Ультразвуковая сварка золотой проволоки
Обновлено: 20.09.2024
Золото и алюминий имеют хорошую взаимную свариваемость при отсутствии толстых оксидных пленок на алюминии. Однако при микросварке золотой проволоки на алюминиевую подложку (либо алюминиевой проволоки на позолоченную подложку) в месте контакта двух различных металлов возникают интерметаллические соединения золота и алюминия. Эти интерметаллические соединения обладают свойствами, отличными от свойств золота и алюминия, что приводит к термодинамической неустойчивости сварных отпечатков. Интерметаллические соединения появляются уже в процессе формирования сварного соединения как при термокомпрессионной сварке, так и при ультразвуковой сварке, и продолжают расти при повышенной температуре в процессе технологических обработок и эксплуатации приборов.
Основными образующимися соединениями являются Au5Al2 («белая чума») и AuAl2 («пурпурная чума»), которые образуются при высоких температурах. Белой чумой называют как само соединение Au5Al2, так и собственно проблему, которую оно вызывает. Это соединение имеет низкую электропроводность, поэтому его образование на стыке металлов приводит к увеличению электрического сопротивления, что может привести к отказу. Пурпурная чума (также ещё известная под названием «пурпурная смерть» или «пурпурное золото») является хрупким, ярко-пурпурным соединением AuAl2, состоящим из около 78,5% Au и 21,5% Al по массе. AuAl2 является наиболее термически стабильным из интерметаллических соединений Au – Al, с температурой плавления 1060°C, сравнимой с температурой плавления чистого золота.
]Процесс роста интерметаллических слоев вызывает уменьшение объема и, следовательно, создает полости (разрывы) в металле около границы раздела между золотом и алюминием. В результате проволока по всему периметру сварочного отпечатка электрически отключается от подложки, а спустя некоторое время происходит и механическое отслоение. Когда электрическое отключение уже произошло, а механическая прочность ещё имеется, этот дефект очень трудно обнаружить (отсюда, видимо, возникли и такие названия — «чума», «смерть»). Иногда достаточно подать на такое полуразрушенное соединение импульс тока, например в процессе измерения, чтобы оно временно восстановилось.
Другие золото-алюминиевые интерметаллические соединения также могут вызывать проблемы с качеством микросварки. При температуре ниже 624°C пурпурная чума заменяется Au2Al, веществом коричневого цвета. Это плохой проводник, приводящий как к электрическим, так и к механическим отказам. При более низких температурах, около 400–450°C, на стыке металлов происходит взаимный процесс диффузии. Это приводит к образованию слоев из нескольких интерметаллических соединений различного состава, от богатого золотом до богатого алюминием, с разной скоростью роста. В результате происходит возникновение пустот по мере того, как более плотные, быстрорастущие слои поглощают более медленно растущие. Этот процесс, известный как опустошение по Киркендаллу, приводит как к увеличению электрического сопротивления, так и к механическому ослаблению проволочного соединения.
Образование интерметаллических соединений в контактах золота с алюминием происходит уже при температуре 100 ºС. В начальный момент времени образуются кристаллы Au2Al, позже появляется фаза AuAl2, а при дальнейшей выдержке фаза Au2Al уменьшается, пока в образце не остаются кристаллы пурпурного цвета AuAl2. Процесс завершается более чем за 150 ч. Пурпурный цвет соединений золота с алюминием связан с образованием исключительно фазы AuAl2. В результате взаимодействия контактирующих пленок золота и алюминия при температуре 150 °С и выше при соотношении толщин δAu/δAl = 3 кристаллов «пурпурной чумы» не обнаружено.
Установлено, что соотношение размеров проволоки и пленки влияет на качество сварных соединений. Например, если отношение ширины деформированной части алюминиевого вывода к толщине золотой пленки больше чем 4 сопротивление контакта изменяется незначительно. Таким образом, выбором соотношения толщин свариваемых материалов можно повышать надежность соединений.
Деградацию сварных соединений системы Al-Au можно существенно уменьшить легированием золотой пленки Pd и Ag, а также алюминиевой проволоки 1-2 % Pd или 1 % Be. Загрязнения золотой металлизации примесями Pb, Zn, Та, Те, S, Co, Fe и т. д. значительно ускоряют диффузионные процессы в сварных соединениях. Отрицательное действие оказывает на деградацию сварных соединений и загрязнение поверхностей соединяемых элементов органическими веществами типа смолы и т. п.
Ультразвуковая микросварка | Сварить или склепать? ➔ часть I
Каждый год в мире производится более четырёх триллионов проволочных соединений, выполненных ультразвуковым методом в полупроводниковых приборах. Несмотря на свою долгую 60‑летнюю историю, этот нелепый «бондинг» по-прежнему используется в пятидесяти миллиардах ежегодно выпускаемых интегральных схем и бесчисленных дискретных приборах. Каждые десять лет появляется очередная технология — «убийца УЗ-сварки».
После оваций, статей и вручения премий за инновации (и банальной раскрутки промышленных гигантов на финансирование НИОКР) подобное новое изобретение благополучно дополняет имеющийся арсенал, а сотни тысяч установок продолжают мирно вышивать узоры из драгоценных нитей. Понимание основ процесса по-прежнему актуально для специалистов отрасли и останется таковым еще долгие годы, наряду с С4, FC, TAB, TSV и другими методами интеграции полупроводниковых компонентов в современном корпусировании.
В отличие от механических процессов («отсюда взять–туда положить») и чистой физики («нагреть–припаять») присоединение выводов ультразвуком всегда считалось непонятной и сложной операцией, в ней всегда было немного магии. Почему необходимо понимать, как протекает процесс соединения проволоки и контактной площадки? Каким образом при минимальной деформации обеспечить максимальную надёжность контакта? Есть ли чёткие критерии выбора частоты для работы с тем или иным материалом? Многие предприятия пробуют перевести свой процесс сварки с традиционных 60 на 100 или 140 кГц, экспериментируют с новыми материалами и режимами, но часто сталкиваются с неоднозначными результатами. Поэтому понимание физических основ процесса по-прежнему важно. В преддверии выхода на российский рынок нового (шестого) поколения автоматов ультразвуковой сварки своим опытом готовы поделиться эксперты F&K Delvotec Bondtechnik — производителя первой в мире автоматической установки проволочных выводов.
Илья Корочкин — Глобал Микроэлектроника, Россия
Сергей Валев — CEO i.V.tec electronics, Россия
Краткое описание процесса:
Как можно перемешать металлы без плавления и где взять лишнее время, если не успел этого сделать.
Вероятно, нелишне напомнить, какие стадии процесса существуют при формировании сварного соединения, и представить его современную физическую модель. На рис. 1–3 схематично показаны три стадии формирования соединения методом «клин-клин». При этом рассмотренные далее базовые принципы справедливы и для более громоздкого в описании метода «шарик-клин».
В момент соприкосновения проволоки с поверхностью контактной площадки (подложки) начинается передача колебаний пьезопреобразователя в точку контакта инструмент-проволока-подложка с амплитудой порядка нескольких микрометров (1–2 мкм для тонкой и 3–5 мкм для толстой проволоки).
Важно отметить, что пара проволока-инструмент на этой стадии колеблется синхронно, как единая система. Таким образом, физическое перемещение (притирка) происходит только по границе проволока — контактная площадка.
Для стабильной передачи колебаний в этой системе крайне необходимо отсутствие случайных проскальзываний проволоки в инструменте, то есть трение в паре инструмент-проволока должно быть намного выше, чем в паре проволока-подложка. Для этого нижняя поверхность инструмента должна слегка деформировать проволоку, «впечатываясь» в неё. В регулируемых настройках оборудования любого производителя найдётся «сила прижима» (Bond Force). Как будет показано ниже, это самый важный параметр при формировании соединения, который подбирают для конкретного типа проволоки, ее диаметра и характера подложки.
Следует подчеркнуть, что эта первая фаза процесса уже создаёт предпосылки для получения того или иного результата:
- Насколько точно оборудованием определён момент контакта с подложкой? Поскольку от момента касания начинается отсчёт заданной длительности УЗ-колебаний, в случае определения «ложного касания» колебания в системе могут прекратиться раньше, чем будет получено качественное соединение.
- Правильно ли выбран инструмент? Все металлы, используемые для получения соединений, имеют свои особенности, и это отражается на материале, из которого сделан инструмент, и форме контактирующей с проволокой поверхности. Например, для сварки золотой проволокой она часто выполняется с рельефом в форме поперечной борозды или перекрестия. Для проволоки разных диаметров и жёсткости подбирают индивидуальные радиусы входа и выхода проволоки, шероховатость поверхности инструмента и т. д. Любой инструмент для ультразвукового присоединения проволочных выводов имеет свыше 40 индивидуальных контролируемых параметров, измеряемых в сотых и тысячных долях миллиметра, что в конечном итоге объясняет его высокую цену. И конечно, усугубляет боль оши- бок при его выборе.
Итак, в течение первых миллисекунд происходит трение проволоки вдоль поверхности контактной площадки, приводящее к очистке трущихся поверхностей от загрязнений и оксидов. В случае сварки алюминиевой проволокой процессу очистки помогает тот факт, что чистый алюминий всегда покрыт твёрдой, но хрупкой оксидной плёнкой При УЗ-воздействии, сочетающем давление и колебания, этот тонкий слой мгновенно разрушается, и его твёрдые частицы быстро обнажают кристаллическую решётку чистого металла, однако не повреждают ее в силу малого размера абразивных частиц оксида алюминия. Эффект «нанотерки» объясняет, почему для качественной сварки алюминиевой проволокой достаточно комнатной температуры. В ходе сварки золотой проволокой, где такого абразива не возникает, для быстрой активации поверхностей требуется нагрев, как правило, до +110. 130°C.
После того как кристаллические решётки касающихся друг друга металлов пришли в тесное соприкосновение, начинается взаимодействие металлов на межатомном уровне (рис. 2). Металлы проволоки и подложки перемешиваются и образуют общие островки интерметаллических зёрен вдоль границы раздела.
Появление зёрен меняет характер движения проволоки, поскольку она теперь не представляет собой единую жёсткую структуру, в которой верхняя и нижняя поверхности движутся в унисон механическим колебаниям инструмента.
Нижняя поверхность проволоки все больше связывается и замедляется, в то время как верхняя продолжает колебаться: происходит деформация проволоки (сопутствующие процессы перекристаллизации и появление дислокаций атомной решётки в данной статье не рассматриваются).
Нужно заметить, что в отличие от пластической, эластическая составляющая деформации в проволоке крайне мала в такой момент, поскольку разница в амплитудах перемещения верхней и нижней поверхностей проволоки составляет порядка 1 мкм при толщине 20–30 мкм, а это на порядок превышает предел эластической деформации металла.
Стрелками на рис. 1–3 схематично показана результирующая амплитуда колебаний в системе. По мере образования и роста зёрен разница в амплитудах колебаний верхней и нижней поверхностей проволоки по сравнению с начальной фазой процесса становится все больше. Начинается уменьшение амплитуды колебаний всей системы, включая и колебания конца инструмента, в силу демпфирующего воздействия на него формирующегося сварного соединения.
Поскольку УЗ-воздействие на точку контакта продолжается, зерна разрастаются и в идеальном случае постепенно занимают всю площадь контакта. В какой-то момент движение нижней поверхности проволоки по подложке прекращается.
Фактически теперь начинает колебаться не проволока, а пара нижняя поверхность проволоки — подложка, хотя и с гораздо меньшей амплитудой, чем исходная пара проволока-подложка.
(обозначено парой маленьких стрелок на рис. 3).
В процессе увеличения площади зёрен сварного соединения инструмент, давящий на проволоку, деформирует её, при этом толщина области под инструментом уменьшается, а ширина получающегося соединения увеличивается. Деформация соединения может отслеживаться как функция смещения по оси Z в реальном времени, что даёт надёжный инструмент для контроля качества соединения с введением таких понятий, как «величина деформации по истечении заданного времени сварки» и «скорость нарастания деформации». Наличие подобных систем характерно для оборудования высокого уровня, предназначенного для производства изделий специального назначения. В своём базовом варианте система контроля деформации (DLC) доступна уже на полуавтоматических настольных установках F&S Bondtec серии 56ХХ и 58ХХ (рис. 4).
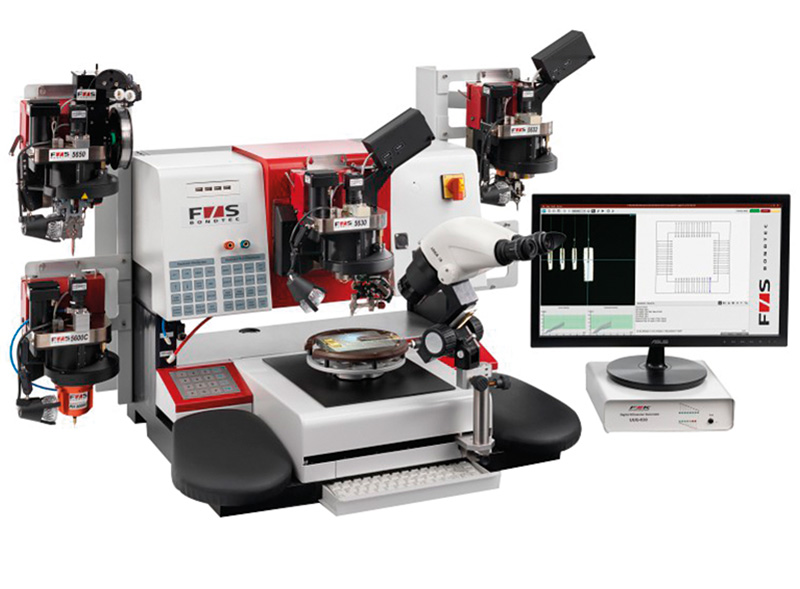
В процессе работы система ведёт постоянный мониторинг деформации и сравнивает результаты с полем допустимых значений. В случае отклонения параметров процесса от допустимых установка может либо отметить это отклонение в журнале работы, либо остановить свою работу до вмешательства оператора.
Интеллектуальная система BPC, предлагаемая на установках серии M17, идёт несколько дальше констатации фактов и сбора статистики. Поскольку при крупносерийном производстве нереально звать на помощь оператора в каждом случае отклонения от эталона, система BPC не только наблюдает, но и активно управляет процессом.
данные о деформации, получаемые в реальном времени, составляют управляющую часть системы с обратной связью и служат для повышения или снижения мощности и длительности УЗ-сварки при отклонении реального характера деформации от заданного пользователем. Таким образом, система BPC помогает в тонкой настройке процесса сварки каждого соединения «на лету» и предотвращает недостаток или избыток энергии, переданной в ходе процесса в точку сварки. Если вспомнить о важности определения момента касания, то в некоторой степени BPC компенсирует неизбежные на этом микроуровне погрешности, в режиме реального времени «загоняя» процесс каждой сварки в отведённые ему рамки. Без этой системы, особенно при работе с гибридными схемами и модулями, погрешности в определении точки касания приводят к большему разбросу параметров прочности (то есть снижению ресурса изделия до момента отказа слабейшего из них), а в худшем случае к слабым или, наоборот, «пережаренным» соединениям и отказам уже в ходе приёмочных испытаний.
В особенности важна функция управления длительностью процесса. Дело в том, что этот параметр по умолчанию устанавливают «с запасом», чтобы дать возможность соединению полностью сформироваться. Избыточное УЗ-воздействие обычно связано с металлургическим отпуском и рекристаллизацией соединения, при которых не происходит дальнейшей деформации проволоки. Вернёмся к схеме третьей фазы соединения (рис. 3), где колебания охватывают всю систему, с большей амплитудой у инструмента и меньшей у подложки. Фактически вместо одной системы появляются две пары, колеблющиеся с разной амплитудой. Градиент амплитуды колебаний в проволоке (вверху больше, внизу меньше) вызывает в материале проволоки холодную пластическую деформацию, называемую нагартовкой (наклёпом). Нагартовка помогает «полезным» дислокациям кристаллической решётки, которые возникли как зерна вдоль поверхности раздела металлов, распространиться глубже в структуры составных металлических слоёв, сильнее привязывая проволоку к подложке. В теории это должно увеличить ресурс соединения. Примером использования такого процесса в «большой» металлургии является холодная прокатка, галтовка и т. п. Важно, что нагартовка происходит при температурах ниже температуры рекристаллизации (начиная от комнатной и до 1/2 температуры плавления) и выражается в образовании округлых зёрен металла на месте вытянутых и деформированных.
Грань, за которой избыточная нагартовка приводит к образованию микротрещин, разрывов кристаллической решётки и повышенной хрупкости соединения, очень тонка. Округлая форма новообразованных металлических зёрен в соединении немного увеличивает содержание пор и снижает общую плотность, и избыточная длительность может привести к отказам уже после начала эксплуатации прибора. Оценить степень структурных изменений в каждом индивидуальном соединении, конечно, невозможно и оперировать приходится только косвенными методами оценки и воздействия на этот микропроцесс.
Алгоритм работы системы BPC в F&K Delvotec M17 предусматривает возможность управления длительностью сварки и мощностью УЗ-воздействия, что определяет интегральную энергию всех импульсов колебаний, приложенную к каждой конкретной точке.
Графически данная энергия может быть представлена как площадь фигуры под кривой деформации (рис. 6).
То, что мы имеем возможность с помощью системы BPC и (главное!) без участия оператора поднимать-опускать (мощность) и удлинять-укорачивать фигуру, изменяя её площадь, объясняет эффект значительного улучшения «критических для качества» характеристик процесса (таких как Cpk), что и предопределило широкую популярность оборудования F&K Delvotec у производителей автомобильной электроники, специальной техники и авионики.
Заметим, что до сих пор, говоря о процессе, который в русском языке называется «сварка», ни разу не было упомянуто ни плавление, ни даже повышение температуры в зоне соприкосновения металлов как результат трения проволоки о подложку. Действительно, несмотря на огромные усилия, затраченные исследователями, нагрев и его влияние на результат сварки до сих пор не удаётся измерить и оценить достоверно. Попытки увидеть микроскопические зоны расплавленного металла в микрошлифах соединений также пока не привели к успеху. Довод о том, что «видимо, эти зоны есть, просто они очень малы», опровергается любопытным опытом по успешному проведению ультразвуковой сварки при температурах порядка 200°C (состояние жидкого азота). Если бы образование соединения было связано с плавлением металлов, понижение температуры окружающей среды на 220°C наверняка сильно повлияло бы на принципиальную возможность получения такого соединения. Во внешнем мире, кстати, этот процесс называют не сваркой, а обозначают термином «бондинг» (bonding), то есть «присоединение, прикрепление, спайка». Возможно, с развитием несырьевых секторов отечественной промышленности термин «бондинг» приживётся и у нас.
Описанная модель соединения кристаллических решёток металлов без нагрева и плавления сначала вызывает сомнения, особенно концепция «жёсткой сцепки» проволоки с рабочим инструментом в ходе всего процесса. Гораздо проще представить себе, что на последних стадиях процесса (как только проволока «прилипает» к подложке) инструмент начинает скользить по проволоке, а не изменяет волшебным образом её внутреннюю структуру. Другими словами, мы утверждаем, что инструмент, ухватив проволоку «за спину», перемешивает с её помощью структуру кристаллической решётки в области контакта с подложкой без её плавления (фазового перехода в жидкое состояние и обратно). Однако есть еще как минимум три довода в пользу такой модели:
1. Путём уменьшения силы прижима инструмента (одного из главных параметров, см. выше) мы можем специально ослабить контакт между ним и проволокой уже после начала образования соединения. При этом инструмент начинает именно «скользить» вдоль проволоки в то время, как уже образовавшиеся зерна соединения удерживают её на подложке. Такое проскальзывание инструмента приводит к появлению обожжённых участков на проволоке вследствие перегрева трением об инструмент. При увеличении прижима до нормального значения этот эффект полностью исчезает, следовательно, при образовании соединения инструмент не скользит по проволоке даже после того, как она прочно соединяется с подложкой.
2. Весьма часто проявляется эффект отслоения («вырывания») металлизации контактной площадки в силу слабой адгезии или дефекта самой подложки. При этом отслоившаяся металлизация и проволока остаются связанными прочным соединением. Если в паре проволока-подложка не происходит колебаний малой амплитуды после образования прочного соединения (сама проволока и подложка находились бы после образования соединения в покое, а колеблется только инструмент, скользя по верхней поверхности проволоки), что тогда вызывает отрыв металлизации?
3. Модель формирования соединения подтверждается экспериментом и наблюдением. С развитием технологий микровидеосъёмки стало возможным провести детальный анализ процесса ультразвукового соединения металлов. В частности, когда в институте IZM (общество Фраунгофера) в Берлине группы Ланга и Шнейдера-Рамелоу провели исследования замедленной съёмки процесса при высоком увеличении, была зафиксирована вся последовательность стадий образования соединения, описанная выше, начиная с синхронного движения инструмента и проволоки по подложке и заканчивая эффектом уменьшения амплитуды колебаний от инструмента к подложке при сохранении её колебаний меньшей амплитуды уже после образования соединения на стадии нагартовки. Ещё одним подтверждением стали и результаты, полученные на лазерном измерителе вибрации, с помощью которого удалось проанализировать амплитуду и частоту колебаний на конце инструмента, проволоке и контактной площадке от начала и до конца процесса.
Далее мы поговорим о том, почему при выборе оптимальной частоты ультразвука необходимо учитывать тип материалов, с которыми предполагается работать.
Ультразвуковая микросварка | Сварить или склепать? ➔ часть II
В первой части статьи мы рассказали о стадиях процесса формирования сварного соединения, разобрались в различиях амплитуды колебаний в системе «инструмент-проволока-подложка» (рис. 1), а также поговорили о том, каким образом при минимальной деформации обеспечить максимальную надёжность контакта. Теперь речь пойдёт о влиянии резонансной частоты ультразвука на качество соединения.
Поскольку в подавляющем большинстве случаев для микросварки применяют частоты порядка 60 или 100/140 кГц, интересно знать, чем был обусловлен такой выбор и что происходит за пределами этого диапазона.
Краткое описание задачи:
Как не ошибиться при выборе оптимальной частоты ультразвуковой сварки?
В научной литературе и материалах конференций SEMI, IMAPS, IEEE и других отраслевых сообществ часто мелькали статьи на тему сварки с применением частот ультразвуковых колебаний 200 и даже 300 кГц. Тема вызывала тогда большой интерес из-за предположения о том, что энергия УЗ-колебаний способна заменить собой нагрев рабочего стола при сварке методом шарик-клин, чтобы процесс можно было проводить при комнатной температуре. Несмотря на то, что ряд опытов оказался успешным, в дальнейшем от идеи ВЧ-сварки пришлось отказаться главным образом по причинам низкой надёжности соединения и узкого технологического окна процесса. Снижение процента выхода годных соединений просто-напросто не компенсировалось сокращением себестоимости. Сегодня в академической среде к УЗ-сварке на высоких частотах практически не возвращаются. Но некоторые разработчики и технологи все же пробуют перейти с 60 на 100 или 140 кГц, когда экспериментируют с новыми материалами и режимами.
Поскольку все специалисты получают неоднозначные результаты, есть смысл понять, зачем вообще менять частоту УЗ-колебаний системы? Какие параметры «утянет» за собой изменение частоты? Своим опытом готовы поделиться эксперты производителя первой в мире автоматической установки ультразвукового присоединения проволочных выводов F&K DELVOTEC M17.
В общем случае с точки зрения воздействия на кристалл/подложку наиболее важным элементом процесса является длительность образования соединения при той или иной резонансной частоте УЗ-преобразователя. Для создания качественного сварного соединения требуется 1000–3000 циклов колебаний инструмента в системе «инструмент-проволока-подложка» (при условном времени сварки около 20 мс и частоте 100 кГц). Именно столько циклов взаимного перемещения всех составляющих системы относительно друг друга требуется для образования наклёпа и общих «зёрен» будущего сварного соединения (подробнее об этом рассказывалось в первой части публикации).
Теоретически при повышении частоты колебаний должно пропорционально сокращаться время, необходимое для формирования сварного соединения. Впрочем, общая производительность оборудования значительно не повысится, так как время приложения УЗ-воздействия занимает менее половины времени цикла — остальное тратится на позиционирование, распознавание и движение рабочей головки.
Гораздо важнее другое. При более высоких частотах качественные соединения образуются при меньших амплитудах колебаний. Это вовсе не значит, что амплитуды колебания на таких частотах по умолчанию ниже (амплитуду преобразователя можно подогнать в нужных пределах в ходе изготовления).
Таблица 1 — Соответствие материалов и частоты УЗ-колебаний
Вернёмся к первой стадии образования сварного соединения в рассмотренной нами ранее модели (рис. 1). После взаимного трения проволоки вдоль поверхности контактной площадки, приводящего к очистке трущихся поверхностей от загрязнений и оксидов, начинается взаимодействие металлов на межатомном уровне. Металлы проволоки и подложки перемешиваются и образуют общие островки интерметаллических «зёрен» вдоль границы раздела. На второй стадии, по мере образования и роста «зёрен», разница в амплитудах колебаний верхней и нижней поверхностей проволоки становится все больше по сравнению с начальной фазой процесса. Начинается уменьшение амплитуды колебаний всей системы «инструмент проволока-подложка», включая колебания конца инструмента, в силу демпфирующего воздействия на него формирующегося «вязкого» соединения металлов. Таким образом, увеличение амплитуды колебаний инструмента оказывается более эффективным при работе с толстыми покрытиями. Грубые поверхности типа гибридных толстоплёночных паст выигрывают от эффекта шлифовки или планаризации под действием бóльших амплитуд на низких частотах (60 кГц и ниже). В то же время большая амплитуда подвергает риску тонкие слои напыления и гладкие поверхности контактных площадок хрупких кристаллов, например в ПАВ‑фильтрах, где толщина металлизации может составлять 40 нм. Столь тонкие слои не требуют грубой притирки и превосходно свариваются на более высоких частотах (140 кГц). По мнению инженеров компании F&K Delvotec, рабочая частота системы в 100 кГц является золотой серединой и может стать оптимальным решением для большинства задач. Это подтверждается и статистикой: чаще всего заказчики выбирают именно данную частоту в качестве основной.
Но как быть, если номенклатура изделий содержит взаимоисключающие группы? Менять установку? Покупать второй генератор? Что касается амплитуды, заказчики в любой момент могут изменить своё предпочтение и заказать преобразователь с другой характеристикой амплитуды колебаний. Это недорогое удовольствие, учитывая стоимость изделий, для производства которых требуется подобный «тюнинг». А цифровой УЗ-генератор UUG‑030 от F&K Phisyktechnik 1 устанавливается по умолчанию на всех моделях брендов и автоматически настраивается на резонанс преобразователя головки в диапазоне 40–200 кГц. При этом у клиентов остаётся свобода маневра при выборе иной резонансной частоты и мощности для экзотических применений и материалов. Например, работа сверхдлинным инструментом в колодцах глубиной 50–70 мм или TAB-сварка изолированной лентой иногда требуют индивидуального подхода.
С генератором UUG‑030 установки серий 53ХХ, 56ХХ, 58ХХ, М17 (рис. 2), оснащённые соответствующими сменными рабочими головками, способны работать с тонкими и толстыми проволоками в диапазоне 17–600 мкм, в том числе композитными и изолированными, с лентой сечением до 2000×300 мкм.
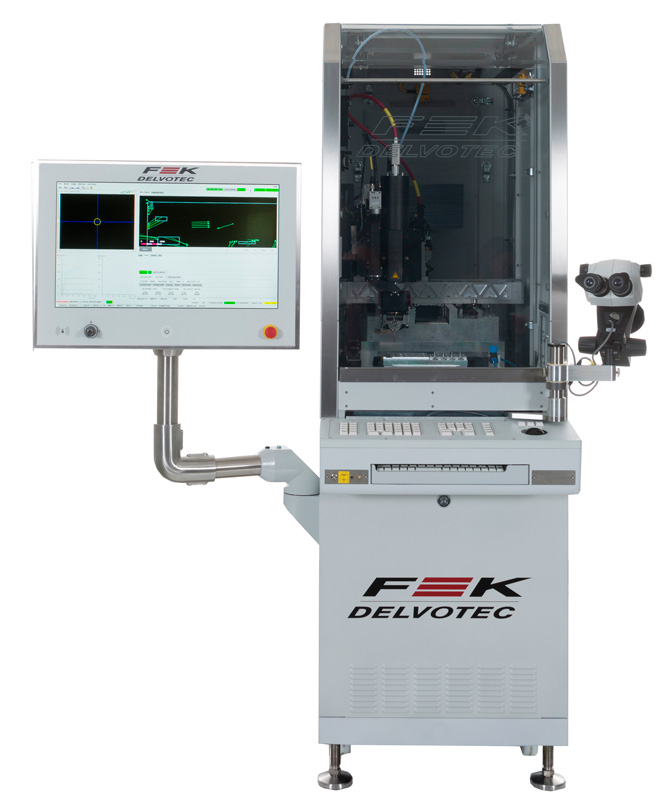
Установка становится настоящей микрофабрикой, способной действовать со всеми современными материалами, с подложками любого типа, алюминиевыми, золотыми, композитными и медными проволоками. А серия 56ХХ к тому же сможет проводить автоматическое тестирование прочности соединений, просто импортируя программу сварки.
Очевидно, что чем выше частота, тем выше линейная скорость движения кончика инструмента. Точнее, скорость всей системы «инструмент-проволока-подложка». Большинство материалов, входящих в состав колебательной системы, с возрастанием частоты УЗ-воздействия больше сопротивляются влиянию друг на друга, поскольку начинает сильнее проявляться противодействующая сила упругого столкновения. На практике это означает, что ультразвуковые колебания работают «по поверхности» и меньше проникают во внутреннюю структуру материалов проволоки и контактной площадки. И наносят им меньший вред. Именно поэтому мягкие материалы типа полиимидных подложек лучше варятся именно на более высоких частотах. Это справедливо и для некоторых чувствительных кристаллов или ПАВ‑фильтров. При стандартном наборе параметров (частота, амплитуда) выполнить качественную сварку на нежной поверхности сложно, но при правильном подборе характеристик, в том числе и на более высокой частоте, трудностей не возникнет.
И наоборот, на низких частотах проволока за счёт более «мягкого» движения подстраивается под грубую и шероховатую поверхность контактных площадок (FR4, толстоплёночных ГИС, LTCC, HTCC), обеспечивая лучшее качество сварки. В таблице представлены общие соответствия материалов и частоты УЗ-колебаний.
При более высокой частоте тракта можно получить прочное соединение на относительно малой деформации проволоки. То есть увеличение частоты становится ещё одним способом улучшить качество и расширить технологическое окно параметров при работе с тонкой (17–20 мкм) проволокой.
Но и для стандартной (25–35 мкм) проволоки меньшая деформация всегда предпочтительнее «передавливания»: понижаются напряжения в пятке сварки, определяющие надёжность, долговечность и устойчивость соединения к термоциклам. Это подтверждается и экспериментально — усилия на обрыв сварных петель крючком уменьшаются с увеличением деформации после достижения ею некоего оптимального значения.
Рис. 3 — Соответствие частоты УЗ-колебаний и метода сварки
ЗАКЛЮЧЕНИЕ
Со времени возникновения УЗ-сварки в 1947 году единых предписаний в отрасли так и не было выработано: любой из методов сварки по-прежнему можно применять в сочетании с двумя-тремя частотами УЗ-генератора. Помимо рассмотренных факторов, решение в пользу той или иной частоты принимается в зависимости от длины и типа рабочего инструмента, длины и высоты петель и типа проволоки. На рис. 3 показана вероятность использования той или иной частоты в привязке к методу сварки (отмечено кружком). Данные получены в ходе закрытого опроса заказчиков оборудования F&K Delvotec, а это в основном изготовители изделий высокой надёжности и автоэлектроники.
В статье мы рассмотрели лишь первый общий принцип выбора частоты в зависимости от материала и типа поверхности контактной площадки. Образно говоря, частота должна быть высока настолько, насколько это возможно (для минимизации рисков повреждения кристалла, «передавливания» пятки петли и уменьшения общего времени воздействия), но в то же время низка настолько, насколько это необходимо для компенсации шероховатости поверхности и проникновения УЗ-частоты вглубь материала. В последующих статьях цикла мы постараемся дать рекомендации и в отношении других параметров.
SamsPcbGuide, часть 14: Технологии — Микроразварка и технология Chip-On-Board
В этой самоизоляционной статье я расскажу о разварке проволочных микровыводов (англ. wire bonding). В контексте печатных плат речь пойдёт о технологии монтажа кристаллов на печатную плату (англ. chip-on-board, COB). Обязательно смотрите видео по ссылкам, микроразварка — это очень красиво!
Разварка обеспечивает электрическое соединение кристалла с выводами корпуса (при корпусировании микросхемы), либо напрямую с проводниками печатной платы (технология COB). Альтернативный способ электрического соединения – это перевёрнутый монтаж кристалла (англ. flip-chip), как в конструкции самого корпуса, так и непосредственно на печатную плату (рис. 1).
Монтаж с использованием микропроволочных выводов появился следом за первыми интегральными схемами в начале 1960-ых годов и успешно используется до сих пор. Перевёрнутый монтаж – это современная технология, возникшая в ответ на требования повышения количества выводов, увеличения быстродействия и снижения габаритов. Однако она имеет ряд конструкционных ограничений, связанных с обеспечением надёжности (подробно об этом я писал здесь), и является технологически более сложной.
В этой статье не будет подробно рассматриваться классификация и теория различных методов разварки – это очень объёмный материал, выходящий за рамки обсуждаемого вопроса. Дело в том, что за свою продолжительную историю технология присоединения микропроволочных выводов развивалась в направлениях повышения стабильности, надёжности, скорости процесса сборки, расширения возможностей оборудования по созданию сварочных петель сложной формы и высокой плотности монтажа (рис. 2). Разнообразие задач и отсутствие универсальной технологии привело в процессе поиска к разработке различных методов разварки. Рассмотрим кратко основные моменты. Несмотря на разнообразие методов, общим для всех принципом является то, что сварное соединение образуется в результате давления и нагрева контактирующих поверхностей до высокой температуры до образования межатомных соединений (чаще всего это интерметаллиды). В зависимости от метода нагрева разварка делится на следующие основные типы: термокомпрессионная (внешний нагрев), ульразвуковая (трение при ультразвуковом импульсе), термозвуковая (сочетание внешнего нагрева и ультразвукового импульса) и контактная (импульсный нагрев при протекании электрического тока) сварки. Основные материалы микропроволочных выводов – алюминий, золото, медь. Медь используют вместо золота для снижения стоимости, но она более жёсткая, а также быстро окисляется на воздухе, что осложняет процесс сварки, и требует более сложного оборудования, создающего в зоне разварки инертную среду (азот или формовочный газ). Высокая же проводимость меди является драйвером для замены алюминия в разварке силовых приборов, несмотря на более сложный техпроцесс.
Ось проволоки при разварке может быть ориентирована параллельно – это разварка типа «клин» (англ. wedge bond), или перпендикулярно – это разварка типа «шарик» (англ. ball bond) (рис. 3). У петли чаще всего две точки контакта, поэтому по типу сварочных точек методы разварки делятся на «шарик-клин» и «клин-клин». Наиболее распространены ультразвуковая сварка алюминиевой проволокой типа «клин-клин» (видео) и термозвуковая сварка золотой/медной проволокой типа «шарик-клин» (видео). В последнем случае для формирования шарика используется оплавление кончика проволоки искровым разрядом (видео), что только добавляет эпичности и красоты в процесс разварки. Для силовых приборов используются алюминиевые и золотые ленты (видео с шикарным звуковым сопровождением).
Ключевыми параметрами при ультразвуковой/термозвуковой разварке являются усилие сварки, мощность и продолжительность ультразвукового импульса. Их сочетание для заданной установки разварки, конкретной проволоки (диаметр, жесткость), конкретного разварочного инструмента, конкретных параметрах контактной площадки (размер, материал) должно обеспечивать повторяемость процесса разварки с гарантируемыми параметрами надёжности соединения. Напрямую контролируемыми параметрами являются внешний вид, усилие на отрыв (англ. pull test) и усилие на сдвиг (англ. shear test) (рис. 4), косвенно – сбои при термоциклировании и других испытаниях в составе изделия.
Подбор параметров является в некотором роде магической процедурой, но тут есть ряд рекомендаций. В целом, выполняется он методом научного тыкапоставноки эксперимента (англ. design of experiment, DOE), то есть последовательным перебором параметров в некотором диапазоне. Отталкиваться в этом поиске можно от опубликованных результатов по оптимизации параметров (например, статьи [1, 2]), от рекомендаций производителя оборудования и, конечно, от наработанного опыта. Далее выполняются тестовые разварки для каждого набора параметров с последующим контролем внешнего вида и усилий на отрыв/сдвиг. Для контроля внешнего вида вполне достаточно увеличения x100 с возможностью измерения линейных размеров (рис. 5), для измерения усилий на отрыв/сдвиг применяются специализированное оборудование (для лабораторных задач можно, например, использовать граммометр с крючком, а сдвиг выполнять вручную и исследовать форму разрушения на увеличениях x100…200 и более). Для оценки внешнего вида важно насмотреться на как можно большее количество микрофотографии красивых и некрасивых точек разварки (вот здесь и здесь, например, есть несколько хороших микрофотографий с описанием), потому что по моему опыту есть корреляция между красотой разварки и её качеством. Кроме того, с опытом появляется понимание того, как при наладке параметров их варьировать, чтобы получить требуемый результат (не хватает усилия при сварке или же слишком большая мощность), то есть перебор становится всё более осознанным и направленным. В своё время мне очень помогло прочтение статей с теорий формирования сварки и влияния параметров на её качество [3, 4]. И ещё вот этих не менее прекрасных статей [5, 6], где авторы (памятники таким ставить) исследовали формирование петли с помощью высокоскоростной камеры. А так, количество прочитанных статей добить до 100, количество разваренных и оторванных перемычек до 10000 и магии в этом процессе станет несколько меньше. Всё ещё очень от установки, конечно, зависит – я в упорной борьбе выжимал максимум из белорусского автомата ЭМ-4450.
Теперь вернёмся к печатным платам и некоторым особенностям их проектирования по технологии COB. Технология применяется для снижения стоимости или при микроминиаютиризации, создании многокристальных модулей и сборок (в частности, светодиодных). На рис. 6 приведено изображение из одной из презентаций Wurth Electronics по данной теме с рекомендациями по проектированию. Представленные ограничения на размеры могут служить в качестве ориентира, дополнительно рекомендуется использовать 3D-модель разварочного инструмента для проверки доступности всех КП во избежание проблем уже по факту. Важно обратить внимание, что в зоне разварки на печатной плате снята маска, чтобы не создавать помех рабочей плоскости разварочного инструмента. Зону под кристаллом лучше не использовать под трассировку, а разместить там монтажную площадку (как на рисунке), особенно если основание кристалла имеет потенциал или требуется монтаж на проводящий клей для повышения теплоотвода. Монтаж кристалла на маску возможен, особенно в случае дальнейшего компаундирования кристалла. Монтаж кристалла может также осуществляться в вырез в печатной плате (англ. pcb cavity) с расположением КП в том же топологическом слое или уровнем выше.
Следующий нюанс, касающийся трассировки, заключается в рекомендации ориентировать КП на печатной плате по направлению разварочных петель для золотой проволоки. Обоснованность её я понял только при написании программы разварки. Суть в том, что вторая точка варки образуется на краю капилляра (рис. 7), а при написании программы указывается его центр, что при больших углах приводит к необходимости учитывать это и смещать расположение точки в программе. Иными словами, так удобней, но это не является принципиальным ограничением, и удобство трассировки имеет более высокий приоритет.
По поводу финишного покрытия печатных плат в отрасли имеется консенсус: для разварки алюминиевой проволокой достаточно ENIG, для золотой проволоки – ENEPIG или гальваническое золото (рис. 8). Почему нельзя использовать более дешёвый и доступный ENIG для разварки золотой проволокой? Ответ, который удавалось найти, заключается в том, что дрейф никеля приводит к деградации сварного соединения со значительным снижением его надёжности. А в ENEPIG палладий служит барьерным слоем, который препятствует этому дрейфу. Для отладочных образцов использовать ENIG вполне допустимо, тем более что параметры разварки при прочих равных для этих покрытий близки. ENEPIG же прямо указывается как рекомендуемое покрытие во многих источниках, по нему приводятся данные по испытаниям на надёжность [7, 8].
Большое внимание также уделяется проблеме образования нежелательных интерметаллидов Au-Al («пурпурная чума» и другие страшные слова), которые возникают при разварке золотой проволокой на алюминиевые КП кристалла или алюминиевой проволокой на ENIG. Вопрос этот достаточно сложный и для полного его понимания необходимых знаний химии у меня, к сожалению, нет. Вывод такой, что разварка в системе Au-Al является потенциальным источником сбоев, особенно при высоких температурах, и должна тщательно испытываться на надёжность. Максимизация усилия на отрыв как одна из стратегий, так как прочность сварки и долговременная надёжность связаны (более тонкий интерметаллический слой с большей площадью покрытия).
Слабым местом разварки «шарик-клин» на ENEPIG из-за тонкого слоя золота является вторая точка сварки. Задача получения качественной разварки осложняется также загрязнением КП после этапа поверхностного монтажа компонентов на печатную плату. Существуют два метода повышения надёжности: с укреплением бампом после сварки (англ. security bump/ball, SB) и c предварительным бампированием (англ. ball stich on ball, BSOB, или stand-off stich, SOS) (рис. 9). Дополнительным параметром оптимизации в этих технологиях является смещение бампа относительно точки сварки [9, 10]. По собственному опыту могу сказать, что для COB себя хорошо показала BSOB. Кстати, BSOB хороша ещё тем, что позволяет ставить вторую точку сварки на кристалл (англ. reverse bonding) и осуществлять разварку между кристаллами напрямую в многокристальных сборках. Буду рад, если в комментариях поделитесь своим опытом применения SB/BSOB и ENIG/ENEPIG.
И напоследок практический совет, может быть, кому-то будет полезно. Разварочные капилляры (а они недешёвые и поставка долгая), бывает, наглухо забиваются золотом. В случае, когда канал невозможно прочистить даже нихромовой проволокой, инструмент всё ещё рано списывать. Поможет «царская водка» – и инструмент как новый.
Литература
[1] J. Gomes, M. Mayer, B. Lin, ”Development of a Fast Method for Optimization of Au Ball Bond Process”, 2015
[2] Byung-Chan Kim, Seok-Jae Ha, etc. “Process Capability Optimization of Ball Bonding Using Response Surface Analysis in Light Emitting Diode (LED) Wire Bonding”, 2017
[3] Hui Xu, Changqing Liu, etc, “Initial bond formation in thermosonic gold ball bonding on aluminium metallization pads”, 2010
[4] Hui Xu, Changqing Liu, etc. “The role of bonding duration in wire bond formation: a study of footprints of thermosonic gold wire on aluminium pad”, 2010
[5] Fuliang Wang, Yun Chen, Lei Han, ”Experiment study of dynamic looping process for thermosonic wire bonding”, 2012
[6] Fuliang Wang, Yun Chen, Lei Han, “Effect of Capillary Trace on Dynamic Loop Profile Evolution in Thermosonic Wire Bonding”, 2012
[7] Chun-Hsien Fu, Liang-Yi Hung, etc. “Evaluation of New Substrate Surface Finish: Electroless Nickel/Electroless Palladium/Immersion Gold (ENEPIG)”, 2008
[8] Kuldip Johal, Sven Lamprecht, Hugh Roberts, ”Electroless nickel/electroless palladium/immersion gold plating process for gold-and aluminum-wire bonding designed for high-temperature applications”, 2000
[9] Chunyan Nan, Michael Mayer, etc. “Golden bump for 20 micron diameter wire bond enhancement at reduced process temperature”, 2011
[10] Young K. Song and Vanja Bukva, “Challenges on ENEPIG Finished PCBs: Gold Ball Bonding and Pad Metal Lift”, 2017
Методы и технологии микросварки
В общем смысле микросварка — это процесс твердотельной сварки за счёт тесного взаимодействия двух металлических материалов, при котором скорость взаимного проникновения (диффузии) металлов является функцией температуры, силы, ультразвуковой энергии и времени.
Микросварка широко применяется для создания межсоединений между кристаллом интегральной схемы и её корпусом при производстве микросхем и других полупроводниковых устройств. Микросварка также используется для подключения микросхем к другой электронике или для соединения одной печатной платы (PCB) с другой. Микросварка считается наиболее рентабельной и гибкой технологией монтажа и используется для сборки подавляющего большинства полупроводниковых корпусов.
Существуют несколько методов или технологий микросварки:
- термокомпрессионная микросварка
- контактная (терморезистивная, микроконтактная) микросварка
- термозвуковая микросварка
- ультразвуковая микросварка.
Термокомпрессионная микросварка
При термокомпрессионной микросварке для деформации проволоки применяется нагрев и усилие сжатия. Основными параметрами процесса являются температура, усилие сварки и длительность сварки. Процессы диффузии находятся в экспоненциальной зависимости от температуры. Поэтому даже небольшое увеличение температуры может значительно сказываться на улучшении качества микросварки.
Обычно при термокомпрессионной микросварке требуется высокая температура (более 300°C) и значительное усилие для образования надёжного соединения. Однако высокая температура и значительное усилие прижима недопустимы для чувствительных кристаллов. Кроме того, этот процесс очень чувствителен при сварке загрязнённых поверхностей. Поэтому в настоящее время термокомпрессия редко используется при производстве оптоэлектронных и интегральных схем.
Контактная (терморезистивная, микроконтактная) микросварка
При этом методе для сварки применяется усилие сжатия и кратковременный нагрев, который осуществляется за счёт кратковременного протекания тока по проволоке. Для протекания тока используется расщеплённый электрод, к обкладкам которого во время сварки прикладывается постоянное или переменное напряжение. Свариваемое изделие и электрод находятся при комнатной температуре. Микроконтактная сварка успешно применяется для сварки золотой, медной, платиновой, стальной проволоки или ленты к контактным площадкам из алюминия, золота, меди, хрома и других. Этот тип микросварки довольно распространён на российских предприятиях при производстве микросборок.
Термозвуковая микросварка
Для термозвуковой микросварки применяются нагрев, усилие сжатия и ультразвуковые колебания. Термозвуковую микросварку используют для сварки золотых проводников к золотым или алюминиевым покрытиям на подложках. Нагрев осуществляется за счёт размещения свариваемого образца на нагревательном столике (так называемый «нижний подогрев». Дополнительно к нижнему подогреву применяют нагрев сварочного инструмента (капилляра) — «верхний подогрев», что улучшает параметры микросварки. Усилие прикладывается к сварочному инструменту вертикально вниз, прижимая проволоку к свариваемой поверхности. Ультразвуковые колебания передаются на микроинструмент (капилляр) во время его контакта с проволокой. Термозвуковая микросварка обычно используется для разварки золотой проволоки или ленты.
Ультразвуковая микросварка
Ультразвуковая микросварка проводится при комнатной температуре с применением усилия сжатия и ультразвуковых колебаний. В основном ультразвуковая микросварка используется для разварки алюминиевой проволоки к алюминиевым или золотым площадкам, хотя этим способом сварки в некоторых случаях можно приварить и золотую проволоку к золотым площадкам. Эта технология доминирует для сварки толстой алюминиевой проволоки (более 100 мкм) в силовой электронике.
Более подробно о влиянии частоты ультразвуковых колебаний на качество ультразвуковой микросварки можно прочитать в этой статье.
Читайте также: