Ультразвуковая сварка в микроэлектронике
Обновлено: 20.09.2024
При ультразвуковой сварке (УЗС) необходимые условия для образования соединения создаются в результате механических колебаний ультразвукового преобразователя. Энергия вибрации создает сложные напряжения растяжения, сжатия и среза. При превышении предела упругости соединяемых материалов происходит пластическая деформация в зоне их соприкосновения. В результате пластической деформации и диспергирующего действия ультразвука происходит удаление адсорбированных пленок жидкости, газов, органических пленок и поверхностных оксидов, происходит увеличение площади непосредственного контакта, что обеспечивает получение прочного соединения.
Ультразвук находит широкое применение в науке для исследования некоторых физических явлений и свойств веществ. В промышленности ультразвуковые колебания используются для очистки и обезжиривания изделий, для обработки труднообрабатываемых материалов. Установлено благоприятное влияние ультразвуковых колебаний на кристаллизующиеся расплавы — происходит дегазация и измельчение зерна и улучшение механических характеристик литых металлов. Получены положительные эффекты при воздействии ультразвуковых колебаний с целью снятия остаточных напряжений. Широкое использование ультразвук находит с целью интенсификации многих медленнотекущих химических реакций. Известна аппаратура для контроля уровня жидкости, скоростей ее течения и т. п. Успешно используется ультразвук для контроля качества литья, сварных соединений и т. п.
В сварочной технике ультразвук может быть использован в различных целях. Воздействуя им на сварочную ванну в процессе кристаллизации, можно улучшить механические свойства сварного соединения благодаря измельчению структуры металла шва и лучшему удалению газов. Ультразвук может быть источником энергии для создания точечных и шовных соединений. Ультразвуковые колебания активно разрушают естественные и искусственные пленки, что позволяет сваривать металлы с окисленной поверхностью, покрытые слоем лака и т. п. Ультразвук уменьшает или снимает собственные напряжения, возникающие при сварке. Им можно стабилизировать структурные составляющие металла сварного соединения, устраняя возможность самопроизвольного деформирования сварных конструкций со временем.
Сварка металлов ультразвуком находит все более широкое применение, так как этот способ имеет ряд преимуществ и особенностей по сравнению с контактной и холодной сваркой. Особенно перспективна ультразвуковая сварка применительно к изделиям микроэлектроники. Весьма перспективна сварка ультразвуком пластмасс; этот метод широко используется в промышленности, так как обладает рядом особенностей, дающих возможность получить высококачественное соединение на многих пластмассах, сварка которых другими методами затруднена или невозможна.
Разработаны оборудование и технология ультразвуковой сварки металлов и пластмасс, успешно использующиеся в промышленности. За рубежом этот метод также находит применение в промышленности.
При сварке ультразвуком неразъемное соединение металлов образуется при совместном воздействии на детали механических колебаний высокой частоты и относительно небольших сдавливающих усилий. В принципе этот метод сварки имеет много общего с холодной сваркой сдвигом.
Колебания, возникающие в какой-либо среде и характеризующиеся упругими деформациями среды, называются упругими. Форма упругих колебаний может быть различна. Наиболее распространенной формой являются гармонические колебания, т. е. колебания, описываемые выражением
где A — смещение или деформация в данном элементе среды в момент времени t; Aм — максимальное значение смещения или деформации; ω — круговая частота колебаний; φ — начальный угол сдвига.
Упругие колебания, частота которых превышает некоторую границу, принято называть ультразвуковыми. Обычно считают, что нормальный человеческий слух не воспринимает в виде слышимого звука гармонические упругие колебания с частотой выше 17 000—20 000 Гц. В практике упругие колебания используются в диапазоне частот от 8000 Гц до мегагерц. При ультразвуковой сварке обычно используется диапазон частот 18—80 кГц.
Скорость распространения ультразвука зависит от физических свойств материала. Например, в стержне скорость распространения продольных волн определяется из следующего соотношения:
где Е — модуль упругости материала; ρ — плотность материала.
Скорость распространения звуковых волн в большинстве твердых тел колеблется в пределах 2000—6000 м/с и изменяется в зависимости от температуры, давления и интенсивности звука.
Длина волны, соответствующая данной частоте, непосредственно определяется из равенства
где c — скорость звука; f — частота.
При частоте 20 кГц длина волны в стали равна 28 см.
Интенсивность плоской продольной звуковой волны в любой среде определяется из уравнения
где А — амплитуда колебаний; f — частота колебаний; ρ — плотность среды; k — коэффициент пропорциональности; с — скорость звука в среде.
Поток энергии волны сквозь некоторую поверхность S равен
где β — угол между нормалью к площадке dS и направлением распространения волны.
Мощность ультразвука, которая может быть передана через среду, зависит от физических свойств среды; если напряжения в зонах сжатия и разрушения превысят предел прочности материала, то твердый материал будет разрушаться. В жидкостях в аналогичных случаях возникает кавитация с образованием мельчайших пузырьков паров жидкости и последующим их захлопыванием. Процесс захлопывания кавитационных пузырьков сопровождается возникновением местных давлений, превышающих 5000 кгс/см 2 . Это явление в жидкостях используется для обработки и очистки изделий.
Машины для ультразвуковой сварки состоят из следующих основных узлов: источника питания, аппаратуры управления, механической колебательной системы и привода давления.
Механическая колебательная система служит для преобразования электрической энергии в механическую, передачи этой энергии в зону сварки, концентрирования этой энергии и получения необходимой величины колебательной скорости излучателя.
Колебательная система (рис. 23) состоит из электромеханического преобразователя 1 с обмотками, заключенного в металлический корпус 2, охлаждаемый водой; трансформатора упругих колебаний 5; сварочного наконечника 4; опоры с механизмом давления 5 и свариваемых деталей 6. Крепление колебательной системы производят с помощью диафрагмы 7. Ультразвук излучается только в момент сварки точки.
На рис. 24 показана схема шовной сварки ультразвуком, которая может быть использована для получения герметичных швов на изделии, В этой схеме сварки колебательная система приводится во вращение специальным приводом. При сварке изделие зажимается между концом вращающегося трансформатора упругих колебаний, выполненного в виде ролика, и нижним прижимным роликом. Ультразвук излучается непрерывно в процессе сварки. Элементом колебательной системы, возбуждающей упругие колебания, является электромеханический преобразователь, использующий магнитострикционный эффект. Переменное напряжение создает в обмотке преобразователя намагничивающий ток, который возбуждает переменное магнитное поле в материале преобразователя. При изменении величины напряженности магнитного поля в материале возникает периодическое изменение размеров, при этом частота упругих колебаний равна двойной частоте тока.
Изменения размеров магнитострикционных материалов незначительны. Так, для сплава К49Ф2 магнитострикционное удлинение составляет 70*10 -6 . Поэтому для увеличения амплитуды смещения и концентрации энергии колебаний, а также для передачи механических колебаний к месту сварки используют волноводы и трансформаторы упругих колебаний. Основным назначением трансформаторов упругих колебаний является увеличение амплитуды колебаний до величины, необходимой для осуществления процесса сварки. Для этой цели концентратор выполняется в виде стержня специальной формы, площадь поперечного сечения которого изменяется вдоль направления распространения колебаний по определенному закону.
Эксперименты показывают, что для целей сварки металлов достаточно иметь трансформаторы с коэффициентом усиления ~ 5, так чтобы амплитуда на конце его при холостом ходе была равна 20—30 мкм.
Магнитострикционный преобразователь и трансформаторы должны быть рассчитаны и изготовлены на заданную частоту ультразвукового генератора. На рис. 25 показана схема изменения амплитуды колебаний в трансформаторе упругих колебаний.
Питание электромеханических преобразователей осуществляется от источника электрической энергии — генератора с частотой колебаний тока 18—180 кГц.
Рабочая частота генератора определяется собственной частотой механической колебательной системы, выходная мощность генераторов 0,01—10,0 кВт.
Процесс ультразвуковой сварки происходит при воздействии сдвигающих высокочастотных колебаний, давления, приложенного перпендикулярно к поверхности листа, и теплового эффекта, сопровождающего процесс сварки. В результате в зоне сварной точки наблюдается небольшая пластическая деформация.
Исследование процесса образования сварного соединения при ультразвуковой сварке медных пластин толщиной 0,35 + 0,35 мм показывает, что при малом времени пропускания ультразвука (менее 0,05 с) сварка не происходит. После разъединения образцов на их поверхности непосредственно под сваривающим выступом наблюдается пятно, имеющее полированную поверхность (рис. 26, а).
Диаметр полированного пятна возрастает при увеличении времени сварки (рис. 26, а — д). При пропускании ультразвука в течение 0,1 с в местах контакта обнаруживаются не только зашлифованные поверхности, но и вырывы металла, свидетельствующие об образовании прочных соединений, так называемых узлов схватывания. На рис. 26, б виден один узел схватывания на зашлифованной поверхности.
Пропускание ультразвука в течение 0,73 с привело к дальнейшему увеличению площади зашлифованного пятна, при этом площадь узла схватывания также возросла. Вокруг основного узла схватывания возникли отдельные небольшие участки схватывания, удлиненные в направлении ультразвуковых колебаний. С увеличением времени пропускания ультразвука > 0,73 с площадь зашлифованного участка почти не изменяется (рис. 26, г, д), но площадь узлов схватывания начинает увеличиваться более интенсивно. При пропускании ультразвука свыше 1,06 с происходит разрушение сварного соединения с вырывом точки по всему контуру.
Проведенные измерения микротвердости поверхности зашлифованного пятна и основного металла вблизи пятна показали, что микротвердость поверхностного слоя зашлифованного пятна выше (42—44 Hм), чем у основного металла (28—30 Hм). Образование полированного пятна на свариваемых поверхностях указывает на то, что оно возникло вследствие трения под действием высокочастотных колебаний соприкасающихся поверхностей непосредственно под контактным выступом.
Таким образом, процесс ультразвуковой сварки происходит под действием трения, вызванного микроскопическим возвратно-поступательным перемещением частиц на трущихся поверхностях.
В начальный момент действия ультразвуковых колебаний на свариваемых поверхностях возникает сухое трение. На этой стадии на свариваемых поверхностях происходит разрушение окисных пленок и пленок из адсорбированных газов и жидкостей. После возникновения ювенильных поверхностей наступает вторая стадия образования сварного соединения. Процесс сухого трения переходит в чистое трение, которое сопровождается образованием узлов схватывания. Схватыванию в значительной степени способствует малая амплитуда колебаний трущихся поверхностей и возвратно-поступательный характер этих колебаний.
Металлографические исследования сварных образцов различных металлов, сваренных при повышенных давлениях, мощности и времени, не обнаружили в зоне сварки литой структуры или воздействия на металл очень высоких температур.
Микроисследования мест сварки показывают, что имеются общие зерна, принадлежащие обеим свариваемым поверхностям и пересекающие границу раздела; кроме этого, образуются общие границы между поверхностными зернами. Очевидно, в этих обоих случаях сварное соединение будет обладать прочностью, равной прочности основного металла.
Большие значения предела прочности ультразвуковых сварных соединений подтверждают то, что они образуются вследствие возникновения металлических связей в узлах схватывания, имеющих такую же прочность и природу, как и основной металл.
Тепловые процессы при сварке
Процесс ультразвуковой сварки сопровождается выделением тепла в зоне сварки. Образование тепла вызывается возникновением трения на контактных поверхностях и пластическими деформациями в металле, сопровождающими образование сварного соединения.
Температура в зоне сварки зависит от прочностных характеристик — главным образом от твердости металла и его теплофизических свойств: теплопроводности и теплоемкости, режима сварки.
Работы показали, что наблюдающееся повышение температуры не является определяющим фактором, так как максимальная прочность сварных соединений достигается ранее, чем достигается максимальная температура в контакте.
Предварительный подогрев изделия приводит к уменьшению длительности пропускания ультразвуковых колебаний и способствует увеличению прочности сварного соединения.
Прочность точечных и шовных сварных соединений
На рис. 30 показана зависимость прочности точечных соединений алюминиевых листов от продолжительности пропускания ультразвуковых колебаний и давления на точку Как видно, при малых давлениях прочность точки в значительной степени зависит от времени прохождения ультразвука. С повышением давления сварные соединения прочнее при меньшем времени прохождения ультразвука. При очень продолжительном пропускании ультразвука и большом давлении сварное соединение некачественно вследствие значительных деформаций основного металла и приваривания его к электроду.
При шовной сварке прочность сварных соединений обычно выше прочности основного металла, и разрушение происходит по основному металлу.
Сварка ультразвуком позволяет соединять различные металлы; хорошо свариваются ультразвуком алюминий, медь, никель, удовлетворительно свариваются нержавеющие стали. При этом прочность сварных точечных соединений достаточно высока, разрушение соединений происходит обычно с вырывом точки по контуру как при испытаниях на срез, так и при испытаниях на отрыв.
С помощью ультразвука получены соединения на ряде тугоплавких металлов — ниобии, тантале, молибдене и вольфраме. Однако недостатком сварных соединений вольфрама и молибдена является их хрупкость.
Важным обстоятельством ультразвуковой сварки является возможность соединения различных металлов, которые обычными методами не соединяются.
Ультразвуковые сварочные машины
Ультразвуковая сварка в последнее время нашла наибольшее применение в микроэлектронике, в основном для приварки токоотводов к интегральным схемам.
Разработаны и выпускаются сериями ультразвуковые машины для сварки различных элементов микросхем оснащенные автоматическими устройствами (автоматически осуществляется подача проводников, сварка, обрезка проводников и т. п.), позволяющими в значительной степени увеличивать производительность.
Преимущества сварки ультразвуком:
- сварка осуществляется в твердом состоянии металла без существенного нагрева места сварки, что дает возможность соединять химически активные металлы или пары металлов, склонные образовывать хрупкие интерметаллические соединения в зоне сварки;
- возможность соединения тонких и ультратонких деталей, возможность приварки тонких листов и фольги к деталям неограниченной толщины, сварка пакетов из фольги;
- снижение требований к чистоте свариваемых поверхностей дает возможность проводить сварку плакированных и оксидированных поверхностей и вообще сварку металлических изделий, поверхности которых покрыты различными изоляционными пленками;
- применение небольших сдавливающих усилий (10—250 кгс), вследствие чего деформация поверхности деталей в месте их соединения незначительна (вмятина, как правило, не превышает 5—10%);
- малая мощность оборудования и несложность его конструкции (если, например, для контактной точечной сварки алюминия толщиной 1 мм необходима машина мощностью 100—150 кВ*А, то при сварке ультразвуком аналогичного соединения потребляется всего 5—2,5 кВ*А).
Область применения
Ультразвуковая сварка нашла достаточно широкое применение для соединения тонких деталей из однородных и разнородных материалов в приборостроении и радиоэлектронной промышленности. В дальнейшем можно ожидать, что этот метод будет использован при сварке металлов, образующих хрупкие интерметаллические соединения, для приварки тонких обшивок к несущей конструкции (в авиационной промышленности, автомобилестроении и ряде других отраслей промышленности).
По мере совершенствования технологического процесса и оборудования область применения ультразвуковой сварки будет непрерывно расширяться.
Ультразвуковую сварку применяют для соединения многих металлов. Наиболее легко свариваются пластичные металлы (алюминий, медь и их сплавы, серебро, никель и т.п.) как между собою, так и с твердыми малопластичными материалами.
Металлические детали могут свариваться с керамикой, стеклом, полупроводниковыми материалами (кремний, германий). Успешно свариваются тугоплавкие металлы: вольфрам, ниобий, тантал, цирконий, молибден. Можно сваривать заготовки через прослойку из третьего металла, например сталь со сталью через алюминий, а также заготовки покрытые оксидами, лаками, полимерами и т.п. Используется УЗС также для соединения пластических масс.
Качество соединений при шовной сварке определяется теми же параметрами, что и при точечной, лишь вместо времени сварки вводится скорость движения детали. При правильно выбранных режимах шовной сварки разрушающее усилие сварного соединения выше чем основного металла.
Ультразвуковая микросварка | Сварить или склепать? ➔ часть II
В первой части статьи мы рассказали о стадиях процесса формирования сварного соединения, разобрались в различиях амплитуды колебаний в системе «инструмент-проволока-подложка» (рис. 1), а также поговорили о том, каким образом при минимальной деформации обеспечить максимальную надёжность контакта. Теперь речь пойдёт о влиянии резонансной частоты ультразвука на качество соединения.
Поскольку в подавляющем большинстве случаев для микросварки применяют частоты порядка 60 или 100/140 кГц, интересно знать, чем был обусловлен такой выбор и что происходит за пределами этого диапазона.
Краткое описание задачи:
Как не ошибиться при выборе оптимальной частоты ультразвуковой сварки?
В научной литературе и материалах конференций SEMI, IMAPS, IEEE и других отраслевых сообществ часто мелькали статьи на тему сварки с применением частот ультразвуковых колебаний 200 и даже 300 кГц. Тема вызывала тогда большой интерес из-за предположения о том, что энергия УЗ-колебаний способна заменить собой нагрев рабочего стола при сварке методом шарик-клин, чтобы процесс можно было проводить при комнатной температуре. Несмотря на то, что ряд опытов оказался успешным, в дальнейшем от идеи ВЧ-сварки пришлось отказаться главным образом по причинам низкой надёжности соединения и узкого технологического окна процесса. Снижение процента выхода годных соединений просто-напросто не компенсировалось сокращением себестоимости. Сегодня в академической среде к УЗ-сварке на высоких частотах практически не возвращаются. Но некоторые разработчики и технологи все же пробуют перейти с 60 на 100 или 140 кГц, когда экспериментируют с новыми материалами и режимами.
Поскольку все специалисты получают неоднозначные результаты, есть смысл понять, зачем вообще менять частоту УЗ-колебаний системы? Какие параметры «утянет» за собой изменение частоты? Своим опытом готовы поделиться эксперты производителя первой в мире автоматической установки ультразвукового присоединения проволочных выводов F&K DELVOTEC M17.
В общем случае с точки зрения воздействия на кристалл/подложку наиболее важным элементом процесса является длительность образования соединения при той или иной резонансной частоте УЗ-преобразователя. Для создания качественного сварного соединения требуется 1000–3000 циклов колебаний инструмента в системе «инструмент-проволока-подложка» (при условном времени сварки около 20 мс и частоте 100 кГц). Именно столько циклов взаимного перемещения всех составляющих системы относительно друг друга требуется для образования наклёпа и общих «зёрен» будущего сварного соединения (подробнее об этом рассказывалось в первой части публикации).
Теоретически при повышении частоты колебаний должно пропорционально сокращаться время, необходимое для формирования сварного соединения. Впрочем, общая производительность оборудования значительно не повысится, так как время приложения УЗ-воздействия занимает менее половины времени цикла — остальное тратится на позиционирование, распознавание и движение рабочей головки.
Гораздо важнее другое. При более высоких частотах качественные соединения образуются при меньших амплитудах колебаний. Это вовсе не значит, что амплитуды колебания на таких частотах по умолчанию ниже (амплитуду преобразователя можно подогнать в нужных пределах в ходе изготовления).
Таблица 1 — Соответствие материалов и частоты УЗ-колебаний
Вернёмся к первой стадии образования сварного соединения в рассмотренной нами ранее модели (рис. 1). После взаимного трения проволоки вдоль поверхности контактной площадки, приводящего к очистке трущихся поверхностей от загрязнений и оксидов, начинается взаимодействие металлов на межатомном уровне. Металлы проволоки и подложки перемешиваются и образуют общие островки интерметаллических «зёрен» вдоль границы раздела. На второй стадии, по мере образования и роста «зёрен», разница в амплитудах колебаний верхней и нижней поверхностей проволоки становится все больше по сравнению с начальной фазой процесса. Начинается уменьшение амплитуды колебаний всей системы «инструмент проволока-подложка», включая колебания конца инструмента, в силу демпфирующего воздействия на него формирующегося «вязкого» соединения металлов. Таким образом, увеличение амплитуды колебаний инструмента оказывается более эффективным при работе с толстыми покрытиями. Грубые поверхности типа гибридных толстоплёночных паст выигрывают от эффекта шлифовки или планаризации под действием бóльших амплитуд на низких частотах (60 кГц и ниже). В то же время большая амплитуда подвергает риску тонкие слои напыления и гладкие поверхности контактных площадок хрупких кристаллов, например в ПАВ‑фильтрах, где толщина металлизации может составлять 40 нм. Столь тонкие слои не требуют грубой притирки и превосходно свариваются на более высоких частотах (140 кГц). По мнению инженеров компании F&K Delvotec, рабочая частота системы в 100 кГц является золотой серединой и может стать оптимальным решением для большинства задач. Это подтверждается и статистикой: чаще всего заказчики выбирают именно данную частоту в качестве основной.
Но как быть, если номенклатура изделий содержит взаимоисключающие группы? Менять установку? Покупать второй генератор? Что касается амплитуды, заказчики в любой момент могут изменить своё предпочтение и заказать преобразователь с другой характеристикой амплитуды колебаний. Это недорогое удовольствие, учитывая стоимость изделий, для производства которых требуется подобный «тюнинг». А цифровой УЗ-генератор UUG‑030 от F&K Phisyktechnik 1 устанавливается по умолчанию на всех моделях брендов и автоматически настраивается на резонанс преобразователя головки в диапазоне 40–200 кГц. При этом у клиентов остаётся свобода маневра при выборе иной резонансной частоты и мощности для экзотических применений и материалов. Например, работа сверхдлинным инструментом в колодцах глубиной 50–70 мм или TAB-сварка изолированной лентой иногда требуют индивидуального подхода.
С генератором UUG‑030 установки серий 53ХХ, 56ХХ, 58ХХ, М17 (рис. 2), оснащённые соответствующими сменными рабочими головками, способны работать с тонкими и толстыми проволоками в диапазоне 17–600 мкм, в том числе композитными и изолированными, с лентой сечением до 2000×300 мкм.
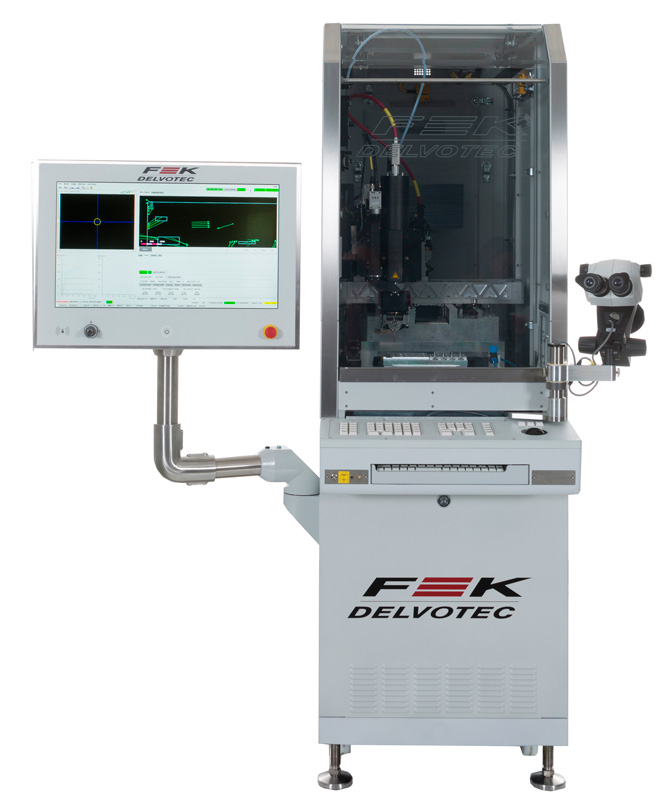
Установка становится настоящей микрофабрикой, способной действовать со всеми современными материалами, с подложками любого типа, алюминиевыми, золотыми, композитными и медными проволоками. А серия 56ХХ к тому же сможет проводить автоматическое тестирование прочности соединений, просто импортируя программу сварки.
Очевидно, что чем выше частота, тем выше линейная скорость движения кончика инструмента. Точнее, скорость всей системы «инструмент-проволока-подложка». Большинство материалов, входящих в состав колебательной системы, с возрастанием частоты УЗ-воздействия больше сопротивляются влиянию друг на друга, поскольку начинает сильнее проявляться противодействующая сила упругого столкновения. На практике это означает, что ультразвуковые колебания работают «по поверхности» и меньше проникают во внутреннюю структуру материалов проволоки и контактной площадки. И наносят им меньший вред. Именно поэтому мягкие материалы типа полиимидных подложек лучше варятся именно на более высоких частотах. Это справедливо и для некоторых чувствительных кристаллов или ПАВ‑фильтров. При стандартном наборе параметров (частота, амплитуда) выполнить качественную сварку на нежной поверхности сложно, но при правильном подборе характеристик, в том числе и на более высокой частоте, трудностей не возникнет.
И наоборот, на низких частотах проволока за счёт более «мягкого» движения подстраивается под грубую и шероховатую поверхность контактных площадок (FR4, толстоплёночных ГИС, LTCC, HTCC), обеспечивая лучшее качество сварки. В таблице представлены общие соответствия материалов и частоты УЗ-колебаний.
При более высокой частоте тракта можно получить прочное соединение на относительно малой деформации проволоки. То есть увеличение частоты становится ещё одним способом улучшить качество и расширить технологическое окно параметров при работе с тонкой (17–20 мкм) проволокой.
Но и для стандартной (25–35 мкм) проволоки меньшая деформация всегда предпочтительнее «передавливания»: понижаются напряжения в пятке сварки, определяющие надёжность, долговечность и устойчивость соединения к термоциклам. Это подтверждается и экспериментально — усилия на обрыв сварных петель крючком уменьшаются с увеличением деформации после достижения ею некоего оптимального значения.
Рис. 3 — Соответствие частоты УЗ-колебаний и метода сварки
ЗАКЛЮЧЕНИЕ
Со времени возникновения УЗ-сварки в 1947 году единых предписаний в отрасли так и не было выработано: любой из методов сварки по-прежнему можно применять в сочетании с двумя-тремя частотами УЗ-генератора. Помимо рассмотренных факторов, решение в пользу той или иной частоты принимается в зависимости от длины и типа рабочего инструмента, длины и высоты петель и типа проволоки. На рис. 3 показана вероятность использования той или иной частоты в привязке к методу сварки (отмечено кружком). Данные получены в ходе закрытого опроса заказчиков оборудования F&K Delvotec, а это в основном изготовители изделий высокой надёжности и автоэлектроники.
В статье мы рассмотрели лишь первый общий принцип выбора частоты в зависимости от материала и типа поверхности контактной площадки. Образно говоря, частота должна быть высока настолько, насколько это возможно (для минимизации рисков повреждения кристалла, «передавливания» пятки петли и уменьшения общего времени воздействия), но в то же время низка настолько, насколько это необходимо для компенсации шероховатости поверхности и проникновения УЗ-частоты вглубь материала. В последующих статьях цикла мы постараемся дать рекомендации и в отношении других параметров.
Ультразвуковая микросварка | Сварить или склепать? ➔ часть I
Каждый год в мире производится более четырёх триллионов проволочных соединений, выполненных ультразвуковым методом в полупроводниковых приборах. Несмотря на свою долгую 60‑летнюю историю, этот нелепый «бондинг» по-прежнему используется в пятидесяти миллиардах ежегодно выпускаемых интегральных схем и бесчисленных дискретных приборах. Каждые десять лет появляется очередная технология — «убийца УЗ-сварки».
После оваций, статей и вручения премий за инновации (и банальной раскрутки промышленных гигантов на финансирование НИОКР) подобное новое изобретение благополучно дополняет имеющийся арсенал, а сотни тысяч установок продолжают мирно вышивать узоры из драгоценных нитей. Понимание основ процесса по-прежнему актуально для специалистов отрасли и останется таковым еще долгие годы, наряду с С4, FC, TAB, TSV и другими методами интеграции полупроводниковых компонентов в современном корпусировании.
В отличие от механических процессов («отсюда взять–туда положить») и чистой физики («нагреть–припаять») присоединение выводов ультразвуком всегда считалось непонятной и сложной операцией, в ней всегда было немного магии. Почему необходимо понимать, как протекает процесс соединения проволоки и контактной площадки? Каким образом при минимальной деформации обеспечить максимальную надёжность контакта? Есть ли чёткие критерии выбора частоты для работы с тем или иным материалом? Многие предприятия пробуют перевести свой процесс сварки с традиционных 60 на 100 или 140 кГц, экспериментируют с новыми материалами и режимами, но часто сталкиваются с неоднозначными результатами. Поэтому понимание физических основ процесса по-прежнему важно. В преддверии выхода на российский рынок нового (шестого) поколения автоматов ультразвуковой сварки своим опытом готовы поделиться эксперты F&K Delvotec Bondtechnik — производителя первой в мире автоматической установки проволочных выводов.
Илья Корочкин — Глобал Микроэлектроника, Россия
Сергей Валев — CEO i.V.tec electronics, Россия
Краткое описание процесса:
Как можно перемешать металлы без плавления и где взять лишнее время, если не успел этого сделать.
Вероятно, нелишне напомнить, какие стадии процесса существуют при формировании сварного соединения, и представить его современную физическую модель. На рис. 1–3 схематично показаны три стадии формирования соединения методом «клин-клин». При этом рассмотренные далее базовые принципы справедливы и для более громоздкого в описании метода «шарик-клин».
В момент соприкосновения проволоки с поверхностью контактной площадки (подложки) начинается передача колебаний пьезопреобразователя в точку контакта инструмент-проволока-подложка с амплитудой порядка нескольких микрометров (1–2 мкм для тонкой и 3–5 мкм для толстой проволоки).
Важно отметить, что пара проволока-инструмент на этой стадии колеблется синхронно, как единая система. Таким образом, физическое перемещение (притирка) происходит только по границе проволока — контактная площадка.
Для стабильной передачи колебаний в этой системе крайне необходимо отсутствие случайных проскальзываний проволоки в инструменте, то есть трение в паре инструмент-проволока должно быть намного выше, чем в паре проволока-подложка. Для этого нижняя поверхность инструмента должна слегка деформировать проволоку, «впечатываясь» в неё. В регулируемых настройках оборудования любого производителя найдётся «сила прижима» (Bond Force). Как будет показано ниже, это самый важный параметр при формировании соединения, который подбирают для конкретного типа проволоки, ее диаметра и характера подложки.
Следует подчеркнуть, что эта первая фаза процесса уже создаёт предпосылки для получения того или иного результата:
- Насколько точно оборудованием определён момент контакта с подложкой? Поскольку от момента касания начинается отсчёт заданной длительности УЗ-колебаний, в случае определения «ложного касания» колебания в системе могут прекратиться раньше, чем будет получено качественное соединение.
- Правильно ли выбран инструмент? Все металлы, используемые для получения соединений, имеют свои особенности, и это отражается на материале, из которого сделан инструмент, и форме контактирующей с проволокой поверхности. Например, для сварки золотой проволокой она часто выполняется с рельефом в форме поперечной борозды или перекрестия. Для проволоки разных диаметров и жёсткости подбирают индивидуальные радиусы входа и выхода проволоки, шероховатость поверхности инструмента и т. д. Любой инструмент для ультразвукового присоединения проволочных выводов имеет свыше 40 индивидуальных контролируемых параметров, измеряемых в сотых и тысячных долях миллиметра, что в конечном итоге объясняет его высокую цену. И конечно, усугубляет боль оши- бок при его выборе.
Итак, в течение первых миллисекунд происходит трение проволоки вдоль поверхности контактной площадки, приводящее к очистке трущихся поверхностей от загрязнений и оксидов. В случае сварки алюминиевой проволокой процессу очистки помогает тот факт, что чистый алюминий всегда покрыт твёрдой, но хрупкой оксидной плёнкой При УЗ-воздействии, сочетающем давление и колебания, этот тонкий слой мгновенно разрушается, и его твёрдые частицы быстро обнажают кристаллическую решётку чистого металла, однако не повреждают ее в силу малого размера абразивных частиц оксида алюминия. Эффект «нанотерки» объясняет, почему для качественной сварки алюминиевой проволокой достаточно комнатной температуры. В ходе сварки золотой проволокой, где такого абразива не возникает, для быстрой активации поверхностей требуется нагрев, как правило, до +110. 130°C.
После того как кристаллические решётки касающихся друг друга металлов пришли в тесное соприкосновение, начинается взаимодействие металлов на межатомном уровне (рис. 2). Металлы проволоки и подложки перемешиваются и образуют общие островки интерметаллических зёрен вдоль границы раздела.
Появление зёрен меняет характер движения проволоки, поскольку она теперь не представляет собой единую жёсткую структуру, в которой верхняя и нижняя поверхности движутся в унисон механическим колебаниям инструмента.
Нижняя поверхность проволоки все больше связывается и замедляется, в то время как верхняя продолжает колебаться: происходит деформация проволоки (сопутствующие процессы перекристаллизации и появление дислокаций атомной решётки в данной статье не рассматриваются).
Нужно заметить, что в отличие от пластической, эластическая составляющая деформации в проволоке крайне мала в такой момент, поскольку разница в амплитудах перемещения верхней и нижней поверхностей проволоки составляет порядка 1 мкм при толщине 20–30 мкм, а это на порядок превышает предел эластической деформации металла.
Стрелками на рис. 1–3 схематично показана результирующая амплитуда колебаний в системе. По мере образования и роста зёрен разница в амплитудах колебаний верхней и нижней поверхностей проволоки по сравнению с начальной фазой процесса становится все больше. Начинается уменьшение амплитуды колебаний всей системы, включая и колебания конца инструмента, в силу демпфирующего воздействия на него формирующегося сварного соединения.
Поскольку УЗ-воздействие на точку контакта продолжается, зерна разрастаются и в идеальном случае постепенно занимают всю площадь контакта. В какой-то момент движение нижней поверхности проволоки по подложке прекращается.
Фактически теперь начинает колебаться не проволока, а пара нижняя поверхность проволоки — подложка, хотя и с гораздо меньшей амплитудой, чем исходная пара проволока-подложка.
(обозначено парой маленьких стрелок на рис. 3).
В процессе увеличения площади зёрен сварного соединения инструмент, давящий на проволоку, деформирует её, при этом толщина области под инструментом уменьшается, а ширина получающегося соединения увеличивается. Деформация соединения может отслеживаться как функция смещения по оси Z в реальном времени, что даёт надёжный инструмент для контроля качества соединения с введением таких понятий, как «величина деформации по истечении заданного времени сварки» и «скорость нарастания деформации». Наличие подобных систем характерно для оборудования высокого уровня, предназначенного для производства изделий специального назначения. В своём базовом варианте система контроля деформации (DLC) доступна уже на полуавтоматических настольных установках F&S Bondtec серии 56ХХ и 58ХХ (рис. 4).
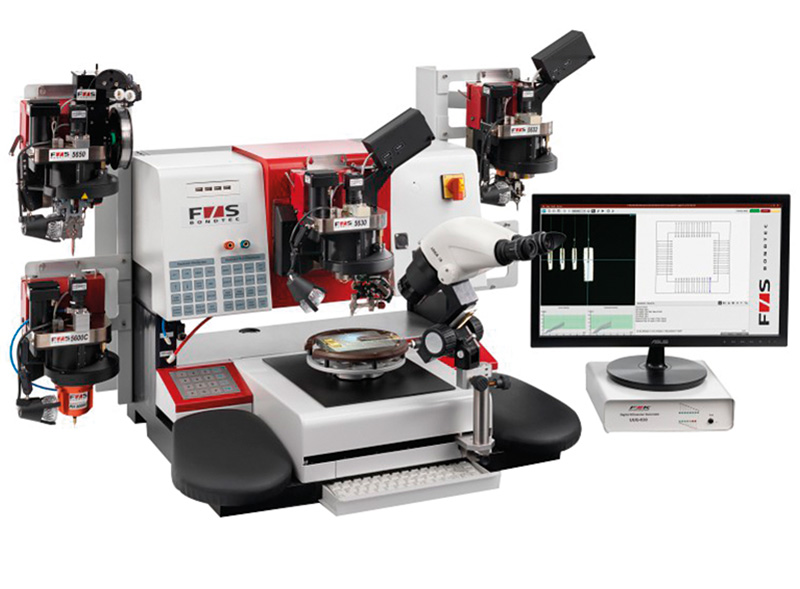
В процессе работы система ведёт постоянный мониторинг деформации и сравнивает результаты с полем допустимых значений. В случае отклонения параметров процесса от допустимых установка может либо отметить это отклонение в журнале работы, либо остановить свою работу до вмешательства оператора.
Интеллектуальная система BPC, предлагаемая на установках серии M17, идёт несколько дальше констатации фактов и сбора статистики. Поскольку при крупносерийном производстве нереально звать на помощь оператора в каждом случае отклонения от эталона, система BPC не только наблюдает, но и активно управляет процессом.
данные о деформации, получаемые в реальном времени, составляют управляющую часть системы с обратной связью и служат для повышения или снижения мощности и длительности УЗ-сварки при отклонении реального характера деформации от заданного пользователем. Таким образом, система BPC помогает в тонкой настройке процесса сварки каждого соединения «на лету» и предотвращает недостаток или избыток энергии, переданной в ходе процесса в точку сварки. Если вспомнить о важности определения момента касания, то в некоторой степени BPC компенсирует неизбежные на этом микроуровне погрешности, в режиме реального времени «загоняя» процесс каждой сварки в отведённые ему рамки. Без этой системы, особенно при работе с гибридными схемами и модулями, погрешности в определении точки касания приводят к большему разбросу параметров прочности (то есть снижению ресурса изделия до момента отказа слабейшего из них), а в худшем случае к слабым или, наоборот, «пережаренным» соединениям и отказам уже в ходе приёмочных испытаний.
В особенности важна функция управления длительностью процесса. Дело в том, что этот параметр по умолчанию устанавливают «с запасом», чтобы дать возможность соединению полностью сформироваться. Избыточное УЗ-воздействие обычно связано с металлургическим отпуском и рекристаллизацией соединения, при которых не происходит дальнейшей деформации проволоки. Вернёмся к схеме третьей фазы соединения (рис. 3), где колебания охватывают всю систему, с большей амплитудой у инструмента и меньшей у подложки. Фактически вместо одной системы появляются две пары, колеблющиеся с разной амплитудой. Градиент амплитуды колебаний в проволоке (вверху больше, внизу меньше) вызывает в материале проволоки холодную пластическую деформацию, называемую нагартовкой (наклёпом). Нагартовка помогает «полезным» дислокациям кристаллической решётки, которые возникли как зерна вдоль поверхности раздела металлов, распространиться глубже в структуры составных металлических слоёв, сильнее привязывая проволоку к подложке. В теории это должно увеличить ресурс соединения. Примером использования такого процесса в «большой» металлургии является холодная прокатка, галтовка и т. п. Важно, что нагартовка происходит при температурах ниже температуры рекристаллизации (начиная от комнатной и до 1/2 температуры плавления) и выражается в образовании округлых зёрен металла на месте вытянутых и деформированных.
Грань, за которой избыточная нагартовка приводит к образованию микротрещин, разрывов кристаллической решётки и повышенной хрупкости соединения, очень тонка. Округлая форма новообразованных металлических зёрен в соединении немного увеличивает содержание пор и снижает общую плотность, и избыточная длительность может привести к отказам уже после начала эксплуатации прибора. Оценить степень структурных изменений в каждом индивидуальном соединении, конечно, невозможно и оперировать приходится только косвенными методами оценки и воздействия на этот микропроцесс.
Алгоритм работы системы BPC в F&K Delvotec M17 предусматривает возможность управления длительностью сварки и мощностью УЗ-воздействия, что определяет интегральную энергию всех импульсов колебаний, приложенную к каждой конкретной точке.
Графически данная энергия может быть представлена как площадь фигуры под кривой деформации (рис. 6).
То, что мы имеем возможность с помощью системы BPC и (главное!) без участия оператора поднимать-опускать (мощность) и удлинять-укорачивать фигуру, изменяя её площадь, объясняет эффект значительного улучшения «критических для качества» характеристик процесса (таких как Cpk), что и предопределило широкую популярность оборудования F&K Delvotec у производителей автомобильной электроники, специальной техники и авионики.
Заметим, что до сих пор, говоря о процессе, который в русском языке называется «сварка», ни разу не было упомянуто ни плавление, ни даже повышение температуры в зоне соприкосновения металлов как результат трения проволоки о подложку. Действительно, несмотря на огромные усилия, затраченные исследователями, нагрев и его влияние на результат сварки до сих пор не удаётся измерить и оценить достоверно. Попытки увидеть микроскопические зоны расплавленного металла в микрошлифах соединений также пока не привели к успеху. Довод о том, что «видимо, эти зоны есть, просто они очень малы», опровергается любопытным опытом по успешному проведению ультразвуковой сварки при температурах порядка 200°C (состояние жидкого азота). Если бы образование соединения было связано с плавлением металлов, понижение температуры окружающей среды на 220°C наверняка сильно повлияло бы на принципиальную возможность получения такого соединения. Во внешнем мире, кстати, этот процесс называют не сваркой, а обозначают термином «бондинг» (bonding), то есть «присоединение, прикрепление, спайка». Возможно, с развитием несырьевых секторов отечественной промышленности термин «бондинг» приживётся и у нас.
Описанная модель соединения кристаллических решёток металлов без нагрева и плавления сначала вызывает сомнения, особенно концепция «жёсткой сцепки» проволоки с рабочим инструментом в ходе всего процесса. Гораздо проще представить себе, что на последних стадиях процесса (как только проволока «прилипает» к подложке) инструмент начинает скользить по проволоке, а не изменяет волшебным образом её внутреннюю структуру. Другими словами, мы утверждаем, что инструмент, ухватив проволоку «за спину», перемешивает с её помощью структуру кристаллической решётки в области контакта с подложкой без её плавления (фазового перехода в жидкое состояние и обратно). Однако есть еще как минимум три довода в пользу такой модели:
1. Путём уменьшения силы прижима инструмента (одного из главных параметров, см. выше) мы можем специально ослабить контакт между ним и проволокой уже после начала образования соединения. При этом инструмент начинает именно «скользить» вдоль проволоки в то время, как уже образовавшиеся зерна соединения удерживают её на подложке. Такое проскальзывание инструмента приводит к появлению обожжённых участков на проволоке вследствие перегрева трением об инструмент. При увеличении прижима до нормального значения этот эффект полностью исчезает, следовательно, при образовании соединения инструмент не скользит по проволоке даже после того, как она прочно соединяется с подложкой.
2. Весьма часто проявляется эффект отслоения («вырывания») металлизации контактной площадки в силу слабой адгезии или дефекта самой подложки. При этом отслоившаяся металлизация и проволока остаются связанными прочным соединением. Если в паре проволока-подложка не происходит колебаний малой амплитуды после образования прочного соединения (сама проволока и подложка находились бы после образования соединения в покое, а колеблется только инструмент, скользя по верхней поверхности проволоки), что тогда вызывает отрыв металлизации?
3. Модель формирования соединения подтверждается экспериментом и наблюдением. С развитием технологий микровидеосъёмки стало возможным провести детальный анализ процесса ультразвукового соединения металлов. В частности, когда в институте IZM (общество Фраунгофера) в Берлине группы Ланга и Шнейдера-Рамелоу провели исследования замедленной съёмки процесса при высоком увеличении, была зафиксирована вся последовательность стадий образования соединения, описанная выше, начиная с синхронного движения инструмента и проволоки по подложке и заканчивая эффектом уменьшения амплитуды колебаний от инструмента к подложке при сохранении её колебаний меньшей амплитуды уже после образования соединения на стадии нагартовки. Ещё одним подтверждением стали и результаты, полученные на лазерном измерителе вибрации, с помощью которого удалось проанализировать амплитуду и частоту колебаний на конце инструмента, проволоке и контактной площадке от начала и до конца процесса.
Далее мы поговорим о том, почему при выборе оптимальной частоты ультразвука необходимо учитывать тип материалов, с которыми предполагается работать.
Сварка ультразвуковая пластика, пластмасс, металлов, полимерных материалов, алюминиевых профилей. Ультразвуковая сварка: технология, вредные факторы
Ультразвуковая сварка металлов представляет собой процесс, в ходе которого получают неразъемное соединение в твердой фазе. Формирование ювенильных участков (в которых образуются связи) и контакт между ними происходят под воздействием специального инструмента. Он обеспечивает совместное действие относительных знакопеременных тангенциальных смещений небольшой амплитуды и сжимающей нормальной силы на заготовки. Рассмотрим далее подробнее, что собой представляет технология ультразвуковой сварки.
Механизм соединения
Малоамплитудные смещения происходят между деталями с ультразвуковой частотой. За счет них микронеровности на поверхности деталей подвергаются пластическому деформированию. Вместе с этим из зоны соединения эвакуируются загрязнения. Ультразвуковые механические колебания передаются к участку сварки от инструмента с внешней стороны заготовки. Весь процесс организуется таким образом, чтобы исключить проскальзывания приспособления и опоры по поверхностям деталей. В процессе прохождения колебаний сквозь заготовки происходит рассеивание энергии. Это обеспечивается внешним трением между поверхностями на начальной стадии сварки и внутренним трением в материале, располагающемся между опорой и инструментом после формирования участка схватывания. В соединении при этом повышается температура, что облегчает деформацию.
Специфика поведения материала
Тангенциальные перемещения между деталями и напряжения, которые вызываются ими и действуют вместе со сжатием от силы сварки, обеспечивают локализацию интенсивной пластической деформации в небольших объемах в приповерхностных слоях. Весь процесс сопровождается размельчением и механической эвакуацией оксидных пленок и прочих загрязнений. Сварка ультразвуковая обеспечивает снижение предела текучести, благодаря чему облегчается пластическая деформация.
Особенности процесса
Сварка ультразвуковая способствует формированию необходимых условий для соединения. Это обеспечивается за счет механических колебаний преобразователя. Благодаря энергии вибрации создаются сложные напряжения среза, сжатия и напряжения. Пластическая деформация возникает при превышении пределов упругости материалов. Получение прочного соединения обеспечивается за счет увеличения площади непосредственного соприкосновения после эвакуации поверхностных оксидов, органических и адсорбированных пленок.
Применение УЗ
Ультразвук широко используется в научной сфере. С его помощью ученые исследуют ряд физических свойств веществ и явлений. В промышленности ультразвук применяется для обезжиривания и очистки изделий, работы с труднообрабатываемыми материалами. Кроме этого, колебания благоприятно воздействуют на кристаллизующиеся расплавы. Ультразвук обеспечивает в них дегазацию и измельчение зерна, повышение механических свойств литых материалов. Колебания способствуют снятию остаточных напряжений. Они также широко применяются для увеличения скорости медленно протекающих химических реакций. Сварка ультразвуковая может использоваться в разных целях. Колебания могут стать источником энергии для образования шовных и точечных соединений. При воздействии ультразвука на сварочную ванную при кристаллизации улучшаются механические свойства соединения за счет измельчения структуры шва и интенсивному удалению газов. За счет того, что колебания активно удаляют загрязнения, искусственные и естественные пленки, соединять можно детали, с окисленной, лакированной и пр. поверхностью. Ультразвук способствует уменьшению или устранению собственных напряжений, появляющихся при сварке. За счет колебаний можно стабилизировать составляющие структуру соединения. Это, в свою очередь, позволяет предотвратить вероятность самопроизвольной деформации конструкций впоследствии. Ультразвуковая сварка находит в последнее время все более широкое применение. Это обусловлено несомненными преимуществами этого способа соединения в сравнении с холодным и контактным методами. Особенно часто используются УЗ колебания в микроэлектронике.
Перспективным направлением считается ультразвуковая сварка полимерных материалов. Некоторые из них невозможно соединить никаким иным методом. На промышленных предприятиях в настоящее время осуществляется ультразвуковая сварка тонкостенных алюминиевых профилей, фольги, проволоки. Особенно эффективен этот метод для соединения изделий из разнородного сырья. Ультразвуковая сварка алюминия используется в производстве бытовых приборов. Этот метод эффективен при сращивании листового сырья (никеля, меди, сплавов). Ультразвуковая сварка пластмасс нашла применение в производстве приборов оптики и тонкой механики. В настоящее время созданы и внедрены в производство машины для соединения разнообразных элементов микросхем. Приспособления оснащаются автоматическими устройствами, за счет которых существенно повышается производительность.
Мощность УЗ
Ультразвуковая сварка пластика обеспечивает неразъемное соединение за счет совместного действия высокочастотных механических колебаний и сравнительно небольшой сдавливающей силы. Этот метод имеет много общего с холодным способом. Мощность УЗ, которую можно передать через среду, будет зависеть от физических свойств последней. При превышении пределов прочности в зонах сжатия, твердый материал разрушится. В аналогичных ситуациях в жидкостях возникает кавитация, сопровождающаяся появлением мелких пузырьков и их последующим захлопыванием. Вместе с последним процессом возникают местные давления. Такое явление используется при очистке и обработке изделий.
Узлы устройств
Ультразвуковая сварка пластика осуществляется с использованием специальных машин. В них присутствуют следующие узлы:
Колебательная механическая система.
Колебательная система используется для преобразования электроэнергии в механическую для последующей ее передачи на участок соединения, концентрирования ее и получения требуемой величины скорости излучателя. В этом узле присутствуют:
Электромеханический преобразователь с обмотками. Он заключен в металлический корпус и охлаждается водой.
Трансформатор упругих колебаний.
Опора с механизмом давления.
Крепление системы осуществляется с помощью диафрагмы. Излучение ультразвука происходит только в момент сварки. Процесс происходит под воздействием колебаний, давления, приложенного под прямым углом к поверхности, и теплового эффекта.
Возможности метода
Сварка ультразвуковая наиболее эффективна для пластичного сырья. Изделия из меди, никеля, золота, серебра и пр. могут соединяться как друг с другом, так и с другими малопластичными изделиями. С повышением твердости свариваемость ультразвуком ухудшается. Эффективно соединяются с помощью УЗ тугоплавкие изделия из вольфрама, ниобия, циркония, тантала, молибдена. Ультразвуковая сварка полимеров считается относительно новым способом. Такие изделия могут также соединяться как друг с другом, так и с другими твердыми деталями. Что касается металла, то его можно соединять со стеклом, полупроводниками, керамикой. Связывать заготовки можно и через прослойку. К примеру, стальные изделия сваривают друг с другом через алюминиевую пластику. За счет кратковременности пребывания под повышенной температурой получается высококачественное соединение разнородных изделий. Свойства сырья подвергается незначительным изменениям. Отсутствие посторонних примесей – одно из преимуществ, которым обладает ультразвуковая сварка. Вредные факторы для человека также отсутствуют. При соединении создаются благоприятные гигиенические условия. Связи изделий отличаются химической однородностью.
Особенности соединения
Сварка металла осуществляется, как правило, нахлесточным способом. При этом добавляется различное конструктивное оформление элементов. Сварка может осуществляться точками (одной или несколькими), непрерывным швом либо по замкнутому кругу. В некоторых случаях при предварительной формовке конца заготовки из проволоки производится тавровое соединение ее с плоскостью. Можно осуществлять ультразвуковую сварку нескольких материалов одновременно (пакетом).
Толщина деталей
Она ограничена верхним пределом. При увеличении толщины металлической заготовки нужно применять колебания с большей амплитудой. Это позволит компенсировать потерю энергии. Увеличение амплитуды, в свою очередь, возможно до определенного предела. Ограничения связаны с вероятностью возникновения усталостных трещин, больших вмятин от инструмента. В таких случаях следует оценить, насколько целесообразна будет ультразвуковая сварка. На практике метод используется при толщине изделий от 3…4 мкм до 05…1 мм. Сварка может использоваться и для деталей с диаметром 0.01…05 мм. Толщина второго изделия может быть существенно больше первого.
Возможные проблемы
При применении метода ультразвуковой сварки необходимо учесть вероятность усталостного разрушения имеющихся соединений в изделиях. Во время процесса заготовки могут разворачиваться относительно друг друга. Как выше было сказано, на поверхности материала от инструмента остаются вмятины. Само устройство отличается ограниченным сроком службы, что обусловлено эрозией его рабочей плоскости. В отдельных точках материал изделия приваривается к инструменту. Это приводит к износу устройства. Ремонт оборудования сопровождается рядом сложностей. Они связаны с тем, что сам инструмент выступает как элемент неразборной единой конструкции узла, конфигурация и размеры которого рассчитаны точно на рабочую частоту.
Подготовка изделий и параметры режима
Перед выполнением ультразвуковой сварки каких-либо сложных мероприятий с поверхностью деталей осуществлять не нужно. При желании можно повысить стабильность качества соединения. Для этого целесообразно только обезжирить изделие растворителем. Для соединения пластичных металлов оптимальным считается цикл с запаздыванием импульса относительно момента запуска ультразвука. При сравнительно высокой твердости изделия целесообразно дождаться небольшого нагрева, прежде чем включать УЗ.
Схемы сварки
Их существует несколько. Технологические схемы УЗ сварки отличаются по характеру колебания инструмента. Они могут быть крутильными, изгибными, продольными. Также схемы различают в зависимости от пространственного положения устройства относительно поверхности свариваемой детали, а также по способу передачи сжимающих сил на изделия и конструктивными особенностями опорного элемента. Для контурного, шовного и точечного соединения используются варианты с изгибными и продольными колебаниями. Ультразвуковое воздействие может сочетаться с локальным импульсным нагревом деталей от отдельного теплового источника. В этом случае можно достичь ряда преимуществ. В первую очередь можно уменьшить амплитуду колебаний, а также силу и время их пропускания. Энергетические свойства теплового импульса и периода его наложения на ультразвук выступают как дополнительные параметры процесса.
Тепловой эффект
Ультразвуковая сварка сопровождается повышением температуры на участке соединения. Возникновение тепла обуславливается появлением трения на поверхностях контактирующих изделий, а также пластическими деформациями. Они, собственно, сопровождают формирование сварного соединения. Температура на контактном участке будет зависеть от прочностных параметров. Главным из них считается степень твердости материала. Кроме того, немалое значение имеют его теплофизические свойства: теплопроводность и теплоемкость. На температурный уровень влияет и выбранный режим сварки. Как показывает практика, появляющийся тепловой эффект не выступает как определяющее условие. Это обуславливается тем, что максимальная прочность соединений в изделиях достигается раньше, чем температура повышается до предельного уровня. Уменьшить продолжительность пропускания ультразвуковых колебаний можно, предварительно проведя подогрев деталей. Это также будет способствовать усилению прочности соединения.
Ультразвуковая сварка в настоящее время в некоторых промышленных отраслях является незаменимым методом соединения деталей. Особенно распространен этот способ в микроэлектронике. УЗ позволяет соединять самые разные пластичные и твердые материалы. Сегодня активно ведется научная работа по усовершенствованию инструментов и технологий сварки.
Советуем подписаться на наши страницы в социальных сетях: Facebook | Вконтакте | Twitter | Google+ | Одноклассники
Читайте также: