Степень автоматизации сварочного оборудования
Обновлено: 14.05.2024
Требования к процессу и режимам сварки пластмассовых труб и соединительных деталей встык НИ, к оборудованию для такой сварки изложены в следующей НД:
- СП 42–103–2003;
- ГОСТ Р ИСО 12176–1–2011 «Трубы и фитинги пластмассовые. Оборудование для сварки полиэтиленовых систем. Часть 1. Сварка встык плавлением» [6] (основан на международном стандарте ISO 12176–1:2006 Plastics pipes and fittings — Equipment for fusion jointing polyethylene systems — Part 1: Butt fusion [7]);
- ГОСТ Р 55276–2012 «Трубы и фитинги пластмассовые. Процедуры сварки нагретым инструментом в стык полиэтиленовых (ПЭ) труб и фитингов, используемых для строительства газо- и водопроводных распределительных систем» [8] (основан на международном стандарте ISO 21307:2011 Plastics pipes and fittings — Butt fusion jointing procedures for polyethylene (PE) pipes and fittings used in the construction of gas and water distribution systems [9]) .
Виды оборудования для сварки НИ. Требования к оборудованию для сварки нагретым инструментом.
Состав и виды аппаратов для стыковой сварки.
Конструктивно аппараты для сварки встык, независимо от производителя конкретного оборудования, состоят из следующих основных частей (рис. 19) .
Центратор (рис. 19) — станина с четырьмя металлическими захватами (хомутами) для зажима свариваемых труб и соединительных деталей. Два из них подвижно (подвижный суппорт) и два неподвижно укреплены на направляющих — стальных штангах.
В аппаратах, используемых для строительства трубопроводов, подвижный суппорт приводится в движение гидросистемой (см. ниже). В соответствии с видом свариваемых элементов (труба/труба, труба/деталь и т. п.) в некоторых аппаратах расстояние между подвижными зажимами может регулироваться при помощи двух боковых гребенок со стопорными отверстиями или же второй подвижный зажим может сниматься.
В моделях аппаратов, предназначенных для сварки труб большого диаметра (> 315 мм), станина может устанавливаться на колесное или гусеничное шасси (Рис. 21).
Редукционные вкладыши (полукольца) — съемные детали, обеспечивающие надежную фиксацию в зажимах (подвижных и неподвижных) во время сварки труб и/или деталей с диаметром, отличным от максимально допустимого для данной модели аппарата. Вкладыши закрепляются в зажимах изнутри болтами или защелками. Сделаны из алюминиевого сплава, их наружный диаметр соответствует внутреннему диаметру зажимов, а внутренний — наружному диаметру свариваемых труб и/или деталей. Обычный ряд внутренних диаметров вкладышей: 63, 75, 90, 110, 125, 140, 160, 180, 200, 225, 250, 280, 315, 355, 400, 500, 630, 710, 800, 1000, 1200, 1400, 1600 мм и т. д. соответствует стандартам на свариваемые трубы и детали.
Торцеватель (рубанок) (рис. 20) — вращающееся дисковое устройство с одним или несколькими лезвиями (резцами, ножами) с приводом от электромотора для механической обработки (торцевания) концов свариваемых встык труб и соединительных деталей. Контакт между свариваемыми частями труб и торцевателем обеспечивается давлением подвижных зажимов.
Торцеватель состоит из следующих элементов:
- корпус;
- электромотор;
- два вращающихся диска с лезвиями;
- концевой выключатель, срабатывающий при установке торцевателя на станину центратора;
- колесо управления скоростью вращения;
- кнопка включения торцевателя;
- фиксатор кнопки включения.
На торцевателе есть крепление к направляющим аппарата для удержания при работе. Концевой выключатель препятствует вращению дисков торцевателя вне сварочного аппарата.
У большинства торцевателей лезвия заточены с обеих сторон. Перевернув, можно использовать их вторую режущую кромку. Чтобы не менять геометрию ножей, их не рекомендуется затачивать. После использования торцеватель следует поместить в защитный кожух.
![]() | ![]() |
Рис. 19. Общий вид аппарата для сварки полимерных труб встык НИ с ручным управлением и его составляющих. | Рис.20. Внешний вид торцевателя. |
Нагревательный инструмент (нагреватель, НИ) (рис. 22) — массивный металлический диск со встроенной электрической спиралью, диаметром, превышающим наибольший диаметр свариваемых на данном аппарате труб. Служит для нагрева и оплавления свариваемых поверхностей труб и соединительных деталей. Обе его стороны (зеркала), контактирующие со свариваемыми поверхностями, покрыты специальным тефлоновым покрытием для предотвращения налипания расплава полимера.
Одно из основных требований к НИ — автоматическое поддержание его температуры во время сварки, которая не должна отклоняться от значения, установленного в соответствии с выбранным режимом сварки, более, чем на 10 °C. Для этого нагреватель снабжен встроенным терморегулятором, автоматически ее поддерживающим, и термометром, показывающим эту температуру.
Ранее выпускались аппараты с нагревом от газовой горелки.
![]() | ![]() |
Рис. 21. Сварочный аппарат высокой степени автоматизации на гусеничном шасси | Рис. 22. Нагреватель с термометром для контроля его температуры, установленный в центраторе. |
Гидросистема — оборудование, обеспечивающее постоянный уровень необходимого давления на свариваемых поверхностях с возможностью его точной регулировки на всех стадиях сварочного процесса. Давление в гидросистеме контролируется по встроенному манометру. Перед включением гидросистемы следует убедиться в соответствии источника питания ее электрическим характеристикам.
Блок электропитания — через него осуществляется подача питающего напряжения на составные части аппарата, обычно 220 или 380 В. В блок встроены электрические разъемы для подключения различных потребителей, терморегулятор нагревателя и выключатель для защиты аппарата и пользователя. При подключении блока к источнику питания следует убедиться в соответствии источника электрическим характеристикам самого блока, а также в том, что верхняя крышка блока закрыта.
Электронный блок контроля (управления) и регистрации — оборудование, осуществляющее для аппаратов средней и высокой степени автоматизации функции регистрации, контроля и управления параметрами сварки (рис. 23, 24) .
В базовую комплектацию сварочного аппарата должны входить также:
Для качественной сварки очень важно стабильное электропитание соответствующего напряжения сварочного аппарата и другого используемого оборудования. Наиболее надежным источником электроэнергии для сварочных работ является автономный электрогенератор, обычно на основе двигателя внутреннего сгорания (Рис. 25) или дизельного мотора.
Мощность электрогенератора должна превосходить суммарную мощность сварочного и вспомогательного электрооборудования примерно на 15–20%. Во время сварки не рекомендуется подключать к электрогенератору какое–либо дополнительное оборудование. При использовании удлинителя для подключения сварочного аппарата параметры удлинителя (сечение проводов, электрическое сопротивление, состояние изоляции и т. п.) должны обеспечивать безопасную передачу достаточной электрической мощности от электрогенератора. Эксплуатация и техническое обслуживание электрогенератора (заправка топливом, маслом, проверка и т. п.) должны производиться согласно инструкциям производителя.
![]() | ![]() |
Рис. 25. Бензиновый электрогенератор. | Рис. 26. Оборудование для резки труб из термопластов. а) Секатор, б) Гильотина, в) Роторная пила. |
Оснастка, приспособления и инструмент, применяемые для сварки полимерных труб НИ, правила их применения.
Помимо основного сварочного оборудования при сварке НИ используются и дополнительные инструменты и приспособления.
Секаторы, гильотины, роторные электрические пилы (рис. 26 а, б, в) и другие инструменты используются для резки свариваемых труб.
Струбцины, скругляющие накладки (рис. 27 а, б) или деовализаторы различных конструкций используют для устранения недопустимой овальности труб перед сваркой.
Для исправления кривизны труб, смотанных с бухты или барабана, используют гидравлические выпрямители (рис. 28) .
Опорные ролики (роликовые опоры) различных конструкций (рис. 31) — приспособление для опоры двигающейся полимерной трубы с целью уменьшения трения трубы при движении подвижных зажимов, нагрузки на гидросистему в процессе сварки и повышения к. п.д. сварочного аппарата.
Гратосниматель (рис. 33) — устройство для снятия сварочного грата с внутренней или наружной поверхности сваренных труб (по требованию заказчика или в соответствии с используемой технологией монтажа) .
В случае необходимости протокол сварки может быть распечатан из памяти блока регистрации (для ССА) или управления (для СВА) прямо на месте проведения работ с помощью портативного принтера (рис. 35) .
Для целей контроля необходимы следующие измерительные инструменты:
- для проведения входного контроля: измерительная рулетка, толщиномер,
- для измерения зазоров в стыке после торцевания: лепестковый щуп (рис. 28),
- для измерения размеров грата: штангенциркуль и/или набор контрольных шаблонов , изготовленных согласно требований НД.
Для маркировки стыков необходим несмываемый водой маркер (рис. 32) или металлическое клеймо (рис.34) .
Для обезжиривания и очистки зеркала нагревателя и торцов труб — одноразовые салфетки (рис. 36) или чистый хлопчатобумажный лоскут и обезжириватель .

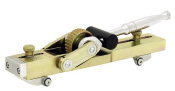
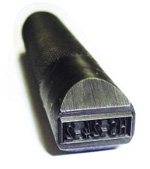
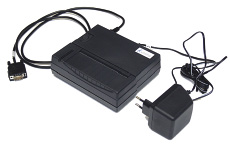
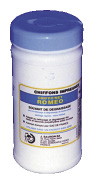
Технические характеристики сварочного оборудования для сварки полимерных труб НИ в зависимости от степени автоматизации и фирм — поставщиков оборудования для сварки полимерных труб НИ.
Характеристики аппаратов для стыковой сварки
Аппараты для стыковой сварки НИ оценивают по таким показателям, как:
- способ управления процессом сварки
(степень автоматизации), - диапазон диаметров свариваемых труб,
- возможность коррекции технологических параметров,
- характеристики силового привода,
- потребляемая мощность,
- масса,
- габаритные размеры,
- транспортабельность,
- надежность в работе.
Производители выпускают аппараты разных типоразмеров для различных диапазонов диаметров свариваемых труб. Обычно модели соответствуют следующим диапазонам диаметров труб (в мм): 40÷160, 63÷250, 90÷315, 225÷500, 315÷630, 400÷800, 500÷1000, 630÷1200, 1000÷1600. Для каждого типоразмера могут выпускаться сварочные аппараты как с ручным управлением, так и ССА и СВА.
Аппараты, используемые в строительстве, имеют гидравлический привод зажимов центратора. Аппараты, используемые для сварки отводов для объектов СК в цеховых условиях, обычно имеют электрический привод зажимов центратора, позволяющий сваривать полимерные трубы под различными углами.
Если диаметр трубопровода невелик, а сам трубопровод не является опасным производственным объектом, привод подвижных зажимов может быть ручным.
В аппаратах, предназначенных для изготовления с помощью сварки НИ соединительных деталей в производственных условиях, привод подвижных зажимов может осуществляться с помощью электромоторов.
Требования НД к аттестации, хранению, перевозке, эксплуатации и обслуживанию оборудования при производстве сварочных работ на технических устройствах групп ГО и СК.
Аттестация оборудования — элемент САСв. Аттестация оборудования проводится согласно РД 03–614–03 в целях проверки его возможности обеспечивать заданные технологические характеристики для различных способов сварки, определяющие требуемое качество сварных соединений при изготовлении, монтаже, ремонте
и реконструкции технических устройств, применяемых
на опасных производственных объектах.
Процедура аттестации сварочного оборудования включает:
- Оформление и подачу документов Заказчиком в аттестационный центр;
- Разработку аттестационным центром Программы испытаний, которая согласовывается с Заказчиком;
- Проведение аттестационным центром испытаний
- в соответствии с программой;
- Оформление аттестационным центром Протокола аттестации и предоставление для экспертизы в НАКС;
- Выдачу НАКС свидетельства об аттестации сварочного оборудования при положительном заключении экспертизы протокола аттестации.
Храниться сварочное оборудование и приспособления должны в сухом закрытом помещении, в чистом виде, механические движущиеся части должны быть смазаны. При длительном хранении необходимо слить масло из гидросистемы.
При перевозке в кузове автомашины следует закреплять оборудование во избежание его повреждения. Самоходное гусеничное оборудование для сварки труб большого диаметра должно перевозиться на специальных тягачах.
При хранении и перевозке необходимо также соблюдать инструкции производителя сварочного оборудования.
Эксплуатироваться сварочное оборудование должно согласно инструкциям по эксплуатации, без превышения рекомендованных параметров, с использованием рекомендованных производителем марок гидравлического масла, при условии своевременного технического обслуживания (обычно 1 раз в год) в специализированных сервисных центрах.
Для ГО — сварочное оборудование проходит систематическое ежегодное сервисное обслуживание предприятием фирмы-производителя этого оборудования либо представителем фирмы, имеющим допуск к сервисному обслуживанию этого оборудования. Дата последующего сервисного обслуживания должна, как правило, автоматически вводиться в протоколы сварки
Степени автоматизации аппаратов для сварки пластиковых труб
Сварка пластиковых труб встык нагретым инструментом используется в промышленном и гражданском строительстве для монтажа трубопроводов различного назначения. Прочность шва сопоставима с характеристиками цельных деталей. Технология процесса зависит от степени автоматизации сварочного оборудования : сварка с ручным управлением СР, средней степенью автоматизации ССА, высокой степенью автоматизации СВА. Классификация оборудования определена в СП 62.13330.2011 и ГОСТ Р ИСО 12176-1-2011.
Аппараты с ручным управлением
Процесс контролирует оператор. Оборудование со степенью автоматизации СР требует от сварщика опыта, знаний, умения пользоваться сварочными таблицами. В некоторых моделях оборудования встроена функция протоколирования. Никаких автоматических систем контроля, оповещения не предусмотрено.
- сварщик самостоятельно определяет момент окончания этапа оплавления, визуально контролируя высоту грата и учитывая толщину стенки трубопровода;
- давление холостого хода измеряют перед каждым соединением.
Требования к приемке швов, выполненных на аппаратах СР, самые жесткие. Контроль стыков проводят в объеме 100 %. Наиболее ответственные участки, например, соединения с коллекторами, трубопроводы рядом со зданиями, испытывают физическими методами.
Аппараты со средней степенью автоматизации
- время начала плавления определяется визуально или фиксируется автоматически в зависимости от модели;
- давление холостого хода измеряется компьютером и передается на блок управления.
Важно: аппарат ССА проводит измерения и сопоставляет их с загруженными алгоритмами, но он не управляет исполнительными устройствами. Сварной шов формирует оператор. Контроль качества проводят в отношении 40 % соединений.
Аппараты с высокой степенью автоматизации
Модели СВА (CNC) называют автоматическими. Блок управления оборудованием не только просчитывает режим сварки, но и регулирует работу гидравлики, нагрев зеркала. Автоматически формируется протокол процесса. Приспособление для извлечения сварочного зеркала может быть встроенным или устанавливается опционально. Высокая степень автоматизации аппаратов для сварки труб наиболее востребована для монтажа газопроводов и распределительных сетей.
Модели СВА отличаются от ССА следующими функциями:
- предустановленные программы с информацией о режимах сварки, учитывают вид полимера, температуру окружающего воздуха, геометрию трубы;
- автоматическое управление сварочным процессом.
В задачи оператора входит подготовка труб и оборудования к монтажу, включение установки, наблюдение за процессом. Рабочий должен проверить основные регистрируемые параметры процесса:
- температура нагревательного элемента;
- давление и время нагрева, оплавления, осадки, охлаждения;
- продолжительность технологической паузы;
- марка полимерного материала;
- диаметр труб;
- температура воздуха.
Проверка качества сварных швов проводится в отношении 20 % соединений. Если аппарат аттестован в НАКС, то физические методы контроля не применяются.
Независимо от степени автоматизации сварочного оборудования для полиэтилена или полипропилена оператор после завершения процесса должен предоставить протокол. В моделях ССА и СВА он формируется автоматически. Помимо рабочих характеристик оборудования в протоколе указывают дату и время сварки, имя оператора, номер соединения, название строительного объекта, марку аппарата. Согласно ГОСТ Р ИСО 12176-1-2011 в оборудовании с автоматическим управлением система должна дополнительно записывать такие параметры как время оплавления торцов, давление смыкания торцов, временные интервалы между удалением нагретого инструмента и сведением торцов, продолжительность сжатия.
Степень автоматизации цеховых аппаратов стыковой сварки
При соблюдении технологии производства фасонных изделий прочность готового соединения – не ниже прочности исходной трубы. Поэтому прочность сварных фасонных изделий – не ниже прочности исходной трубы или литых фасонных изделий. Однако, нарушить технологию совсем несложно, и не всегда это можно обнаружить по внешнему виду готового шва.
Поэтому, согласно действующему законодательству, для сварки трубопроводов повышенной опасности (в частности, газопроводов) должны использоваться гидравлические аппараты с возможностью, как минимум, протоколирования параметров сварочного процесса. Как максимум – с полной автоматизацией самого процесса. При сдаче объекта распечатка т.н. паспорта каждого сварного шва – обязательна, в т.ч. и каждого сварного шва фасонного изделия.
При прокладке водопроводов протоколирование параметров сварочного процесса законодательством не предписывается. Однако если вы хотите быть уверены, что вашему предприятию не придется отвечать за брак, допущенный персоналом, качество выполненной сварки лучше контролировать с помощью протоколов сварных швов.
Гидравлические аппараты стыковой сварки условно разделяются на 3 категории по степени автоматизации:
Неавтоматизированные
Управление аппаратом – ручное, с помощью органов управления на панели управления, которая расположена на основной машине. Параметры сварки (температура, давление, время) задаются оператором вручную, по сварочным таблицам. Никакие обратные связи не предусмотрены. Протоколирования нет.
Средняя степень автоматизации
На внешний блок автоматизации LDU 2006 заводятся две обратные связи – по давлению масла в гидравлической системе и по температуре зеркала (от термодатчика сварочного зеркала). На основной машине предусмотрены необходимые разъемы, а в комплект поставки LDU 2006 включены все необходимые кабели. Датчик «положения каретки» не используется, этот параметр не контролируется.
Для повышения точности автоматической навигации по сварочному процессу в LDU 2006 используется дополнительная обратная связь – по давлению масла в обратной ветке гидравлической системы. Резкое повышение давления в этой ветке понимается автоматикой как раскрытие центратора, т.е. разведение труб.
Блок автоматизации не управляет сварочным процессом непосредственно. На основании введенных параметров свариваемой трубы, измеренного пассивного сопротивления, а также замера температуры воздуха блок автоматизации рассчитывает оптимальное значение каждого параметра сварочного процесса, указывает его на дисплее на каждом этапе сварки и следит за тем, насколько точно оператор выполняет все предписания.
По окончании сварки блок автоматизации сохраняет информацию о рекомендованных и фактических параметрах сварочного процесса в своей памяти с возможностью распечатки на встроенном или на внешнем принтере или переноса в компьютер для обработки и хранения.
Высокая степень автоматизации
Модуль автоматизации CNC для цеховых машин серии PL выполнен в отдельном модуле с панелью управления. Он значительно сложнее модуля автоматизации CNC для полевых машин серии PT.
Модуль автоматизации не только рассчитывает оптимальные значения параметров сварки, но также непосредственно регулирует температуру сварочного зеркала, управляет гидроприводом сведения/разведения трубных зажимов, торцевателя, сварочного зеркала, а также включением/выключением торцевателя. Для этого в модуль автоматизации заведены обратные связи от бесчисленных датчиков и концевых выключателей машины. В результате после установки трубных сегментов в зажимы весь сварочный процесс происходит в буквальном смысле автоматически.
Инструкция по технологии стыковой сварки полиэтиленовых труб
При монтаже трубопровода свариваются одна неподвижная труба (ранее смонтированная часть трубопровода) и одна подвижная труба (очередной хлыст). При сварке стыковых соединений труб на цеховых машинах, как правило, обе трубы подвижные. В любом случае, чтобы выполнить режимы стыковой сварки, необходимо обеспечить соосность труб, а также возможность прижима торцов труб к нагревателю и затем друг к другу с контролируемым усилием. Для этой цели служит центратор (рис.2).
Центратор – конструкция, состоящая из двух или более направляющих и двух или более хомутов для крепления свариваемых труб (Определение ГОСТ Р ИСО 12176-1). В непрофессиональных переводах иностранных инструкций к сварочным аппаратам встречаются термины «базовая машина» или «основная машина» (от английского «Basic machine»).
Функции центратора – обеспечение соосного крепления труб, исправление овальности труб, перемещение одной или обеих труб вдоль оси, обеспечение контролируемого усилия прижима торцов труб к нагревателю или друг к другу.
5.2 Гидравлический агрегат
Гидравлический агрегат – необходимый компонент аппарата для сварки полиэтиленовых труб с гидравлическим приводом центратора . Гидравлический агрегат подключается к центратору двумя шлангами с т.н. быстроразъемными соединениями (БРС) и создает контролируемое давление масла.
В самом массовом (неавтоматизированном) варианте органы управления насосом и клапанами находятся на верхней панели агрегата (рис.3), в случае цеховых машин – на передней панели машины. Переключение рычага влево или вправо включает насос агрегата на разведение или сведение труб. Регулировочный клапан служит для точной регулировки создаваемого давления. Байпасный клапан – для быстрого сброса давления.
Чем сложнее машина, тем больше функций у гидравлического агрегата. В самом простом случае небольшой полевой машины (например, PT-315) гидравлический агрегат только обеспечивает осевое перемещение подвижной трубы. На более сложных полевых машинах гидравлика может также закрывать/открывать и запирать/отпирать хомуты центратора, а также поднимать/опускать боковые роликовые упоры труб. На цеховой машине PL-630 гидравлический агрегат также управляет вводом торцевателя и сварочного зеркала в зону сварки.
Для визуального контроля величины создаваемого агрегатом давления служит стрелочный манометр. Как правило, на гидравлические агрегаты машин для сварки полиэтиленовых труб ставят маслонаполненный манометр – для плавного движения стрелки. Шкала манометра заполнена маслом, с небольшим пузырьком воздуха. Не удивляйтесь, это нормально.
5.3 Торцеватель
Торцеватель предназначен для обработки торцов труб непосредственно перед сваркой стыкового соединения.
Основу торцевателя составляют два параллельных металлических диска с радиально расположенными ножами. Вращаясь между прижатыми к нему трубами, такой «дисковый рубанок» выравнивает торцы труб и обеспечивает идеальное их прилегание друг к другу (рис.4).
В качестве привода торцевателя на малых механических сварочных аппаратах (до Ø 110 мм) чаще всего используют рычаг с храповиком (рис.10). Для труб малого диаметра этого вполне достаточно, а экономия – существенная.
На механических и гидравлических аппаратах среднего размера (обычно до Ø 355 мм) в качестве привода торцевателя используют электродрели с коллекторным двигателем (рис.9). И мощность подходящая, и серийные электродрели стоят недорого.
На гидравлических сварочных машинах от Ø 500 мм и выше мощность электродрели для торцовки труб недостаточна. Используют асинхронный мотор-редуктор (рис.11), хотя он и подороже.
На профессиональных гидравлических сварочных машинах торцеватель, как правило, снабжен микроконтактом безопасности, который замыкается только тогда, когда торцеватель установлен на центратор. Ни на подставке, ни при переноске торцеватель включить нельзя.
5.4 Нагреватель
«Нагреватель», или «Сварочное зеркало» – и есть тот самый «нагретый инструмент» для «сварки встык нагретым инструментом». Инструмент состоит из плоского алюминиевого блина (чаще всего круглого), в который залиты один или несколько электрических нагревательных элементов. Алюминиевый блин покрыт тефлоном, чтобы нагретый инструмент не прилипал к торцам труб. К блину крепятся рукоятки для переноски. Терморегулятор находится в рукоятке или вынесен в отдельный блок, к которому подключается сварочное зеркало.
Термин «сварочное зеркало» - старый и устоявшийся, но в ГОСТ Р ИСО 12176-1 его почему-то заменили на «нагреватель». В непрофессиональных переводах инструкций к аппаратам можно встретить термин «нагревательная пластина» (от английского “heater plate”). Называют также «нагревательным элементом». Это уж совсем двусмысленно. Нагревательным элементом инструмента для сварки ПНД труб чаще всего являются ТЭНы (трубчатые нагревательные элементы), причем в некоторых моделях сварочных зеркал ТЭНы заменяемые.
Нагретый инструмент может быть подвижно закреплен на центраторе (рис.9) с возможностью быстро откинуть его из зоны сварки одним движением руки. Очень полезно для сварки ПВХ труб , поскольку позволяет до минимума сократить технологическую паузу. Гораздо чаще нагретый инструмент и торцеватель находятся на специальной подставке (рис.11) – это чтобы весь сварочный комплект удобнее было транспортировать. Большие сварочные зеркала снабжены такелажными кольцами, чтобы можно было поднимать каким-то подъемником (рис.5). Кроме того, большие сварочные зеркала имеют форму не диска, а кольца – это для уменьшения массы нагретого инструмента и экономии алюминия.
В любом случае, система крепления нагретого инструмента на центраторе не обеспечивает его жесткой фиксации, как у торцевателя. Обеспечивает только более-менее однозначное положение инструмента между прижатыми торцами труб.
5.5 Редукционные вкладыши
Хомуты центратора , предназначенные для фиксации труб, имеют внутренний диаметр, соответствующий самой большой трубе, которую этот конкретный аппарат может варить.
Однако каждый сварочный аппарат рассчитан на определенный рабочий диапазон номинальных диаметров DN – например, от 90 мм до 315 мм. Если хомуты имеют внутренний диаметр 315 мм, то для фиксации труб любого меньшего диаметра необходимо установить в хомуты т.н. редукционные вкладыши соответствующего размера.
Чаще всего редукционные вкладыши крепятся к хомутам болтами (рис.6). На некоторых моделях сварочных аппаратов предусмотрена система быстрого крепления вкладышей на защелках. Это имеет смысл только при сварке труб небольшого диаметра, когда сам сварочный цикл имеет небольшую продолжительность. Если для стыковой сварки толстостенной ПНД трубы Ø 630 мм требуется 2 часа, то какая вам разница, сколько занимает смена вкладышей – 5 минут или 30 секунд?
Вкладыши гидравлических аппаратов имеют серьезную ширину, производятся с применением высокоточной мехобработки и стоят вполне серьезных денег. Поэтому в стандартный комплект аппарата не включены. Если вам нужно варить только диаметры 315 мм и 250 мм, то зачем вы должны платить за десяток других комплектов вкладышей?
На механических аппаратах, как правило, вкладыши проще – очень часто просто штампованные из листовой стали. И, естественно, меньше. Поэтому в комплектацию механического сварочного аппарата обычно входят вкладыши всего рабочего диапазона диаметров. Для цены аппарата это погоды не делает.
5.6 Электрокран
Когда сваривают трубы большого диаметра, требуется подъемное устройство для поднятия торцевателя, сварочного зеркала и верхних половинок трубных хомутов. Поэтому с большими сварочными машинами в качестве опции предлагается электрокран, который крепится к центратору и управляется с дистанционного пульта (рис.7).
С другой стороны, при монтаже трубопроводов больших диаметров в любом случае требуется какой-то автокран (рис.8). Его часто используют также для манипуляций с торцевателем и сварочным зеркалом.
5.7 Варианты привода центратора
Обеспечить перемещение и усилие прижима, теоретически, можно с помощью любого привода – механического, гидравлического, пневматического, электрического, электромагнитного… Тут всё дело в удобстве работы, в надежности оборудования, а также в его технологичности и цене. В процессе эволюции на полевых машинах выжили всего 2 типа привода – механический и гидравлический. На цеховых машинах изредка встречается пневматический привод, но это скорее исключение. Механический привод имеет 2 основные разновидности – приводной рычаг и приводной винт, поэтому можно говорить о трех типах привода центратора , каждый из которых имеет свои достоинства и недостатки.
Центратор с приводным рычагом
![]() |
---|
Рис. 9 Центратор с приводным рычагом |
- Очень быстрое перемещение подвижной трубы, благодаря чему продолжительность фазы 3 (технологическая пауза) можно сократить до 1-2 сек. Это делает возможным даже сварку труб из ПВХ (см.п.10.5).
- Приводной рычаг – самое недорогое техническое решение.
- Неудобно использовать в траншее, колодце или пр. стесненных условиях.
- Крайне трудно создать сварочное усилие более 70-80 кгс. Принимая во внимание, что требуемое сварочное усилие пропорционально площади сечения свариваемой трубы (см.п.8.2.4), для ПЭ труб диаметром более 160 мм приходится вводить большие ограничения по толщине стенки.
Чтобы сварочные аппараты с приводным рычагом нашли свою нишу на рынке, конструкторы оборудования подчеркнули их достоинства и ограничили применение:
- Для снижения цены трубные хомуты сделали не парными, а одинарными, дополнив каждый хомут боковым упором для трубы.
- Раз уж в траншее или навесу использовать все равно неудобно, сделали более удобной сварку на открытой местности. Для этого добавили рабочий стол-раму, а торцеватель и сварочное зеркало подвижно закрепили на центраторе .
- Ограничили диаметры и толщину стенки свариваемых труб.
Центратор с приводным винтом
![]() |
---|
Рис. 10 Центратор с приводным винтом |
- Компактная конструкция, позволяет работать в стесненных условиях и навесу.
- Приводной винт – недорогое техническое решение сравнительно с гидравликой.
- При разработке аппарата приходится искать компромисс между скоростью перемещения подвижной трубы и создаваемым сварочным усилием. Для толстостенных ПНД труб диаметром более 160 мм найти хороший компромисс не удается – либо сварочного усилия не хватает, либо подвижная труба движется медленно, из-за чего фаза 3 (технологическая пауза) получается слишком длинная.
Чтобы подчеркнуть достоинства сварочных аппаратов с приводным винтом, их часто делают с расчетом на работу в колодце или навесу, для чего максимально уменьшают размеры и вес. Торцеватель и сварочное зеркало на центраторе не закрепляют, а выносят на отдельную подставку.
Центратор с гидравлическим приводом
![]() |
---|
Рис. 11 Центратор с гидравлическим приводом |
- Возможность создания сколь угодно большого сварочного усилия. Позволяет сваривать трубы любого диаметра, с любой толщиной стенки.
- Очень просто (и даже в электронном виде) измерить текущее усилие прижима , создаваемое центратором . Достаточно врезать в гидравлическую систему датчик давления. Это позволяет применять на гидравлических аппаратах средства автоматизации сварочного процесса.
- Возможность разделить привод (гидравлический агрегат) и центратор , соединив их шлангами. Маленькие образцы гидравлических аппаратов (напр., PT-125) удобны для сварки навесу.
- Гидравлический агрегат – весьма заметная добавка к цене сварочного аппарата.
С учетом этих особенностей гидравлические аппараты заняли нишу «профессионального» сварочного оборудования для сварки стыковых соединений – без ограничений по толщине стенки свариваемых труб, без ограничений по диаметрам сварки, с возможностью автоматизации для сварки особо ответственных трубопроводов. Цена отходит на второй план, на то оно и «профессиональное» оборудование.
5.8 Конструктивные исполнения (степень автоматизации)
ГОСТ Р ИСО 12176-1 в значительной степени является переводом международного ISO 12176-1 и дает классификацию сварочного оборудования по степени автоматизации, несколько отличную от привычной нам классификации, впервые введенной в 2003г. в СНиП 42-01-2002 (п.10.4.5 СНиП) и по-прежнему используемой по отношению к оборудованию для сварки газопроводов. Классификация ГОСТ:
Читайте также: