стабилизации дуги и возможности применения вылета электрода большой длины этот процесс может быть успешно применен для сварки стыковых соединений толстолистовых материалов с узкощелевой подготовкой кромок.
Наибольшее распространение импульсная сварка получила для соединения алюминиевых сплавов толщиной ≥1,5 мм и специальных сталей толщиной > 1 мм.
Для каждого сварочного тока должны быть выбраны оптимальные частота и энергия импульсов. Частоту 50 Гц следует применять при малых токах, когда использование частоты 100 Гц невозможно. При токах свыше 70—100 А следует применять частоту 100 Гц, так как при частоте 50 Гц увеличивается чешуйчатость шва, его пористость и дымообразование.
Современные сварочные аппараты позволяют использовать широкий диапазон амплитуд импульсов различной длительности и формы волны на частотах от нескольких герц до нескольких сотен герц. Амплитуда и длительность импульса, объединённые должным образом, создают дугу, способную расплавить и отсоединять каплю электродной проволоки диаметром, близким к толщине этой проволоки.
Такая дуга в паузах между возбуждениями импульса не оказывает существенного влияния на глубину расплавления металла. За счет этого достигается устойчивое горение дуги в пространстве, улучшается качество сварки: отсутствует разбрызгивание расплавленного металла проволоки, целиком устраняются кратеры из сварных точек при уменьшении требуемых участков перекрытия в месте сварного шва. Выбор целесообразного отношения токов дуг (импульсной и дежурной) способен также значительно ускорить процесс сварки, но этот процесс является сложной операцией. Высота и длительность импульса зависят от состава проволоки, её диаметра и в меньшей степени от состава защитного газа.
Более всего для контроля параметров импульса подходят аппараты с синергетической системой управления. Такие аппараты позволяют не только настраивать основные параметры сварочного процесса: величину фонового и импульсного тока, времени их протекания, длину дуги и т.д., но и отталкиваться от предустановленных программ, рассчитанных специально под конкретные данные, как свариваемого материала, так и используемых «расходников»: состава газовой защиты и присадочной проволоки. Подобные настройки хорошо заметны на приведённых ниже изображениях меню аппарата CEA DIGITECH .
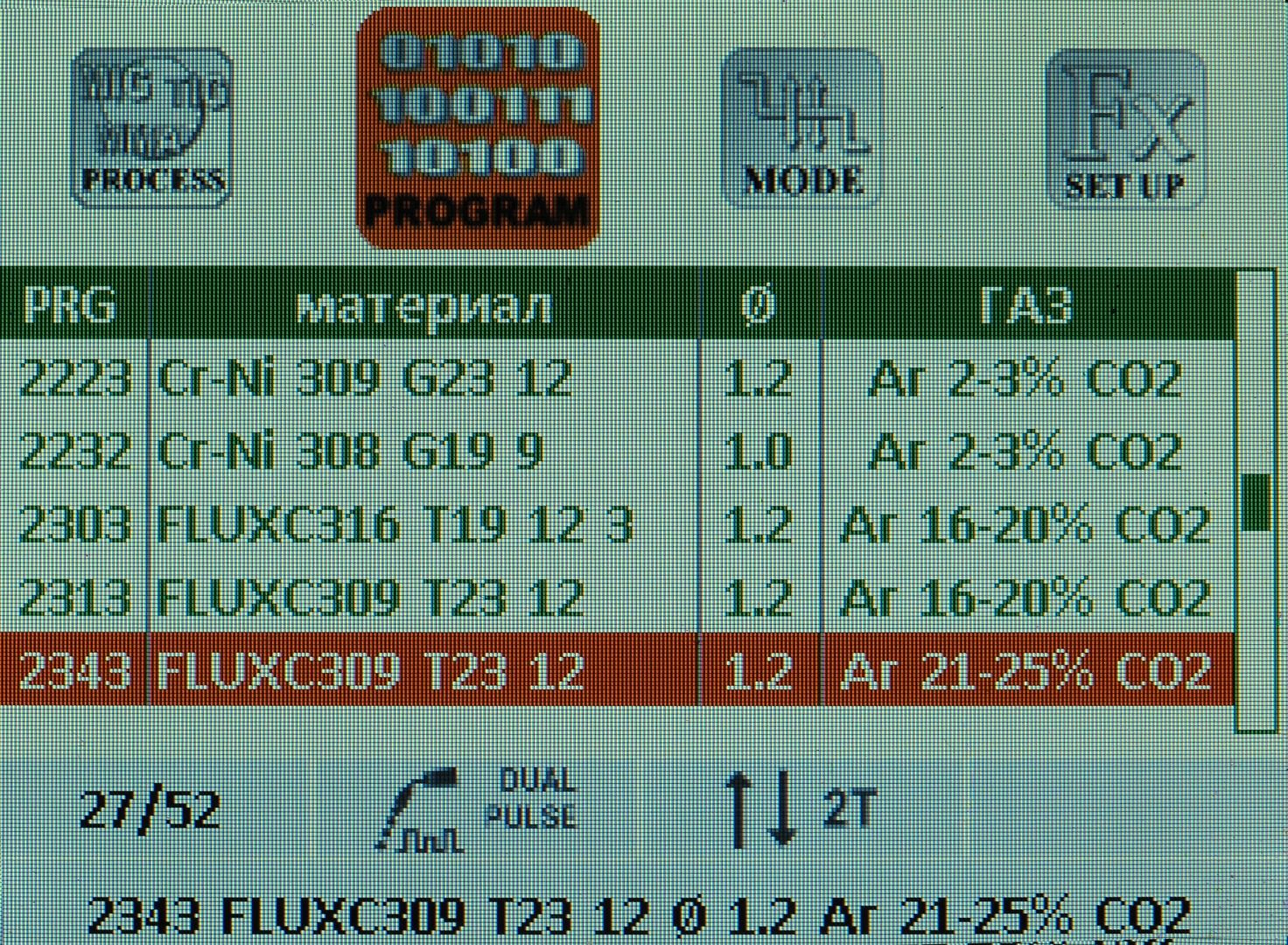
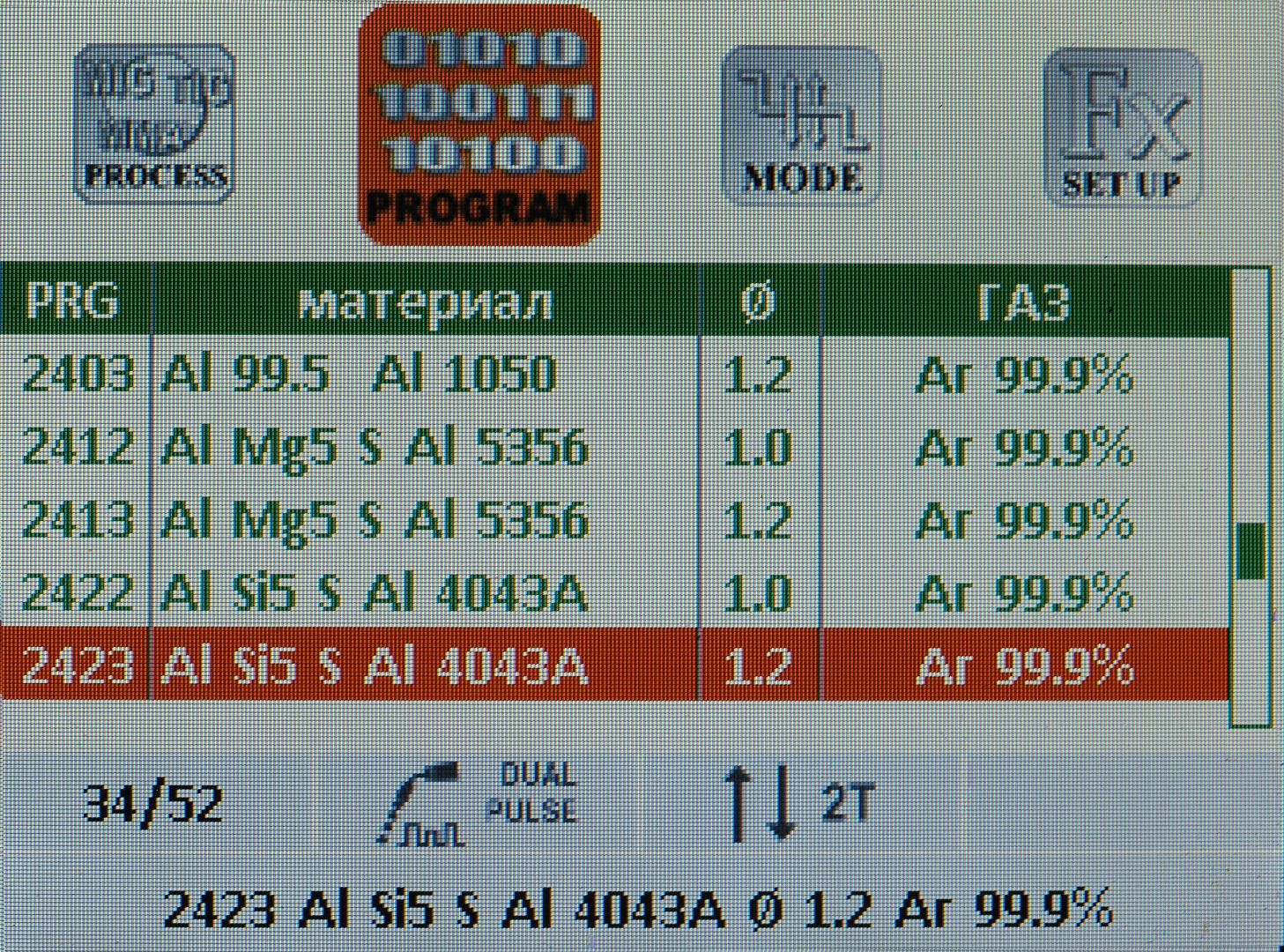
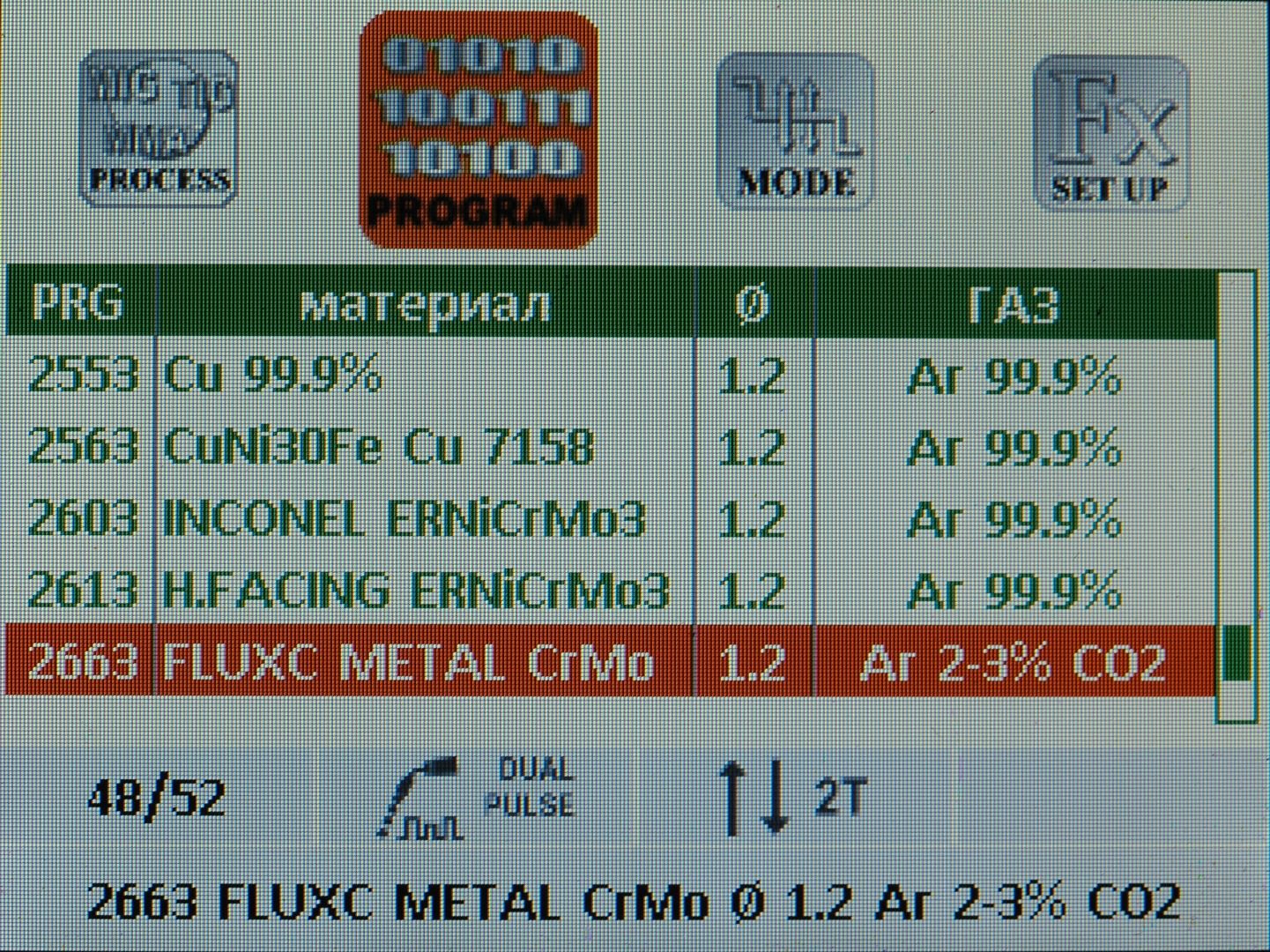
Меню выбора программ для сварки различных материалов аппарата DIGITECH
Основные преимущества импульсного режима MIG/MAG сварки:
• Она позволяет добиться плавной, без брызг сварки на средних токах (50-150A), которые иначе подходят только для сварки короткой дугой с непериодичной подачей металла в зону сварки и, как следствие, появление брызг металла.
• Импульсная передача является промежуточной между струйным переносом и сваркой короткой дугой, которая может быть слишком "холодной" (из-за прерывистого образования электрической дуги, дуга эффективно 'выходит' между каждым циклом плавления). Это делает его идеальным для сварки больших толщин, где необходим контроль тепловложения, но для которых струйный перенос будет уже слишком "горячим".
• Импульсный режим MIG сварки позволяет сваривать при более высоких скоростях там, где погружённая дуга или струйный перенос не применимы.
• Возможность перехода капельного переноса в мелкокапельный и струйный.
Двойной импульс
Сутью MIG/MAG процесса с двойными импульсами является модулирование высокочастотного несущего сварочного тока, вырабатываемого силовым инвертором, с низкочастотными импульсами, которые формируются вторичным инвертором. При этом существенно изменяется форма импульса и соотношения ток/пауза.
За счет изменения формы импульса и угла наклона фронта волны импульса появляется возможность получения управляемого мелкокапельного переноса в режиме короткого замыкания.
Режим короткого замыкания характеризуется плавным перетеканием капли с конца электродной проволоки в сварочную ванну.
Размер капли практически соответствует диаметру электродной проволоки, что позволяет уменьшить размер ванны жидкого металла и улучшить растекание капли в ванне. Уменьшение размера ванны ведет к правильному равномерному формированию обратного валика, повышая качество корневого прохода и улучшая условия сварки тонкого металла.
При работе с тавровыми швами двойной импульс тока позволяет получить шов с вогнутым катетом и избежать появления вероятных концентраторов напряжений в зоне сплавления.
Что касается системы настроек режима сварки, то она, прежде всего, зависит от назначения аппарата, цены и, если есть возможность, предустановленных программ, расширяющих функции. Так, аппарат СЕА DIGITECH , помимо наглядного интуитивно понятного меню, обладает гибкими настройками параметров сварки как импульсной, так и двойным импульсом на всех этапах процесса.
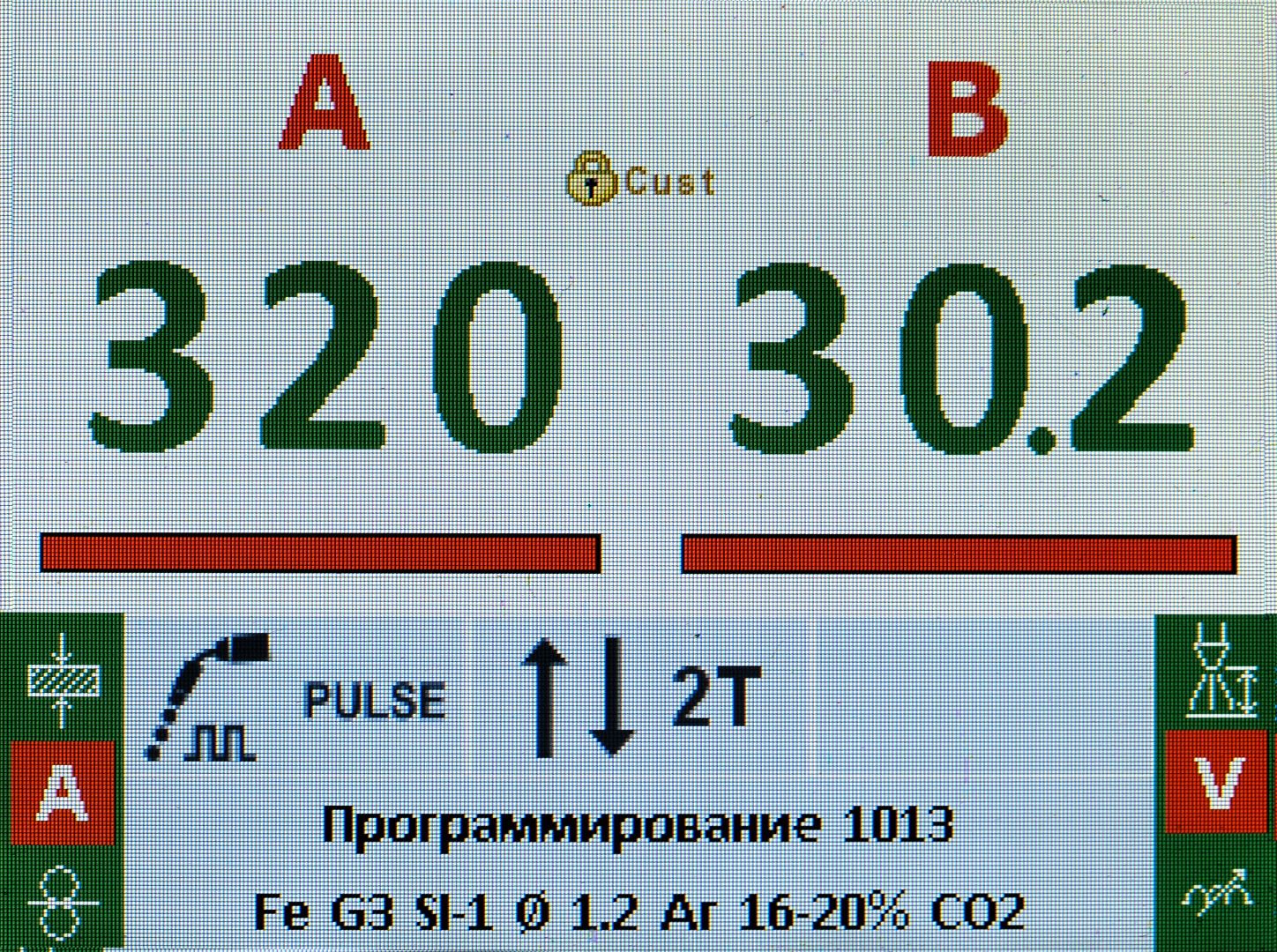
Регулировочные параметры отображены квадратами, настраиваемый параметр подсвечен зелёным.
Слева направо: предварительная подача газа, стартовая скорость, горячий старт, начальный ток, начальная длина дуги, начальное нарастание, конечное затухание, конечный ток, конечная длина дуги, растяжка дуги, послесварочный газ.
Диаграмма двойного импульса с настройками: первая модуляция (от I1 до I2), разность токов двойного импульса, длительность двойного импульса, баланс двойного импульса, частота двойного импульса, вторая модуляция (от I2 до I1).
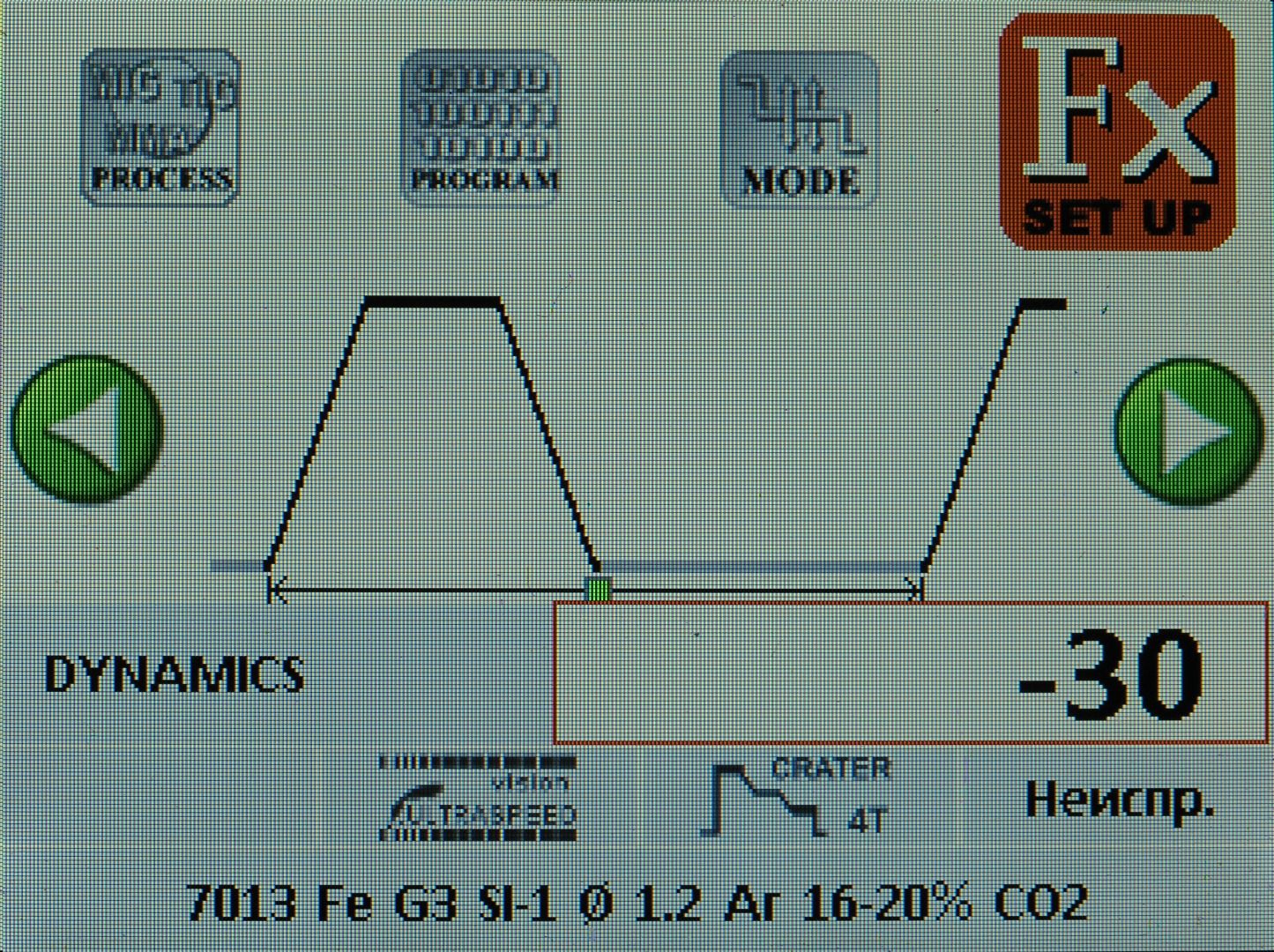
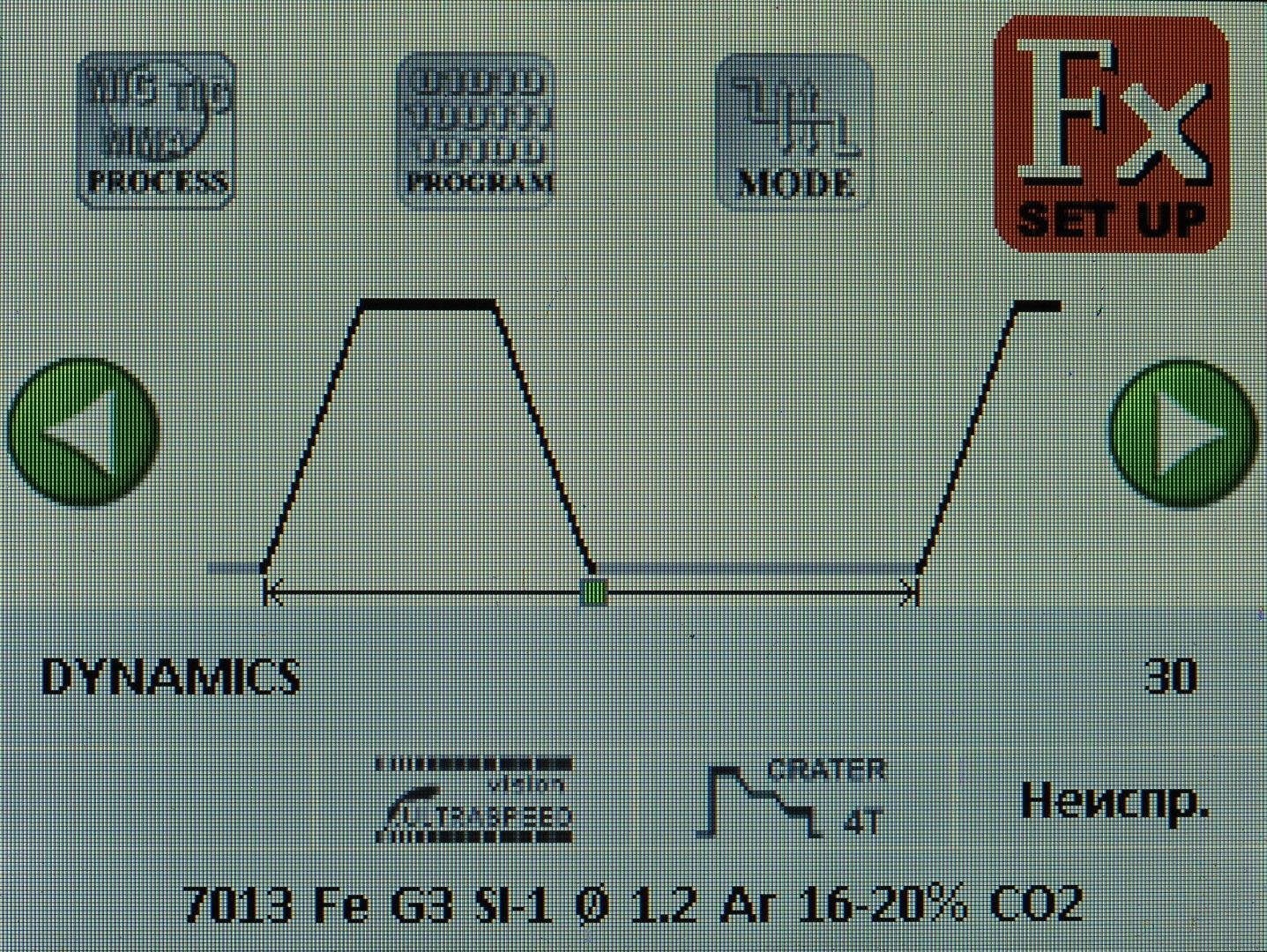
Регулировка динамики/частоты импульса для режима ULTRASPEED (специальная функция полуавтоматов СЕА).
В линейке СЕА следующие аппараты имеют возможность полуавтоматической сварки MIG / MAG с использованием импульса/двойного импульса: DIGISTAR 250 , DIGITECH VISION PULSE 5000 . C описанием аппаратов Вы можете ознакомиться, просто нажав на интересующую модель.
Что такое импульсная сварка и в чем преимущество этого метода?
Виды сварки
Сварочные технологии никогда не отстают от скоростей научно-технического прогресса. Новые методы, материалы или оборудование постоянно пополняют и без того широкий список всевозможных способов соединения металлов и неметаллов.
Импульсная сварка – один из новых методов, который уже нашёл самое широкое применение в монтаже современных мощных трубопроводов и строительстве: как промышленном, так и гражданском.
Особенности импульсной сварки
Этому виду сварки под силу соединение таких капризных металлов как сплавы меди, сталь и многие другие цветные сплавы, в том числе алюминиевые. Импульсная сварка отлично справляется со сложными стыковыми швами при соединении металлических заготовок с толстыми краями.
Исторически импульсная сварка была изобретена и разработана в качестве конкурентного метода электродуговой технологии, у которой имеются определенные недостатки с точки зрения производительности и качества сварочного шва.
Суть процесса
Принцип импульсной сварки.
Если коротко, то это процесс последовательного расплавления металла заготовки в определенных точках со следующим этапом в виде покрытия.
Главный элемент данного процесса — так называемая дежурная дуга невысокой мощности, которая продолжает работать в остановках между повторяющимися импульсами и передает импульсный ток лишь частично.
Эта дуга практически не влияет на металл между импульсами, она отлично и устойчиво горит в пространстве. Второе состояние этой же дуги – импульсное, которое плавит металл в точках приложения.
Соотношение токов от дуги в разном состоянии – импульсном и дежурном должно быть правильным, что может ускорить сварку и повысить качество шва.
Возможности классической дуговой сварки в среде защитных газов сильно расширяются, если металл плавится под воздействием импульсной дуги.
Главная ее особенность – специальный режим включения и выключения дуги, которая обусловлена программой в зависимости от природы металлов соединяемых заготовок, толщины их кромок и положения швов в пространстве.
Короткие импульсы производятся за счет энергии специального аккумулятора, который предварительно заряжается от электрической цепи. Главная технологическая особенность и преимущество метода – способность импульсной сварки формировать неразъемные соединения металлов с абсолютно разным составом.
Оборудование для импульсной сварки требуется особое – это особый специализированный — импульсный сварочный аппарат с определенными расходными материалами. Импульсный аппарат генерирует дозированные сварочные импульсы.
Расходными материалами являются разного рода электроды – плавящиеся и неплавящиеся.
В состав импульсного сварочника входят следующие элементы:
- выпрямитель низкочастотного характера;
- еще один выпрямитель высокочастотного характера;
- устройство сварочного инвертора;
- трансформатор;
- электронный блок управления – плато;
- рабочие шунты.
Два способа импульсной сварки определяются выбором и использованием электродов:
- с применением электродов неплавящегося вида;
- с применением плавящихся электродов с устранением недостатка процесса в виде разбрызгивания капель расплавленного металла.
Так или иначе это контролируемый повторяющийся процесс переноса расплавленного металла расходника в защитной среде газа.
Вот как это происходит:
- Капля расплавленного металла проволоки расходника отделяется и перемещается на заготовку под воздействием мощного импульса.
- Сразу же после этого сила сварочного тока падает до уровня, который может лишь поддерживать дугу – дуга становится «дежурной», малой мощности.
- Мгновенно начинается процесс остывания металла в сварочной ванне.
- Начинается точное повторение такого же цикла переноса капли под импульсом, с падением тока, остываем и т.д.
С точки зрения электрической составляющей процесса импульсной сварки в аппарате применяется трансформация сетевого напряжения в выпрямленное постоянное, после чего оно превращается в напряжение с высокой частотой.
Технические нюансы
До начала работы приёмник энергии нужно подключить к сети электропитания, чтобы зарядить его до нужного уровня. Сама импульсная сварка занимает совсем немного времени, так как используется энергия, имеющаяся в запасе в приемнике. Такую сварку вполне можно выполнить своими руками, она совсем не сверхсложная.
При этом способе отлично контролируется и минимизируется малоприятное явление в виде разбрызгивания капель расплавленного металла. Имеется прекрасная возможность производить сварочные швы высокого качества практически в домашних условиях.
Швы формируются вследствие расплавления отдельных порций металла с последующим покрытием.
Важнейший момент – правильное выставление режима импульсной и дежурной дуги. Если режим верный, процесс пройдет быстро, правильно и, самое главное, безопасно, без всяких кратеров в ответственных стыковых участках.
Импульсная сварка на постоянном токе
Жесткость режима является технологической особенностью данного метода. Все дело в длительности импульса. Если его поменять, изменятся все параметры сварки.
Одно из важных преимуществ – возможность контролировать и минимизировать кристаллизацию металла. Можно изменять форму сварочной ванны. Дополнительно можно контролировать и снижать риск деформации сварочного шва.
Данный метод часто применяется для соединения металла с толщиной краев свыше 3-х мм.
Классификация видов
Импульсная сварка подразделяется на четыре вида:
- конденсаторная
с применением аппаратов с огромным диапазоном силы тока. Отлично подходит для сварки алюминиевых деталей; - аккумуляторная
в которой используются устройства с щелочными аккумуляторами, отлично справляются с замыканиями в сети; - инерционная
с использованием кинетической энергии мощного маховика; - электромагнитная
с получением механической энергии с помощью магнитного поля. Элементы крепятся магнитными силами в сочетании с высоким давлением.
Алгоритм действий
Это один из самых лучших видов сварки в целом. Нет никакого разбрызгивания, не формируются несплавления, варить можно в любом положении, очень экономно расходуются электроды. Швы формируются исключительно качественными без каких-либо прожогов.
Схема конденсаторной сварки.
Принцип действия сварочного инвертора в сочетании с импульсной технологией следующий: перенос металла электрода в сварочную ванну с одновременным регулированием тока.
Все начинается с формирования капли металла на конце электрода, которая при повышении тока попадает в сварочную ванну. Теперь этот горячий момент должен смениться холодным этапом с остыванием металла. Так может происходить много раз.
Проволока электрода должна быть хорошо разогрета. Это особенно важно при низких значениях тока.
Импульсный сварочный аппарат является чрезвычайно универсальным устройством: его можно применять в том числе и в газовой среде, для соединения металлических деталей самой разной толщины и конфигурации.
Эти аппараты очень удобны в работе с понятными регулировками для грамотной и тонкой настройки. Обычно они снабжены неплохим программным сопровождением, что делает их еще более эффективными по всем критериям.
Главные достоинства метода
Преимущества импульсной сварки:
- Первым делом это великолепное качество сварочного шва. Сразу же заметим, что импульсные устройства – вещи весьма недешевые. Но они того стоят и обязательно окупят все затраты в будущем.
- Импульс варит все: от стали до алюминия.
- Нужен минимум дополнительных инструментов и расходных материалов.
- Нет разбрызгивания металла.
- Не бывает прожогов и несплавлений.
- Возможность контролировать дугу.
- Отличная возможность управлять процессом переноса металла.
- Экономный расход материалов, в том числе сварочной проволоки и электродов.
- Легкая чистка шва в конце.
- Легкость для исполнения даже новичками.
На сегодняшний день у данного метода есть лишь один конкурент по популярности и эффективности – это сварка полуавтоматом. Она отличается высокой производительностью и, что немаловажно, непрерывностью процесса.
Но серьезным недостатком является разбрызгивание металла, при котором теряется до 30% материала. Кроме потерь, эти брызги нужно чистить после сварки, что очень непросто и портит внешний вид сварочного шва. Сварка импульсом исключает такую беду.
Главная область применения метода – монтаж трубопроводов самого ответственного вида, где особенно важны прочность шва с крепко сформированным обратным валиком без финишной зачистки.
Недостатков у этого метода всего два:
- он не годится для больших сварочных площадей;
- всегда нужно серьезное охлаждение индуктора.
Микроимпульсная сварка
Представьте себе, этот метод нашел отдельное и очень широкое применение в стоматологии — протезировании зубов. Речь о микросварке с использованием титана в виде тонких листов. Специальный микроимпульсный аппарат способен сваривать дентальные сплавы, в том числе титановые.
Качество таких швов нисколько не уступает лазерному стоматологическому аппарату, зато стоимость его значительно ниже. По этой причине они весьма популярны в небольших стоматологических клиниках.
Импульсный сварочник своими руками
Устройство сварочного аппарата вполне позволяет сделать его в домашних условиях для бытового применения. Составные части легко купить, здесь нет никаких проблем. Но не нужно забывать о некоторых нюансах.
Особый фокус – на транзисторах, потому что они быстрее всего ломаются и выходят из строя. На них не экономить, а покупать четыре транзистора высокого качества.
Перед тем, как приступить к работе, нужно обдумать и высчитать силу сварочного тока и мощность устройства. Примеров с подобными расчетами огромное количество в сети, они могут помочь с выработкой верного решения.
Как влияет циклограмма на процесс настройки аппаратов TIG?
Сварка — это технологический процесс, в котором необходимо учитывать большое количество параметров и факторов. Наибольший контроль за сварочными характеристиками необходим при аргонодуговой сварке TIG неплавящимся электродом в среде защитных инертных газов. Поэтому для упрощения контроля за рядом параметров в сварочных инверторах используется циклограмма.
С помощью циклограммы сварщик задает необходимые параметры сварки, чтобы процесс не вызывал сложностей, а также для предотвращения различных дефектов. Рассмотрим циклограмму сварочного аппарата ПТК МАСТЕР TIG 200 P AC/DC D92.
Каждый параметр циклограммы важен, поэтому для получения качественных сварных соединений необходимо понимать, для чего он нужен и как его настроить. Давайте поподробнее разберем каждый из них.
Время подачи газа перед сваркой
Это параметр, при котором увеличивается время задержки срабатывания высокочастотного осциллятора, при этом газовый клапан в аппарате находится в открытом положении, тем самым подавая защитный газ в горелку. Обычно имеет диапазон регулировки от 0,1 до 10–15 секунд. Регулировка этого параметра позволяет выгнать из всех каналов аргонодуговой горелки лишний кислород для того, чтобы он не попал в зону сварки и не наполнил сварочный шов парами, т.к. инертные газы тяжелее воздуха и вытесняют кислород из зоны сварки.
Совет. Рекомендованное значение времени подачи газа от 1,0 до 2,0 секунд. Этого вполне достаточно, чтобы выгнать воздух из всех каналов и не расходовать защитный газ понапрасну.
Стартовый ток
Параметр, который позволяет установить сварочный ток в начале сварки. Равномерно прогревает свариваемые кромки металла для получения сварочной ванны и последующего введения присадочного прутка. Обычно имеет диапазон 5–15 Ампер до максимального значения сварочного тока аппарата.
Время нарастания тока
Параметр, с помощью которого можно контролировать время изменения сварочного тока со стартового до основного (пикового) тока. Параметр имеет особое значение при сварке толстого металла, когда кромки уже разогреты, но силы сварочного тока не хватает для того, чтобы получить сварочную ванну. Диапазон регулировки от 0,1 сек до 10–15 секунд.
Пиковый ток
Или основной ток для сварки дугой без импульса — это основной сварочный параметр, который формирует сварочную ванну и сварочный шов. При сварке импульсной дугой – это верхний предел сварочного тока, так же формирующий сварочной шов. Обычно имеет диапазон от 5–15 Ампер до максимального значения сварочного тока аппарата.
Совет. Стартовый ток лучше установить больше пикового (основного) тока на 10–20 Ампер, чтобы быстро сформировать сварочную ванну без дальнейшего перегрева основного металла. Время спада тока лучше установить от 1,5 до 2,0 секунд, чтобы долго не греть металл и не получить прожог.
Базовый ток
Показатель, который в сочетании с пиковым током дает импульсную дугу с определенной частотой, которую можно регулировать. Базовый ток устанавливает нижний предел импульса. Используется при сварке тонколистового металла для предотвращения перегрева, выгорания легирующих элементов, прожогов и короблений. Базовый ток позволяет удержать сварочную ванну от провала и от прожога. Стандартный диапазон регулировки от 5–15 Ампер до максимального значения сварочного тока аппарата.
Этот параметр будет активен только в режиме AC Pulse и DC Pulse, т.е. при сварке импульсной дугой, в других режимах данный параметр работать не будет.
Время снижения тока
С помощью времени снижения тока можно контролировать время изменения сварочного тока основного (пикового) до тока заварки кратера. Имеет диапазон регулировки от 0,1 до 10–15 секунд. В течение этого времени ток будет плавно снижаться для того, чтобы в конце сварочного шва не образовался кратер.
Ток заварки кратера
Параметр, который позволяет установить ток для завершения процесса сварки. Диапазон от 5–15 Ампер до максимального значения сварочного тока аппарата. Позволяет завершить сварку без образования кратера.
В режиме работы горелки 2Т спад тока и заварка кратера начинается после отпускания кнопки, в режиме 4Т кнопку необходимо зажать до погашения дуги.
Время подачи газа после сварки
Параметр, при котором высокочастотный осциллятор отключается, при этом газовый клапан в аппарате находится в открытом положении, тем самым подавая защитный газ в горелку. Диапазон регулировки от 0,1 до 10–15 секунд. Регулировка этого параметра позволяет охладить горелку и свариваемое изделие.
Дополнительные сварочные параметры
Рекомендуем обратить внимание на сварочные параметры, которые применимы только в определенных режимах:
1. Баланс полярности переменного тока в режиме AC и AC Pulse
Полярность тока сварки существенным образом сказывается на характере протекания процесса аргонодуговой сварки. При использовании обратной полярности процесс сварки TIG характеризуется следующими особенностями:
- Сниженный ввод тепла в изделие и повышенный в электрод (поэтому при сварке на обратной полярности электрод должен быть большего диаметра при одном и том же токе. Иначе он будет перегреваться и быстро разрушится.
- Зона расплавления основного металла широкая, но неглубокая.
- Наблюдается эффект катодной чистки поверхности основного металла, когда под действием потока положительных ионов происходит разрушение окисной и нитридной пленок (катодное распыление), что улучшает сплавление кромок и формирование шва.
При сварке на прямой полярности наблюдается следующее:
- Повышенный ввод тепла в изделие и сниженный в электрод.
- Зона расплавления основного металла узкая, но глубокая.
Совет. При сварке алюминия на переменном токе, на кончике вольфрамового электрода необходимо образовать шарик, диаметром не более ½ диаметра электрода.
Чтобы образовать шарик на конце электрода необходимо:
- Выставить регулировку так, чтобы баланс полярности переменного тока был 50/50. На аппарате ПТК МАСТЕР ПТК МАСТЕР TIG 200 P AC/DC D92 показатель равен (65+15)/2=40. 40% — баланс отрицательной полуволны и положительной полуволны одинаков.
- Выставить баланс полярности в положение 45–50. На этом режиме шарик образуется в заданных значениях диаметра. Если вы выставите баланс полярности больше, то положительная полуволна увеличится, электронов потечет больше, на вольфраме начнет увеличиваться шарик.
- После образования шарика рекомендуем вернуть баланс полярности в исходное положение.
2. Частота переменного тока (режим AC и AC Pulse)
Этот параметр влияет на тепловложение в металл, на стабильность горение дуги, на глубину проплавления и ширину зоны очистки. Чем больше частота переменного тока, тем стабильнее горение дуги, более узкий сварочный шов, меньше тепловложение в изделие. Применяется при сварке тонколистового металла, где требуется стабилизировать дугу и уменьшить тепловложение. Чем меньше частота переменного тока, тем шире сварочный шов, больше зона очистки и больше провар. Применяется при сварке толстого металла.
3. Частота импульса (режим DC Pulse и AC Pulse)
Этот параметр влияет на тепловложение в металл, на стабильность горение дуги и на глубину проплавления. Чем больше частота импульсов тока, тем чаще пиковый ток будет спадать до базового и наоборот — базовый ток подниматься до пикового. Это обеспечивает стабильное горение дуги, узкий сварочный шов и меньшее тепловложение в изделие.
Применяется при сварке тонколистового металла, где требуется стабилизировать дугу и уменьшить тепловложение. Чем меньше частота переменного тока, тем реже пиковый ток будет спадать до базового и наоборот – базовый ток подниматься до пикового, следовательно, шире сварочный шов, больше зона очистки и больше провар. Применяется при сварке толстого металла.
4. Скважность или заполнение импульса в режиме DC Pulse и AC Pulse
Этот параметр схож по физическому смыслу с балансом полярности переменного тока. Однако, скважность импульса регулирует не положительную или отрицательную полуволну, а регулирует длительность пикового и базового тока в цикл длительности импульса.
Пример: Если частота импульса 50 Гц, что соответствует 20 мс, а базовый и пиковый ток — 50 и 100 Ампер соответственно, то при скважности импульса 50%, 10 мс ток будет 100 Ампер, а оставшиеся 10 мс — 50 Ампер, если скважность импульса составит 75% — 15 мс будет ток 100 А, а 5 мс – 50 мс.
Исходя из вышесказанного, чем выше скважность импульса, тем больше длительность пикового тока и выше тепловложение в металл, шире сварочная ванна. Чем меньше скважность — тем меньше тепловложение, стабильнее дуга, у́же сварочная ванна.
Запомните, что внимательное отношение к настройкам сварочных параметров поможет избежать дефекты и трудности при аргонодуговой сварке TIG. В качестве рекомендации ниже приведена таблица, в которой сделан акцент на важные моменты настройки параметров сварки. Таблица носит ознакомительный характер и не служит руководством к действию.
Ремонт сварочного инвертора своими руками
Сварочный аппарат является неотъемлемым инструментом при проведении монтажных работ, где задействован металлопрофиль. На смену тяжелым трансформаторным пришли инверторные сварочники. Они имеют небольшой вес и более мобильны, поэтому полюбились многим мастерам. Во время эксплуатации могут происходить типичные и нетипичные поломки, поэтому важно знать, можно ли провести ремонт сварочного инвертора своими руками. Что для этого нужно и как проходит процесс устранения неполадок, будет рассмотрено в этой статье.
Чем отличается сварочный инвертор
Инверторный сварочный аппарат получил свое название в силу того, какие в схеме происходят преобразования. Сетевой ток, который поступает в него имеет частоту в 50 Гц, это означает, что импульс изменяется 50 раз в секунду. На выходе из инверторного сварочника частота тока близка к постоянному, т. е. происходит процесс выравнивания. Чтобы добиться этого применяется несколько модулей, которые собраны в одну или несколько схем. На входе находится первичный блок, который производит выравнивание, он состоит из диодного моста. После предварительного выпрямителя ток попадает на блок инвертора. Здесь в дело вступают транзисторные ключи, он обеспечивают преобразование постоянного тока в высокочастотный, максимальное его значение достигает 100 кГц.
Высокочастотный ток поступает из транзисторной сборки на трансформатор. В этом блоке монтируется высокочастотный трансформатор, который понижает напряжение. При этом производится повышение силы тока, что важно для нормального горения электрода. В отдельных моделях инверторный сварочных аппаратов сила тока на выходе может достигать 300 ампер. Заключающим модулем является еще один выпрямительный модуль, после которого ток уходит к электродам. Этот модуль также собран на диодном мосте. При этом используются полупроводники большой мощности. Кроме основных элементов, есть и дополнительные, например, вся электроника нуждается в постоянном охлаждении, поэтому предусмотрен высокооборотистый вентилятор, который обеспечивает воздухообмен.
Причины неисправностей
Львиная доля поломок инверторных сварочных аппаратов приходится на неправильную их эксплуатацию. В некоторых случаях инверторный сварочный аппарат может храниться в ненадлежащем помещении, где есть повышенная влажность. Если она попадает на электронику, то это приведет к замыканию компонентов и выходу их из строя. Также не стоит использовать сварочный инверторный аппарат во время дождя или сразу после него. Каждый инверторный сварочный аппарат рассчитан на номинальную нагрузку и ее превышение может привести к выходу из строя силовых модулей. Такая причина может, например, крыться в обработке металла большой толщины высокими токами. Это приведет к перегреву и прогоранию транзисторных сборок или других элементов.
Большинство инверторных сварочных аппаратов отлично справляются с пониженным напряжением, но в некоторых случаях оно может стать причиной выхода из строя одного из модулей. Стоит помнить, что при пониженном напряжении мощность инверторного агрегата также падает, что понижает его КПД, т. к. часть мощностей расходуется на повышение тока на выходе. В некоторых случаях причиной поломки может стать некачественное закрепление рабочего или подводящего кабеля. Если контакт ненадежный, тогда в этих узлах возникает перегрев, из-за которого также возможно возникновение замыкания. Недостаточное охлаждение в силу выхода из строя вентилятора или прикрытия вентиляционных отверстий также приводит к выходу из строя схемы.
Обратите внимание! Агрегаты могут выходить из строя снова после того, как был произведен ремонт сварочных инверторов. Это связано с применением некачественных комплектующих. Их всегда стоит заказывать у проверенных продавцов, которые занимаются оптовыми поставками.
Распространенные неисправности
Существует ряд неисправностей, с которыми сталкиваются при работе с инверторным сварочным аппаратом. Они устраняются довольно просто, поэтому на них стоит остановиться подробнее.
Неустойчивая дуга
Неустойчивость дуги у инверторного сварочного аппарат может проявляться в разбрызгивании металла или прожигании обрабатываемой поверхности. Причиной тому является неверный подбор силы тока на выходе для толщины конкретного металла и электрода. Некоторые производители электродов указывают на упаковках, какой ток может быть применен для конкретного электрода. Подходящее значение можно выбрать экспериментальным путем, просто покрутив ручку в меньшую сторону. Если есть уверенность в правильности показаний тока на выходном дисплее инверторного сварочного аппарата, тогда можно воспользоваться таблицей, которая приведена ниже.
В некоторых случаях может наблюдаться частое прилипание электрода к заготовке. Такое явление обычно наблюдается у новичков, которые не имеют достаточного опыта работы с инверторным сварочным аппаратом. Но есть и другая причина такого процесса, она заключается в пониженном напряжении на входе. При этом агрегат не способе выдать требуемую силу тока для конкретного электрода, он разогревается и просто прилипает, а дуга даже не начинает горение. Также стоит проверить надежность подключения рабочих кабелей. В некоторых случаях плохой контакт может стать причиной прилипания электрода к поверхности заготовки.
Устранить недостаток можно чисткой байонетных креплений рабочих кабелей. Для этого можно воспользоваться растворителем или мелкой наждачной бумагой. Важно проверить удлинитель, которым сварочный агрегат подключен к сети питания. Если сечение проводника заужено, то оно может быть причиной падения напряжения. Выявить это можно по нагреву кабеля. Обычно для таких целей подбирается удлинитель с сечением кабеля не меньше 2,5 мм2. Также стоит помнить, что при длине свыше 30 метров на проводниках наблюдаются потери, поэтому необходимо либо большее сечение, либо меньшая длина. Еще одной причиной прилипания электрода является качество и подготовка заготовок для сваривания. Если на них есть большое количество ржавчины, тогда перед работой ее лучше счистить шлифовальной машинкой. Ниже приведена таблица, которая позволит подобрать сечение провода и номинал автомата для конкретной силы тока сварочника.
Нет тока на выходе
Проблема может проявляться в том, что питание в сети есть, а тока на выходе из инверторного агрегата нет, хотя все сигнальные огни могут светиться. В этом случае стоит обратить внимание на состояние агрегата. Если на панели управления загорелась лампочка рядом с пиктограммой термометра, тогда аппарат просто перегрелся. Поэтому стоит выждать время, пока вентилятор достаточно охладит внутренние компоненты. Важно внимательно осмотреть рабочие кабеля, если на них есть следы перебития или сильного изгиба, то такую проблему сразу стоит локализовать, заменив кабель или вырезав поврежденную часть.
Внезапное выключение
Другой неприятной неисправностью, которая может возникнуть во время ответственного процесса, является произвольное выключение сварочного агрегата. Проблема может заключаться не в самом сварочном аппарате, а в автоматическом выключателе, который установлен в сети питания. При превышении допустимой силы тока при потреблении он срабатывает, прекращая подачу. В некоторых случаях из строя может выйти предохранитель самого сварочного агрегата. Это происходит из-за резких всплесков в сети питания. Жучок можно поставить, если задача срочная, но лучше заменить предохранитель на новый.
Внезапное отключение может произойти и после продолжительной работы. Это может говорить о несоблюдении режима сварка-отдых. Если это так, то срабатывает температурный датчик, который просто прекращает подачу в силу перегрева. Насильно работу продолжить не удастся, поэтому потребуется выждать период остывания.
Другие неисправности
Есть и другие поломки, которые не имеют внешних проявления. Для их выявления есть общий алгоритм, которого следует придерживаться. Первым делом сварочный агрегат осматривается визуально. Выявляются повреждения корпуса, а также следы прогаров, которые могут возникнуть при коротком замыкании. Далее зажимаются все разъемные соединения и проверяются регуляторы и выключатели. Инспектируется предохранитель сварочного агрегата. Он не всегда имеет вид прозрачной колбы с нитью. Если проблема не была устранена, тогда потребуется дальнейший осмотр после разборки. Металлический корпус демонтируется, чтобы был доступ к внутренним компонентам. Их также необходимо осмотреть визуально.
Неисправные элементы, обычно, сразу бросаются в глаза. Это могут быть вспухшие конденсаторы или расплавившиеся элементы. Стоит обратить внимание на потемнения, которые есть на плате. В некоторых случаях элемент внешне может выглядеть нормально, но на самом деле быть неисправным. Далее проверяется наличие напряжений, которые должны быть на схеме. Проверяется наличие напряжение на входе и после каждого блока. Для этого понадобится качественный мультиметр, который способен выдерживать большие токи. Когда выявлен виновный блок, необходимо произвести прозвонку и замеры каждого отдельного элемента, чтобы вычислить виновника. В этом отношении самым доступным и простым может оказаться ремонт сварочного инвертора Ресанта. На сварочники фирмы Ресанта 220 и другие есть много схем в свободном доступе, по которым можно определиться со строением. Несколько видео о ремонте инверторного агрегата можно посмотреть ниже.
Резюме
Самостоятельный ремонт инверторного сварочного аппарат подразумевает наличие основных знаний по схемотехнике, электронике и законами физики. В противном случае будет сложно разобраться с основными компонентами и причинами их выхода из строя. В большинстве случаев выход из строя каких-либо компонентов инверторного сварочника обусловлен неисправностью других компонентов, которые явно не проявляют недостатков.
Читайте также: