Условия захвата металла валками при прокатке
Обновлено: 11.05.2024
Прокаткой называют вид обработки давлением, при котором металл пластически деформируется вращающимися гладкими или имеющими соответствующие канавки (ручьи) валками. Взаимное расположение валков и заготовки, форма и число валков могут быть различными. При этом получают прокат – готовые изделия или заготовки для последующей обработки ковкой, штамповкой, прессованием, волочениемили резанием. В прокат перерабатывают до 80 % всей выплавляемой стали и большую часть цветных металлов и сплавов, его используют в строительстве, машиностроении и других отраслях промышленности.
Существуют три основных вида прокатки: продольная, поперечная и поперечно-винтовая (косая).
При продольной прокатке заготовка деформируется между гладкими или имеющими калибры валками, вращающимися в противоположные стороны, и перемешается перпендикулярно к осям валков.
При поперечной прокатке валки вращаются в одном направлении, оси их параллельны, а заготовка деформируется ими, вращаясь вокруг своей оси.
При поперечно-винтовой(косой) прокатке валки вращаются в одном направлении, оси их расположены под некоторым углом, благодаря чему заготовка деформируется валками и при этом не только вращается, но и перемещается оступательно вдоль своей оси.
Продукция прокатного производства. Инструмент и оборудование.
Прокатным станом называется технологический комплекс последовательно расположенных машин и агрегатов, предназначенных для пластической деформации металла в валках (собственно прокатки), дальнейшей его обработки и отделки (правки, обрезки кромок, резки на мерные изделия и пр.) и транспортировки.
Продукцией прокатного производства являются полосы, листы, трубы, прутки различного профиля (круглого, квадратного, прямоугольного, шестигранного, углового, двутаврового, швеллерного, таврового и др.), железнодорожные и трамвайные рельсы, колеса, шары, кольца и др.
Технология производства основных видов проката, производство труб.
Трубопрокатные установки различают по способу производства, размерам изготавливаемых труб и составу основного оборудования, которое в каждом конкретном случае располагается по определенному плану.
Для производства бесшовных труб широко применяются установки с
пилигримовым, автоматическим и непрерывным станом. В качестве заготовок для производства бесшовных труб используют слитки, а также катаные заготовки. Процесс прокатки состоит из двух основных операций: прошивки отверстия в заготовке и прокатки прошитой заготовки. Прошивку выполняют на прошивном стане поперечно-винтовой прокатки двумя конусообразными рабочими валками, оси которых пересекаются под углом 6. 12°. В валках такого стана заготовка 1 получает одновременно вращательное и поступательное движение.
Металлические трубы обычно делают сварными. При этом либо лист сворачивают так, что шов идёт вдоль трубы, либо навивают ленту по спирали. Современные технологии позволяют заметно усилить прочность шва стальной трубы — его прочность всего на 10—15 % меньше прочности остальной её части.
Ковка. Операции ковки: осадка, протяжка, прошивка, инструмент.
Ковка – один из способов обработки металлов давлением, при котором инструмент оказывает многократное воздействие на нагретую заготовку, в результате чего она, деформируясь, постепенно приобретает заданную форму и размеры.
К основным операциям машинной ковки относятся осадка, протяжка, прошивка, гибка, сварка, скручивание, отрубка и раскатка.
Осадка – уменьшение высоты заготовки при увеличении площади ее поперечного сечения. Осадку производят бойками или осадочными плитами. Заготовки, у которых отношение высоты к диаметру более 2,5, осаживать не рекомендуется во избежание возможного продольного искривления.
Протяжка – удлинение заготовки или ее части за счет уменьшения площади поперечного сечения. Она осуществляется последовательными обжатиями отдельных, примыкающих друг к другу участков заготовки при ее подаче вдоль оси.
Прошивка – получение полостей в заготовке за счет вытеснения материалу. Она может использоваться как самостоятельная операция для образования отверстия либо как подготовительная операция для последующей раскатки или протяжки заготовки на оправке.
Ковка. Операции ковки: отрубка, гибка, инструмент. Оборудование для ковки.
Отрубка – полное отделение части заготовки по незамкнутому контуру путем внедрения в заготовку деформирующего инструмента. Отрубку топорами осуществляют для удаления прибыльной и донной частей слитка, лишних концов поковки или для разделения длинной поковки на более короткие части.
Гибка – образование или изменение углов между частями заготовки или
Придание ей криволинейной формы. Гибку осуществляют с помощью различных опор, приспособлений и в подкладных штампах.
Оборудование: Операции машинной ковки выполняют на различных типах молотов и гидравлических прессах.
Молоты – машины, деформирующие металл ударом за счет кинетической энергии падающих частей (штока, бабы, верхнего подвижного бойка), накопленной к моменту соударения с заготовкой. Скорость движения рабочего инструмента в момент удара составляет 3. 8 м/с, время деформирования – сотые доли секунды. Основной характеристикой молота является масса падающих частей.
В зависимости от типа привода молоты бывают пневматическими, паровоздушными, механическими, гидравлическими, газовыми и др.
Ковочные гидравлические прессы. Основной характеристикой пресса является развиваемое усилие. Гидравлические ковочные прессы изготавливают с усилием 3. 20 МН. Гидропрессы работают со значительно меньшими скоростями, чем молоты. Скорость
деформирования (движение рабочего инструмента) не превышает 0,3 м/с.
Разработка техпроцесса изготовления поковки методом горячей объемной штамповки.
Горячей объемной штамповкой можно получать поковки сложной конфигурации без напусков, с небольшими припусками и допусками, что снижает объем последующей обработки резанием. Производительность штамповки значительно выше, чем ковки, и составляет десятки и сотни поковок в час.
Технологический процесс изготовления поковок горячей объемной штамповкой в общем случае состоит из следующих основных операций: резки проката на мерные заготовки на пресс-ножницах, нагрева заготовок в электрических или пламенных печах, осадки заготовки, штамповки в штампе, обрезки заусенца и прошивки отверстия, термообработки и очистки поверхности от окалины в дробеметном барабане.
В зависимости от типа штампов различают следующие способы горячей объемной штамповки: в открытых штампах, в закрытых штампах, штамповка выдавливанием, штамповка прошивкой, штамповка в разъемных матрицах.
Холодная листовая штамповка. Сущность, операции: вытяжка с утонением стенки, отбортовка, обжим, формовка.
Листовая штамповка – способ изготовления плоских и объемных изделий из листа, полосы, ленты без существенного изменения толщины металла. Листовая штамповка характеризуется высокой производительностью, обеспечивает точность и стабильность размеров изготавливаемых деталей и позволяет получить значительную экономию металла. Операции листовой штамповки можно полностью механизировать и автоматизировать.
Все основные операции листовой штамповки делятся на разделительные, в которых этап пластического деформирования завершается разрушением заготовки, и формообразующие, в которых заготовка в процессе деформирования не разрушается, а только изменяет свою форму.
Вытяжка – образование полой заготовки или детали из плоской или полой листовой заготовки.
Отбортовка – образование борта по внутреннему или наружному контуру листовой заготовки. При отбортовке отверстия металл в зоне деформации растягивается и утоняется.
Кинематические условия продольной прокатки
В зависимости от положения полосы в очаге деформации различают три стадии прокатки: захват металла валками, установившийся процесс и выброс металла из валков.
Первая стадия начинается с момента захвата металла, продолжается в процессе заполнения очага деформации и заканчивается, как только передний конец полосы выйдет за пределы плоскости выхода металла из валков. Это неустановившаяся стадия, поскольку в процессе заполнения очага деформации происходит изменение практически всех параметров процесса прокатки.
Вторая стадия – установившийся процесс прокатки, начинается с момента образования переднего конца некоторой длины за плоскостью выхода металла из валков и длится до момента приближения заднего конца полосы непосредственно к плоскости входа металла в валки. В этой стадии значения всех параметров прокатки выдерживаются примерно на одном уровне.
Третья стадия начинается с момента приближения заднего конца полосы непосредственно к плоскости входа металла в валки, длится в течение освобождения очага деформации и заканчивается, как только задний конец полосы пересечет плоскость выхода металла из валков. Как и первая, это неустановившаяся стадия процесса прокатки.
Посмотрим, как изменяется соотношение сил, действующих на полосу, при переходе от неустановившегося к установившемуся процессу прокатки.
По мере продвижения материала вглубь очага деформации точка приложения нормальной силы будет передвигаться по направлению к плоскости выхода и при достижении установившегося процесса нормальная сила займет положение под углом j к линии центров валков (рис.3.11).
Тогда условие захвата металла в установившемся процессе будет . Если принять, что нормальные напряжения равномерно распределяются по длине очага деформации, то нормальная сила будет делить угол захвата пополам, т.е. .
Следовательно, в установившемся процессе условие захвата металла валками будет иметь вид: или .
Отсюда следует весьма важный с практической точки зрения вывод. Наиболее трудным в смысле осуществления захвата металла валками является начальный период прокатки. Если же он состоялся, то в условиях установившегося процесса появляется возможность примерно двукратно увеличить угол захвата и соответственно обжатие.
Зависимость коэффициента трения от условий прокатки.
1. При прокатке в стальных валках коэффициент трения на 15…20% больше, чем при прокатке в чугунных.
2. Чем больше шероховатость поверхности валков и/или полосы, тем выше коэффициент трения (см. табл.3.1).
3. С повышением содержания углерода в стали коэффициент трения снижается. При прокатке легированных сталей он в 1,2…1,6 раза больше, чем при прокатке углеродистых сталей.
4. В зависимости от температуры прокатки коэффициент трения вначале увеличивается, достигая максимума при 500…800 o C. Затем, при дальнейшем увеличении температуры он снижается (рис.3.12). Полагают, что основное влияние на коэффициент трения оказывает не собственно температура, а окалина на поверхности полосы. Образующийся при нагреве окисный слой, как абразив, способствует увеличению коэффициент трения. При повышенных температурах он размягчается и начинает действовать как смазка.
5. С увеличением скорости прокатки коэффициент трения снижается. По данным Таффеля особенно интенсивно он снижается в интервале скоростей 2…3 м/сек (рис.3.13).
6. При увеличении контактных напряжений коэффициент трения проявляет тенденцию к увеличению.
7. применение смазки способствует снижению коэффициента трения (см. табл.3.1).
Предложено множество формул для определения коэффициента трения. Одной из наиболее ранних и достаточно удачных является формула экелунда:
f = 1,05 – 0,0005t, где t – температура прокатки.
Она получена экспериментальным путем при прокатке стали с содержанием углерода 0,15% при t ³ 700 o C в стальных валках. Формулы многих других авторов структурно не отличаются от формулы Экелунда – изменяются лишь значения свободного члена и множителя при температуре.
Наиболее удачно усовершенствовали формулу Экелунда Бахтинов и Штернов, введя в нее три дополнительных коэффициента:
где К1 - учитывает материал валков. Для стальных он равен единице, для чугунных – 0,8;
К2 - учитывает скорость прокатки. При V £ 1 м/сек. он равен единице и плавно снижается до 0,4 при V £ 16 м/сек.;
К3 - учитывает материал прокатываемой полосы. Для углеродистой стали он равен единице, для легированных – 1,2…1,6.
Существует ряд методов экспериментального определения коэффициента трения. По одному из них - методу максимального угла захвата, - вычисляют величину обжатия при максимальном угле свободного захвата и по ней определяют его значение по формуле . Полученное значение a (в радианах) приравнивают коэффициенту трения.
4.1. Опережение и отставание.
Если измерить скорость полосы на входе и выходе из валков (соответственно Vн и Vh ) и сопоставить ее с окружной скоростью валков Vв (рис.4.1.), то окажется, что они связанны неравенством Vн < Vв < Vh , т.е. задний конец отстает, а передний опережает валки. Эти явления – входа полосы в валки со скоростью, меньшей окружной скорости валков, называют отставанием (Sн), а выхода полосы из валков со скоростью, выше окружной скорости валков – опережением (Sh). Какова их природа? При продольной прокатке валки сообщают полосе переносную скорость Vв. Кроме того, в процессе обжатия большая часть металла в соответствии с законом наименьшего сопротивления будет смещаться против хода прокатки с некоторой скоростью V¢, а меньшая часть – по ходу прокатки со скоростью V¢¢. И тогда скорость задней части полосы будет (Vв - V¢), а передней (Vв + V¢¢), что и приводит к упомянутому выше неравенству.
Таким образом, опережение образуется за счет смещения частиц металла в направлении прокатки, а отставание - за счет смещения частиц металла против направления прокатки.
С практической точки зрения более важно знать величину Sh, поскольку она непосредственно связана с Vh, а это есть не что иное, как скорость прокатки – один из важнейших параметров продольной прокатки.
Поэтому в дальнейшем будем рассматривать в основном опережение.
Посмотрим, как будет изменяться скорость металла и валков по длине очага деформации. Горизонтальная проекция окружной скорости валков в любой точке очага деформации будет Vв × cosj, где угол j - текущий центральный угол очага деформации, изменяющийся от a до нуля. Тогда горизонтальная проекция окружной скорости валков в плоскости входа будет , а в плоскости выхода - Vв (рис.4.2.).
Скорость металла в очаге деформации будет изменяться от Vн на входе до Vh – на выходе металла из валков. Характер этого изменения определяется, исходя из закона постоянства объема. Через плоскость входа в единицу времени пройдет Fн × Vн металла, а через плоскость выхода – Fk Vh, где Fн и Fк площадь поперечного сечения полосы на входе и выходе из валков, соответственно. Поскольку Fн × Vн = Fk Vh, то . Аналогично можно определить скорость течения металла в любом сечении очага деформации.
Из неравенства Vн < Vв < Vh следует, что в очаге деформации существует такое сечение, где скорость металла и валков совпадает. Это вертикальное сечение называют нейтральным или критическим, а соответствующий ей центральный угол – нейтральным или критическим углом g. Зона от a до g называется зоной отставания, а от g до нуля – зоной опережения (рис. 4.2.).
Таким образом, в зоне отставания валки опережают металл, а в зоне опережения, наоборот, металл опережает валки. Поэтому силы трения в зоне отставания совпадают с направлением прокатки, а в зоне опережения – противонаправлены.
Опережение можно определить по разности скоростей полосы и валков, отнесенной к скорости валков (обычно выражают в процентах):
Но более удобно выражать Sh через величину пути, пройденного полосой (lh) и валками (lв) в единицу времени: , %.
Значение ln и lв легко определить, например, методом керновых отпечатков (рис.4.3.).
Для определения Sh предложено немало формул. Более употребительными являются формула Финка:
и формула Головина-Дрездена: .
Последняя, по сути, является упрощенной формулой Финка.
Для вычисления опережения по этим формулам необходимо знать величину g. Для ее определения И.М.Павлов предложил формулу .
Каковы предельные значения g? При a = 0 и g = 0. При естественном начальном захвате a = b, а . Это его максимальное значение. При a = 2b угол g = 0. При этом и Sh = 0. То есть, в последнем случае на всем протяжении очага деформации имеет место только одна зона – зона отставания, валки буксуют по полосе, процесс прокатки прекращается.
Отчего зависит опережение?
1. При увеличении диаметра валков и опережение увеличивается.
2. При увеличении толщины полосы опережение уменьшается.
3. При увеличении обжатия опережение вначале увеличивается, а затем, достигнув максимума, уменьшается. Это, кстати, следует и из зависимости g от a.
4. При увеличении коэффициента трения и опережение увеличивается. Поэтому все факторы, которые влияют на коэффициент трения, в таком же направлении влияют и на опережение.
Рассматривая скоростные условия прокатки, следует отметить, что кроме скорости прокатки в теории прокатки широко используют понятие скорости деформации. Она зависит от скорости прокатки, но в отличие от нее учитывает еще параметры очага деформации и относительное обжатие.
А.И. Целиков предложил следующую формулу для ее определения: , сек -1 .
Скорость деформации изменяется в широких пределах – от 0,1 сек -1 на обжимных станах до 1000 сек -1 на современных проволочно-мелкосортных станах.
4.2.Уширение при продольной прокатке.
При продольной прокатке происходит уменьшение высоты полосы, а смещенный объем металла может перемещаться в двух направлениях – в продольном (в длину) и в поперечном (в ширину). При этом количество металла, смещаемого в том или ином направлениях, определяется законом наименьшего сопротивления.
Смещение металла в поперечном направлении называется уширением.
Напомним, что наиболее употребляемыми показателями уширения являются: абсолютное уширение , мм, коэффициент уширения и показатель уширения .
Различают три вида уширения: свободное (естественное), ограниченное (стесненное) и вынужденное.
Свободным называется уширение, когда поперечному течению металла ничто не препятствует, кроме сил контактного трения.
Ограниченное уширение имеет место, когда поперечное течение металла встречает какое-либо противодействие (например, создаваемое боковыми стенками калибра или вертикальными валками).
Вынужденное уширение обычно является следствием неравномерного обжатия полосы по ширине, когда вытяжке более обжимаемых участков полосы препятствуют менее обжимаемые, и металл вынужденно смещается в поперечном направлении.
Уширение является одним из основных параметров прокатки, поскольку оно непосредственно влияет на точность, а, следовательно, и на качество проката, особенно сортового. Если толщину профиля можно достаточно точно выдержать путем регулирования зазора между валками, то точность профиля по ширине всецело зависит от уширения. Тем более, что допускаемые отклонения по ширине составляют десятые и даже сотые доли миллиметра, а уширение – миллиметры. Между тем, получить аналитическую зависимость, которая бы функционально отражала влияние различных факторов на уширение, чрезвычайно сложно из-за их многочисленности. Поэтому определение уширения является не столько предметом инженерного расчета, сколько опыта и интуиции калибровщика.
До настоящего времени для практических расчетов используют главным образом эмпирические зависимости, основным достоинством которых является их простота.
Одна из первых зависимостей была предложена жезом, согласно которой величина уширения определяется абсолютным обжатием, а влияние остальных факторов учитывается показателем уширения: . Для различных условий прокатки К изменяется в пределах от 0,35 до 0,48. Однако , как показали более поздние исследования, коэффициент К в значительной степени сам зависит от обжатия, и при может достигать значений 2,5. Тем не менее, при умеренных обжатиях формула Жеза может давать приемлемые результаты.
Более удачной является формула Зибеля-Петрова: , или . Здесь уширение поставлено в зависимость от относительного обжатия и протяженности очага деформации, а К = 0,35…0,45.
Наиболее совершенной является формула Чекмарева:
где К – показатель вида уширения: при свободном уширении он равен единице, при стесненном – 0,6…0,8;
n – степенной показатель. Для узкого очага деформации, когда , он равен единице, для широкого при - двум.
Зависимость уширения от условий прокатки.
1. При увеличении обжатия и диаметра валков уширение возрастает.
2. Дробность деформации способствует уменьшению уширения.
3. При увеличении ширины полосы уширение уменьшается. Поэтому при прокатке широких полос им вообще пренебрегают.
4. Увеличение коэффициента трения способствует росту уширения. Все факторы, влияющие на коэффициент трения, в таком же направлении влияют на уширение.
5. Повышение содержания углерода в стали приводит к уменьшению уширения. Уширение легированных сталей в 1,1…1,6 раза больше, нежели углеродистых.
При анализе зависимости уширения от различных факторов необходимо руководствоваться следующим. Металл в очаге деформации находится в условиях трехосной схемы сжатия: - главное сжимающее напряжение, - среднее главное напряжение и - продольное главное напряжение. При заданном значении течение металла в продольном или поперечном направлениях зависит от соотношения и . Все, что способствует относительному увеличению , приводит к увеличению поперечной деформации, и наоборот.
Вследствие влияния контактных сил трения и ряда других факторов ширина полосы имеет переменное значение по высоте (бочкообразный или вогнутый контур поперечного сечения). Поэтому в ряде случаев необходимо определять среднюю (приведенную) ширину.
Она равна площади поперечного сечения полосы, деленной на ее толщину, то есть, . Соответственно, приведенное уширение будет .
При продольной прокатке уширение может быть позитивным или негативным явлением. В большинстве случаев уширение нежелательно, так как требует непроизводительных затрат рабочего времени и энергии. Но иногда из узкой заготовки необходимо получить широкую полосу. В этом случае уширение выполняет полезную функцию.
Прокатка
Прокатка-способ обработки давлением, при котором металл деформируется путем обжатия его между двумя вращающимся валками (прокатного стана).
Прокатке подвергают до 80 – 90 % всей выплавляемой стали и до 50 – 60 % выплавляемого цветного металла. Широкое применение прокатки объясняется рядом преимуществ ее по сравнению с другими видами ОМД (прессованием, волочением), а также высокой производительностью и меньшей стоимостью изготовления изделий.
Различают три основных вида прокатки (рис.3.6):
Валки вращаются в этом способе в разные стороны. Это наиболее распространенный способ. Применяется для изготовления профильного и листового проката.
2) Поперечную прокатку.
Валки вращаются в одну сторону и придают вращение заготовке, которая формируется вдоль оси валков. Используется для изготовления круглых профилей.
3) Поперечно-винтовую. Валки располагаются под углом друг к другу, вращаясь в разные стороны. Заготовка получает вращательное и поступательное движение. Применяется для получения бесшовных труб и проката с периодическим профилем.
Рис.3.6. Основные способы прокатки: продольная (а), поперечная (б) и поперечно-винтовая (в).
Продукция (сортамент) прокатного производства .
Профиль прокатанного изделия – форма его поперечного сечения;
Cортамент – совокупность различных профилей разных размеров. Сортамент прокатываемых профилей делится на 4 основные группы:
1. Сортовой прокат: профили общего назначения (круглого, квадратного сечения, швеллеры, двутавры и т.п.) и профили специального назначения (рельсы, профили, применяемые в судостроении, строительстве и др. областях).
2. Листовой прокат: фольга (толщиной до 0,2 мм), тонколистовой (0,2…4 мм), толстолистовой (4…160 мм) броневые плиты (до 550 мм).
3. Трубы бесшовные и сварные (например, бесшовные стальные трубы имеют диаметр 30…650 мм, а сварные – диаметром 10…1420 мм).
4. Специальные виды проката: колеса; кольца; зубчатые колеса; периодические профили, у которых форма и площадь поперечного сечения периодически изменятся вдоль оси.
Характеристики деформации при прокатке. При прокатке металл подвергается деформации только на некотором участке, который по мере вращения валков и движения заготовки вперед как бы перемещается по прокатываемому металлу. Этот участок называется очагом деформации.
Дуга АВ – дуга захвата (дуга, по которой валок соприкасается с прокатываемым металлом). Центральный угол α, соответствующий дуге захвата – угол захвата.
Коэффициент вытяжки , где L – длина заготовки после прокатки; l – длина заготовки до прокатки.
Коэффициент обжатия , где H и h – высота заготовки до и после прокатки.
Коэффициент уширения , где B и b – ширина заготовки после прокатки и до прокатки соответственно.
Рис.3.7. Деформация заготовки между валками.
Так как при пластической деформации объём металла практически не изменяется, то можно записать l·H·b = L·h·B, здесь l·H·b – объём заготовки до деформации, L·h·B – объем заготовки после обработки давлением, а значит верным является следующее равенство: λ = β·μ, т. е. металл, обжатый по высоте, идет в вытяжку и уширение.
Условия захвата металла валками. Различают две ситуации: неустановившийся процесс прокатки, когда болванка только подводится к валкам, но не втянута между ними, и установившийся процесс – когда заготовка уже втянута в валки.
а) Неустановившийся процесс (рис.3.8). При соприкосновении заготовки с вращающимися валками последние будут оказывать на нее действие в виде сил N перпендикулярных поверхности валков в точках соприкосновения А, и сил трения Т, направленных по касательной к поверхности валков. Проекции сил N и Т на горизонтальное направление обозначенв соответственно Nx и Tx.
Рис.3.8. Силы, действующие на прокатываемый металл со стороны валков, в начальный момент захвата. |
Валки захватят заготовку, если
где ƒ – коэффициент трения.
Подставим в (3.1) сначала (3.2), а потом (3.3), получим основное условие захвата заготовки
Так как ƒ = T/N = tgβ, где β – угол трения, то условие захвата можно представить, как β > α, т. е., если равнодействующая R направлена вертикально или отклонена влево от вертикали (как на рис.3.8), то захвата не будет.
б) Установившийся процесс . В этом случае передний конец полосы вышел из валков на определенную величину, контакт полосы с валками происходит по всей дуге захвата (рис.3.7), что приводит к изменению соотношения между углами α и β. В этом случае условие захвата:
где n ≈ 2, т. е. при установившемся процессе прокатки захват заготовки происходит примерно в 2 раза легче, чем при неустановившемся.
На коэффициент трения влияют пластичность металла, его температура, скорость вращения валков, материал валков и состояние их поверхности, химический состав металла заготовки.
При горячей прокатке блюмов из слитков на обжимных станах αmax = 24 … 32º; ƒ = 0,45…0,62. При горячей обработке сортового металла αmax = 20 … 25º; ƒ = 0,36…0,47. При горячей прокатке листов и полос αmax = 15 … 20º; ƒ = 0,27 … 0,36. При холодной прокатке листов на валках с чистой поверхностью αmax = 5 … 10º ƒ = 0,009 … 0,18. При холодной прокатке листов на отшлифованных валках со смазкой αmax = 3 … 5º; ƒ = 0,003 … 0,09.
Оборудование и инструмент для прокатки. Инструмент прокатки – валки (рис.3.9), которые делятся на гладкие, применяемые для прокатки листов, лент и ручьевые (калиброванные) для получения сортового проката (квадрат, круг, рельс, швеллер и т. д.). Валки состоят из бочки 3, шейки 2 и трефы 1. Шейки валков служат размещения валков в подшипниках, устанавливаемых в станинах. Трефы – фигурный хвостовик для соединения с приводом станка. Вырез на боковой поверхности калиброванного валка называется ручьём.
Совокупность двух ручьев пары волков образует калибр. Калибры прокатных валков, через которые пропускается металл, по своему поперечному сечению отвечают той форме профиля, которая должна получаться при каждом пропуске. Калибры могут быть открытыми и закрытыми.
Рис.3.9. Ручьевой (а) и гладкий (б) валки.
Для получения какого-либо профиля (проката) необходимо произвести калибровку валков. Калибровка – расчет режима обжатия металла по проходам, конструирование формы и размеров калибров и определение последовательности расположения их на валках. Калибровка – самый важный и трудный вопрос прокатного дела, вследствие сложности процесса деформации металла при прокатке. От правильности расчета и выбора формы последовательных калибров зависит качество прокатываемого профиля.
Размеры сечения исходной заготовки значительно больше размеров сечения готового профиля, и поэтому, как правило, последний почти никогда не удается получить сразу в один проход между валками. Поэтому прокатку проводят в несколько проходов (пропусков). В каждом проходе сечение прокатываемого металла уменьшается, при этом форма и размеры ее постепенно приближаются к требуемому профилю.
В случае прокатки листов и полос (на гладких валках) уменьшение толщины прокатываемого металла в каждом проходе достигается соответствующим сближением валков.
Прокатка слитков или заготовок производится последовательно в калибрах следующих типов:
· Обжимные (вытяжные). Имеют выпуск 5 – 10%. Служат для изготовления из отливки полуфабриката под дальнейшую прокатку. Обжимные калибры: прямоугольные, ромбические, квадратные и овальные.
· Черновые (подготовительные). Имеют выпуск 2 – 4%. Изменяют форму поперечного сечения полупродукта, приближая ее к сечению готового профиля.
· Предотделочные (предчистовые). В ряде случаев эти калибры отсутствуют.
· Отделочные (чистовые). Имеют выпуск 1 – 1,5%. Обеспечивают окончательное формирование профиля.
Выпуск – величина тангенса угла наклона боковых стенок калибра, выраженная в процентах.
Исключительно важное значение имеют расположение калибров в валках. В целях предупреждения возникновения значительных напряжений в металле, а также удара при захвате заготовки калибр должен быть врезан так, чтобы воздействия верхнего и нижнего валков на прокатываемый профиль были примерно одинаковыми. Поэтому естественным является такое расположение калибров, при котором их нейтральные линии находятся посередине между осями верхнего и нижнего валков. Для симметричных профилей (прямоугольных, полосовых, овальных) нейтральной линией калибров служит их горизонтальная ось симметрии. Нейтральная линия фасонных калибров проводится через их центр тяжести. При неправильной калибровке прокатываемый металл или не заполнит весь калибр – тогда размеры профиля не будут соответствовать требуемым, или, наоборот, переполнит калибр – тогда на краях профиля неизбежно появятся заусеницы. Кроме того, в прокатываемом металле могут возникнуть значительные напряжения, которые вызовут трещинообразование или другие виды брака.
Чередующееся сочетание калибров получило название системы калибров (рис.3.10), например, ромб-квадрат, овал-квадрат, ромб-ромб и т. д. Наиболее широко применяемыми системами вытяжных калибров являются системы:
а) Прямоугольных калибров. Эту систему используют для прокатки блюмов в крутые заготовки.
б) Ромб-квадрат и овал-квадрат. Эти для прокатки в более мелкие заготовки.
в) Овал-круг. Эта система для прокатки малопластичных металлов.
Расчет каждой из систем вытяжных калибров проводится по специальным методикам.
Рис.3.10. Схема прокатки стали круглого сечения диаметром 5…20 мм (а), круглого сечения диаметром более 20 мм (б) и квадратного сечения (в) в калибрах определённых систем.
Наиболее удобным для прокатки круглого профиля являются системы: квадрат-овал-квадрат (рис.3.10, а) или квадрат-ромб-квадрат (рис.3.10, б). В обоих случаях квадратные калибры в валках расположены на ребре. Подобное распределение и чередование калибров способствует лучшему обжатию и проработке всех слоев прокатываемого металла. Прокатку изделий квадратного сечения производят в чередующихся калибрах системы ромб-квадрат-ромб (рис.3.10, в).
Основное оборудование прокатного производства – прокатный стан (рис.3.11), состоящий из привода и одной или нескольких рабочих клетей. В привод входит электродвигатель 8, редуктор 7, шестеренная клеть 5, муфты 6 и шпинделей 4. Рабочая клеть состоит из валков 2 и станины 1. В станине имеются нажимные механизмы 3 для изменения расстояния между валками и регулированием взаимного расположения их осей.
Рис.3.11. Схема прокатного стана.
Прокатные станы классифицируют:
1. По числу и расположению валков в рабочих клетях:
а) Станы дуо (рис.3.12 а, б), имеющие 2 валка, вращающиеся в одну (нереверсивные станы) либо в обе стороны (реверсивные станы). Последние позволяют пропускать обрабатываемый металл в обе стороны.
в) Многовалковые станы – шестивалковые, двенадцативалковые и двадцативалковые (рис.3.13 б, в, г).
![]() | Рис.3.12. Схема расположения валков в двухвалковых и трёхвалковых станах. |
Рис.3.13. Схема расположения валков в многовалковых станах.
Конструкции на рис.3.12 (в, г) позволяют применять рабочие валки малого диаметра, благодаря чему растёт давление металла на валки и увеличивается вытяжка.
г) Универсальные станы, имеющие кроме горизонтальных валков также и вертикальные (с одной или обеих сторон).
2. По числу и расположению рабочих клетей:
б) Многоклетьевые (с линейным расположением клетей и с последовательным расположением клетей).
В станах с линейным расположением клетей валки всех клетей кинематически связаны друг с другом и вращаются с одной скоростью, что препятствует значительному увеличению скорости прокатки по мере увеличения длины прокатываемой заготовки.
В станах с последовательным расположением клетей (непрерывные станы) каждая клеть имеет свой привод. Окружная скорость каждой последующей пары валков больше скорости предыдущей пары на строго определенную величину. На непрерывных станах можно прокатывать полосу с натяжением, что увеличивает обжатие.
3. По назначению:
а) Станы для производства полупродукта: блюминги – обжимные станы для обжатия крупных стальных слитков в блюмы; слябинги – обжимные станы для обжатия слитков в слябы. Блюм – заготовка квадратного сечения от 150 150 мм до 450 450 мм. Сляб – полуфабрикат, имеющий прямоугольное сечение толщиной 65 … 300 мм и шириной 600 … 1600 мм.
б) Заготовочные станы для получения полупродукта более мелкого сечения из блюмов или слитков небольшой массы.
в) станы для выпуска готового проката: сортовые, листопрокатные, трубопрокатные и. т. д.
Размер блюмингов, слябингов, заготовочных, рельсобалочных, сортовых станов характеризуется диаметром рабочих валков. Например, стан 500 имеет валки диаметром 500 мм. Для листовых станов основной параметр – длина бочки валка. Например, стан 3000 имеет длину бочки рабочих валков 3000 мм.
Технология производства основных видов проката. Наиболее общая схема технологического процесса прокатки включает следующие операции:
1. Подготовка исходного материала к прокатке;
2. Нагрев металла перед прокаткой;
3. Собственно прокатку;
4. Отделку и контроль качества проката.
Для прокатки блюмов и слябов исходным материалом служат слитки спокойной, полуспокойной или кипящей стали массой до 60 т или из цветных металлов и сплавов массой до 10 т. При прокатке сортового или листового проката исходный материал – блюм или сляб или полупродукт после заготовочного стана.
При подготовке исходного материала к прокатке удаляют поверхностные дефекты: плены, шлаковые включения на слитках или неглубокие трещины, лампасы, закаты, волосовины и др. дефекты. Удаляют их огневой зачисткой, обдиркой на металлорежущих станках, пневматической вырубкой, зачисткой абразивными кругами, электродуговой зачисткой и др. способами. В ряде случаев в технологическом потоке обжимных станов устанавливают машины огневой зачистки для удаления дефектов на прокатанном полупродукте, но чаще всего эти операции выполняются в складских помещениях. Удаление поверхностных дефектов повышает качество поверхности прокатанной продукции, увеличивает выход годного продукта и улучшает технико-экономические показатели работы стана.
Подготовленный исходный материал нагревают в разных нагревательных устройствах. Листы тоньше 2 мм в горячем состоянии прокатывать сложно из-за их быстрого остывания, такие листы, как правило, получают холодной прокаткой (чаще рулонным способом) из горячекатаных листов – заготовок. Количество нагрева оказывает большое влияние на макрокроструктуру и микроструктуру металла, а механические свойства и качество металла – на производительность стана и величину брака.
Нагретый металл транспортируют к стану для прокатки по рольгангу, пропуская по пути через окалиноломатели, в которых окалина дробится при деформировании в валках с небольшими обжатиями.
К отделочным операциям относятся: правка, осуществляемая на роликовых правильных машинах для устранения общей и кромочной неплоскостности; термическая обработка, заключающаяся, как правило, в нормализации или отжиге для перераспределения и снятия остаточных после прокатки напряжений и обеспечения однородности показателей механических свойств в любом сечении проката, термообработка необходима для легированных сталей и для листов или профилей значительной толщины (более 12…14 мм); резка на листы и профили заказанной длины на дисковых или гильотинных ножницах; у листов обрезают также продольную кромку, удаляя узкую полосу, которую может получиться непрямолинейной после прокатки, иметь недостаточную толщину и кромочные дефекты (трещины, расслоения, подрезы и т. п); испытание; взвешивание; маркирование с указанием марки стали, шифра металлургического завода, номера плавки и простановкой клейма ОТК с помощью керна и дублированием накерненной маркировки надписью краской.
Тема: «Захват металла валками»
Цель работы:Научиться определять возможность захвата металла валками при разных условиях и изучить влияние величины обжатия, диаметра валков на захват металла валками.
Продолжительность работы – 2 часа
Методические указания
Захват металла валками при обработке металлов давлением
Процесс прокатки обеспечивается наличием сил трения, действующих между поверхностями валков и металла.
![]() |
![]() |
Рисунок 6 – Условия захвата металла валками для случая |
Рисунок 7 – Условия захвата металла валками для случая |
![]() |
Рисунок 8 – Условия захвата металла валками для случая |
53 |
Угол захвата определяется по формуле:
Максимально допустимые углы захвата для различных случаев прокатки приведены в табл. 25
Таблица 25 – Максимально допустимые углы захвата |
Виды прокатки | Угол захвата в градусах |
Холодная прокатка со смазкой в шлифовальных валках | 3 - 4 |
Холодная прокатка в валках с грубой поверхностью | 5 - 8 |
Горячая прокатка в гладких валках | 15 - 22 |
Прокатка в калиброванных валках: чугунных стальных | 24 - 26 28 - 30 |
Прокатка в валках с накаткой или насечкой | 32 - 36 |
54 |
Определите угол захвата при прокатке полосы с различными обжатиями на рельсобалочном стане и постройте график зависимости угла захвата от обжатия.
Таблица 26 - Исходные данные
№ варианта | Диаметр валков, D,мм | Обжатие, |
1 | 950 | 40; 60; 80; 100; 110 |
2 | 950 | 30; 35; 40; 45; 60 |
3 | 950 | 50; 55; 60; 65; 70 |
4 | 950 | 20; 30; 40; 45; 50 |
5 | 950 | 50; 60; 70; 80; 100 |
6 | 850 | 20; 30; 40; 50; 60 |
7 | 850 | 25; 35; 45; 55; 65 |
8 | 850 | 15; 20; 25; 30; 35 |
9 | 850 | 10; 25; 30; 45; 50 |
10 | 850 | 15; 20; 30; 35; 40 |
55 |
Рисунок 9 - График зависимости угла захвата от обжатия |
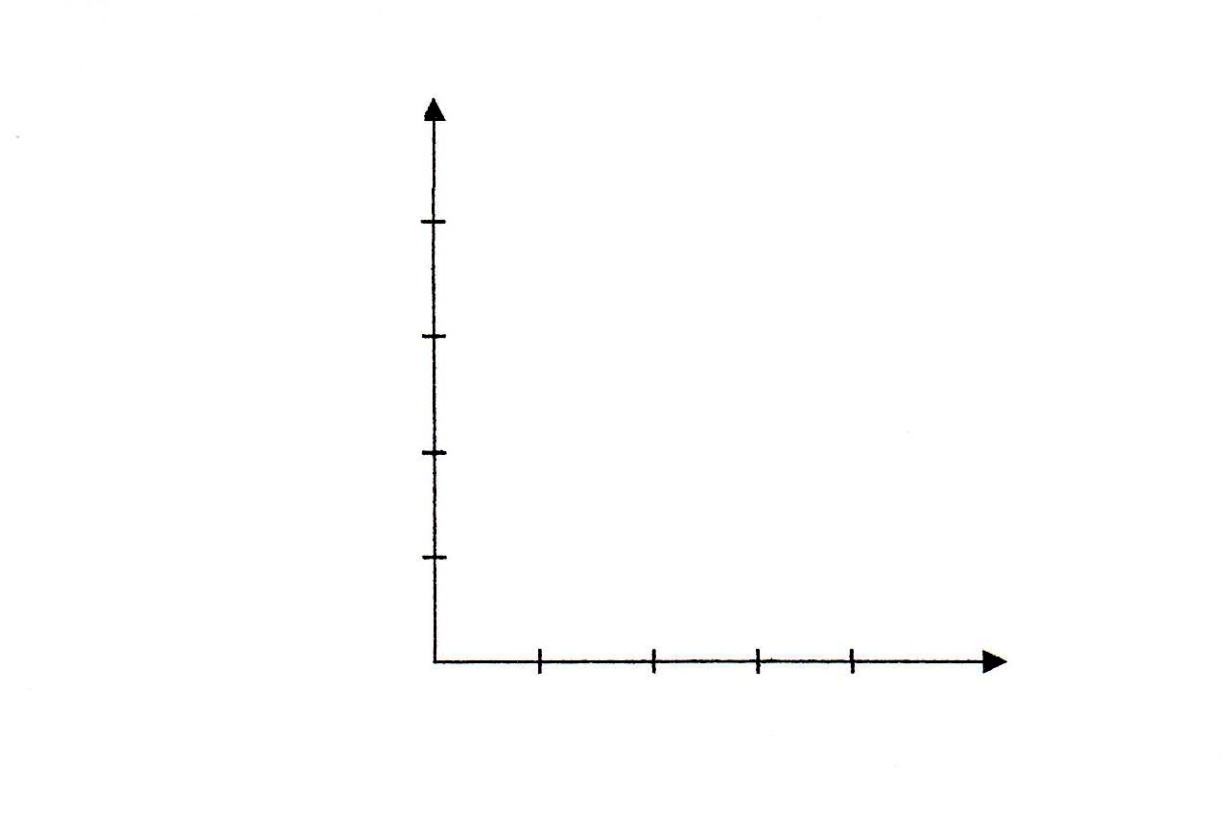
По результатам работы сделать вывод.
Задача №2
Определите угол захвата при прокатке на валках различного диаметра и постройте график зависимости угла захвата от диаметра валков.
Таблица 27 - Исходные данные
№ варианта | Обжатие, | Диаметр валков, D, мм |
1 | 20 | 400; 500; 600; 700 |
2 | 30 | 350; 450; 650; 750 |
3 | 40 | 300; 350; 400; 450 |
4 | 50 | 500; 600; 700; 800 |
5 | 60 | 550; 650; 750; 850 |
6 | 70 | 600; 700; 800; 900 |
7 | 80 | 650; 750; 850; 950 |
8 | 90 | 700; 800; 900; 1000 |
9 | 100 | 950; 1000; 1050; 1100 |
10 | 120 | 1000; 1100; 1200; 1300 |
56 |
D, мм |
Рисунок 10 - График зависимости угла захвата от диаметра валков |
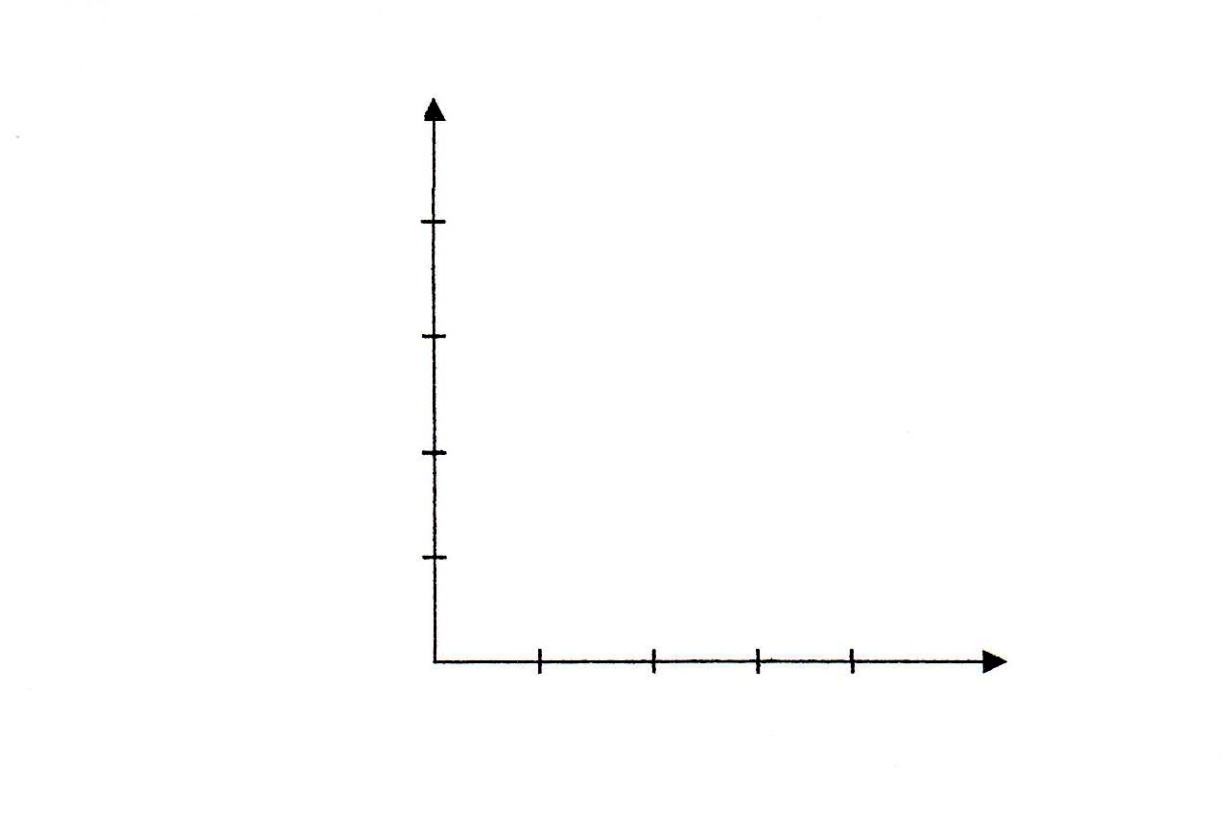
Задача №3
Установите возможен ли захват металла валками и приведите схему действия сил на металл в момент захвата.
Цель работы: Научиться определять возможность захвата металла валками при разных условиях и изучить влияние величины обжатия, диаметра валков на захват металла валками.
![]() |
![]() |
Рисунок 6 – Условия захвата металла валками для случая |
Рисунок 7 – Условия захвата металла валками для случая |
![]() |
Рисунок 8 – Условия захвата металла валками для случая |
53 |
№ варианта | Диаметр валков, D ,мм | Обжатие, |
1 | 950 | 40; 60; 80; 100; 110 |
2 | 950 | 30; 35; 40; 45; 60 |
3 | 950 | 50; 55; 60; 65; 70 |
4 | 950 | 20; 30; 40; 45; 50 |
5 | 950 | 50; 60; 70; 80; 100 |
6 | 850 | 20; 30; 40; 50; 60 |
7 | 850 | 25; 35; 45; 55; 65 |
8 | 850 | 15; 20; 25; 30; 35 |
9 | 850 | 10; 25; 30; 45; 50 |
10 | 850 | 15; 20; 30; 35; 40 |
55 |
Рисунок 9 - График зависимости угла захвата от обжатия |

№ варианта | Обжатие, | Диаметр валков, D , мм |
1 | 20 | 400; 500; 600; 700 |
2 | 30 | 350; 450; 650; 750 |
3 | 40 | 300; 350; 400; 450 |
4 | 50 | 500; 600; 700; 800 |
5 | 60 | 550; 650; 750; 850 |
6 | 70 | 600; 700; 800; 900 |
7 | 80 | 650; 750; 850; 950 |
8 | 90 | 700; 800; 900; 1000 |
9 | 100 | 950; 1000; 1050; 1100 |
10 | 120 | 1000; 1100; 1200; 1300 |
56 |
D , мм |
Рисунок 10 - График зависимости угла захвата от диаметра валков |

Таблица 28 - Исходные данные
57 |
Задача
Определить, возможен ли захват металла валками, если диаметр валков
D = 500 мм, толщина заготовки до пропуска = 120 мм, температура в данном пропуске t = 950в чугунных валках.
1) Определяем коэффициент трения
2) Определяем угол трения
3) Определяем абсолютное обжатие
4) Определяем угол захвата
Захват металла валками произойдёт, так
58 |
Задача №1
Установите возможен ли захват металла валками, если коэффициент трения при захвате f = 0,484, диаметр валков D = 1000 мм, высота очага деформации на входе металла в валки = 500 мм. Привести схему действия сил на металл в момент захвата.
Установите возможен ли захват металла валками, если высота очага деформации на входе металла в валкиD = 450 мм, коэффициент трения при захвате металла валками (валки стальные) f = 0,4. Осуществится ли захват металла, если при прочих равных условиях прокатку вести в чугунных валках? Привести схемы действия сил на металл в момент захвата раската стальными и чугунными валками.
Коэффициент трения при захвате металла чугунными валками f = 0,32. Установите, возможна ли прокатка, если высота очага деформации на входе металла в валки = 110 мм, диаметр валков D = 530 мм. Осуществится ли захват металла, если при прочих равных условиях прокатку вести на стальных валках? Привести схемы действия сил на металл в момент захвата раската стальными и чугунными валками.
Задача№4
D = 650 мм, материал валков – сталь. Температура металла, задаваемого в валки t = 1200Читайте также: