Почему металл нагревается при деформации
Обновлено: 18.05.2024
Нагрев деформированного металла не только сказывается на изменении статических характеристик металла, но и заметно влияет на изменение предела выносливости. Это имеет большое значение применительно к тем деталям, которые в процессе изготовления или в условиях эксплуатации подвергаются кратковременному воздействию повышенной температуры. [2]
При нагреве деформированного металла выделяется энергия, накопленная при пластической деформации, металла; в процессе возврата выделяется только часть этой энергии. Калориметрические исследования [146] показали, что при возврате меди выделяется только 3 - 10 % общей энергии, а основная часть выделяется при рекристаллизации. [4]
При нагреве деформированного металла имеется другая возможность образования более совершенной структуры и приближения к равновесию - без протекания полигонизации. Будут ли реализованы оба процесса - полигонизация и рекристаллизация - или один из них, зависит от многих факторов. Полигонизация чаще наблюдается после слабой деформации, рекристаллизация - после значительной. [5]
При нагреве деформированного металла до определенной температуры происходит перераспределение дислокаций с уменьшением энергии, но без существенного уменьшения общего числа дислокаций. Перераспределение дислокаций заметно изменяет структуру - в теле зерна возникает большое количество мелких субзерен, свободных от дислокаций ( блоки, полигоны), слабо разориентированных одно относительно другого. Этот процесс называется полигонизацией. [6]
При нагреве холодно деформированного металла в нем происходят следующие процессы: 1) возврат ( отдых), 2) рекристаллизация, 3) собирательная рекристаллизация. Как видно из фиг. [7]
Возвратом называется нагрев деформированного металла до сравнительно низких температур, вызывающий снятие значительной части внутренних напряжений и caMonpOH3BOJijbHoe устранение искажений в кристаллической решетке, происходящее вследствие тепловых колебаний атомов. Некоторая часть напряжений остается, и обломки зерен сохраняются. [8]
Возврат - нагрев деформированных металлов и сплавов ниже температуры их рекристаллизации ( - 0 2 Тт), выдержка и медленное охлаждение ( с печью) для частичного восстановления их структурного совершенства в результате уменьшения плотности дефектов строения, однако без заметных визуально изменений микроструктуры. Возврат обусловлен микроструктурными изменениями внутри каждого зерна. Возврат включает две стадии - отдых и полигонизацию. [9]
Какие процессы протекают при нагреве деформированного металла выше температуры рекристаллизации. Как изменяются при этом структура и свойства. [10]
Отжиг этого вида заключается в нагреве деформированного металла до температуры, не превышающей температуру рекристаллизации, ведет к перераспределению дислокаций внутри скоплений по типу полпгонизации и сопровождается часто образованием сегрегации на дефектах. В результате этого процесса дислокации образуют стабильные конфигурации, что сопровождается уменьшением искажений кристаллической решетки и повышением сопротивления деформированию. [11]
Снятие искажений кристаллической решетки при нагреве деформированного металла приводит к частичному возврату прежних механических свойств: прочность и твердость снижаются, а пластичность повышается. Этот процесс называется отдыхом или возвратом. Исходный до пластической деформации уровень прочности и пластичности в результате одного только возврата достигнут быть не может. Вытянутые и раздробленные зерна сохраняются. [13]
Скрытая энергия деформации выделяется при нагреве деформированного металла в достаточно широкой области температур, причем для чистых металлов часто наблюдается только один экстремум ( рис. 151), а в сплавах - два, иногда три экстремума. [15]
Большая Энциклопедия Нефти и Газа
Тепловой эффект деформации.
Ранее установлено, что упругая деформация – процесс обратимый, а пластическая – необратимый. В соответствии с законом сохранения энергии работа пластической деформации изменяет внутреннюю энергию кристалла. Деформация приводит к увеличению плотности дислокаций и образованию различных дефектов кристаллической решетки. Поэтому внутренняя энергия кристалла возрастает. Экспериментальные исследования показывают, что только незначительная часть работы Апл переходит в энергию искажения решетки. В основном затраченная на пластическую деформацию работа переходит в тепловую энергию.
Обозначим работу деформации, переходящую в тепло, Ат и выразим ее через полную работу пластической деформации Апл и коэффициент выхода тепла ηт:
На основании экспериментальных данных установлено, что ηт = 0,75. 0,85 для сплавов. Это означает, что свыше трех четвертей работы деформации переходит в тепловую энергию и температура тела в очаге деформации повышается.
Тема 6
НАГРЕВ И РАЗУПРОЧНЕНИЕ ДЕФОРМИРОВАННЫХ
МЕТАЛЛОВ
Нагрев и последующее охлаждение деформированных металлов приводят к существенным изменениями, связанным с упорядочением решетки, уменьшением количества дефектов и обусловливают разупрочнение металлов. Причинами этих изменений являются возврат и рекристаллизация.
Возврат. Упрочнение металла при деформации определяется совместным влиянием дефектов. Однако подвижность точечных, линейных и двумерных дефектов различна. Поэтому при нагреве и последующем охлаждении деформированных металлов наблюдаются изменения, обусловленные прежде всего точечными и линейными дефектами, которые обладают наибольшей подвижностью. В литературе эти изменения связывают с возвратом. Возврат – это процесс упорядочения кристаллической решетки деформированных металлов при их нагреве и охлаждении, приводящий к изменению субструктуры металлов. При возврате упорядочение кристаллической решетки происходит в пределах субзерен и не вызывает структурных изменений. Поэтому механические свойства деформированных металлов изменяются, не очень значительно (рис. 6.1).
6.1 |
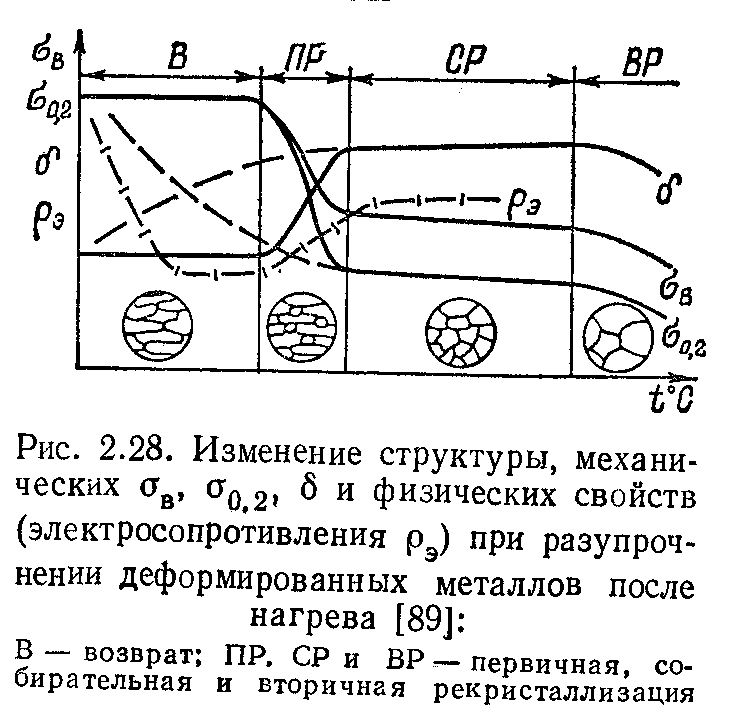
В процессе возврата принято различать две стадии: отдых и полигонизацию. Нагрев деформированного металла до температуры Т ≈ 0,2Тпл, выдержка и последующее охлаждения приводят к отдыху. В результате отдыха значительно уменьшается количество точечных дефектов; избыточные вакансии устремляются к стокам, и их концентрация приходит к равновесной. Межузельные атомы занимают места вакансий. Дислокации противоположных знаков, лежащих в одних и тех же плоскостях скольжения в пределах субзерен, частично аннигилируют. В процессе отдыха происходят несущественные изменения, связанные с упорядочением решетки. Поэтому ощутимо изменяются только физические свойства, например электропроводность, которые сильно зависят от концентрации точечных дефектов. После нагрева до температуры 0,2ТплТТпл, выдержки и охлаждения происходит полигонизация. Под влиянием нагрева дислокации приобретают более высокую подвижность и образуют устойчивые конфигурации, которые приводят к уменьшению внутренней энергии решетки. Такими конфигурациями являются стенки дислокаций. Следовательно, после нагрева до температуры Т < 0,3Тпл, выдержки и охлаждения строение деформированного металла (его субструктура) существенным образом изменяется: снижаются концентрация вакансий и плотность дислокаций, дислокации выстраиваются в стенки и образуют субграницы, формируются области, почти свободные от дислокаций. Это вызывает ощутимые изменения физических и механических свойств: снижаются твердость и предел текучести, повышаются пластичность, уменьшается (в большинстве случаев) электрическое сопротивление.
Рекристаллизация. Дальнейшее повышение температуры обусловливает подвижность двумерных дефектов. По этой причине изменения в строении деформированных металлов захватывают уже структуру (зерна поликристаллических металлов). Такие глубокие изменения в структуре металлов обусловлены рекристаллизацией. Рекристаллизация – это процесс образования новых равноосных зерен вместо ориентированной волокнистой структуры деформированного металла. Новые зерна, в основном свободные от напряжений, имеют гораздо меньшую твердость и сопротивление деформации. Они образуются и растут за счет искаженных и поэтому неравновесных зерен деформированного металла. Процесс продолжается до тех пор, пока в структуре не исчезнут искаженные неравновесные зерна. Рекристаллизация различных металлов начинается при температурах около 0,4Тпл. Эта температура весьма условна и характерна для металлов технической чистоты. Для химически чистых металлов она снижается до (0,1…0,2) Тпл.
При рассмотрении кинетики рекристаллизации принято различать следующие три стадии: первичную, собирательную и вторичную рекристаллизации.
Первичная рекристаллизация – это процесс образования устойчивых зародышей, из которых растут новые неискаженные зерна. Металлографическими методами получены прямые доказательства того, что зародыши при рекристаллизации появляются на участках с наибольшими искажениями, т.е. на границах зерен и субзерен. Чтобы ясно представить кинетику собирательной рекристаллизации, необходимо учесть, что повышение температуры металлов вызывает диффузию.
Диффузия – это перемещение атомов в кристаллическом теле на расстояния, превышающие параметр решетки. Одна из важнейших характеристик диффузии – ее скорость, т.е. количество вещества m, перемещающегося через единицу площади поверхности за единицу времени.
Резкое повышение подвижности атомов при нагреве вызывает перестройку кристаллической структуры деформированных металлов: из состояний неустойчивого равновесия в сильно искаженных областях кристаллитов атомы переходят в положения устойчивого равновесия, подстраиваясь к неискаженным решеткам зародышей новых зерен. Этот процесс начинает интенсивно протекать при температуре, превышающей 0,4Тпл, и называется собирательной рекристаллизацией.В процессе собирательной рекристаллизации размеры зерен увеличиваются.
Рис. 6.2. Пространственная диаграмма рекристаллизации стали 50. |
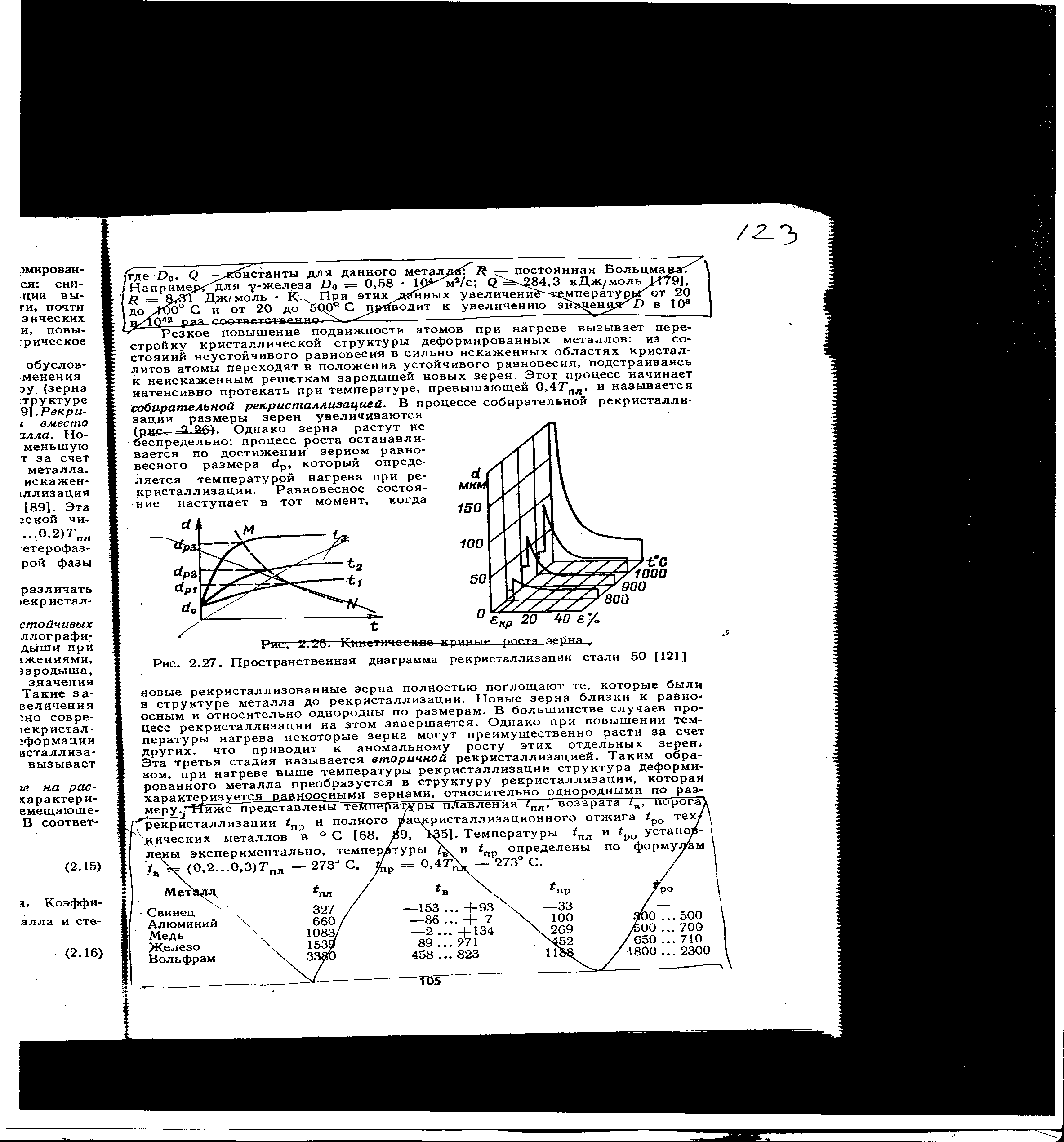
Однако зерна растут не беспредельно: процесс роста останавливается по достижении зерном равновесного размера dр, который определяется температурой нагрева при рекристаллизации. Равновесное состояние наступает в тот момент, когда новые рекристаллизованные зерна полностью поглощают те, которые были в структуре металла до рекристаллизации. Новые зерна близки к равноосным и относительно однородны по
размерам. В большинстве случаев процесс
рекристаллизации на этом завершается.
Однако при повышении температуры нагрева некоторые зерна могут преимущественно расти за счет других, что приводит к аномальному росту этих отдельных зерен. Эта третья стадия называетсявторичной рекристаллизацией. Таким образом, при нагреве выше температуры рекристаллизации структура деформированного металла преобразуется в структуру рекристаллизации, которая характеризуется равноосными зернами, относительно однородными по размеру.
Конечный размер зерен зависит от температуры нагрева, а также в значительной мере от степени предшествовавшей холодной пластической деформации. Чтобы наглядно представить эту связь, строят трехмерные диаграммы рекристаллизации. Анализ диаграмм показывает, что рекристаллизация начинается только по достижении критической степени деформации εкр (рис. 6.2). При ε ≈ εкр происходит резкое увеличение размера зерна. Для чистых металлов εкр лежит в интервале 1…5%, для сплавов – в пределах 5…15%. В большинстве случаев с повышением температуры значение εкр уменьшается. При увеличении степени деформации размер зерна, как правило, уменьшается. Эти важные свойства диаграмм рекристаллизации следует иметь в виду при назначении режимов деформации холодной штамповки. Если в процессе ОМД деформация попадает в интервал критических соответствующих данной марке материала, то после нагрева и рекристаллизации получим деталь с крупнозернистой структурой и пониженными механическими свойствами.
Влияние нагрева на структуру и свойства деформированного металла
Около 10…15 % всей энергии, затраченной на пластическую деформацию, поглощается металлом и накапливается в нем. Остальная часть энергии идет на нагрев металла.
Деформированный металл находится в неравновесном, неустойчивом состоянии, и в нем могут протекать процессы, направленные на достижение устойчивого состояния. Этот переход связан с уменьшением искажений в кристаллической решетке и снятием напряжений, что в свою очередь определяется возможностью перемещения атомов.
С повышением температуры подвижность атомов увеличивается и начинают развиваться процессы, приводящие металл к равновесному состоянию. По мере нагрева деформированный металл проходит стадии возврата и рекристаллизации, в результате чего изменяются его структура и свойства (рисунок 20).
В области возврата (при нагреве до 0,3 Тпл) происходит повышение структурного совершенства металла в результате уменьшения плотности дефектов строения. При этом не наблюдается заметных изменений структуры, видимой в оптический микроскоп. Механические свойства металла изменяются незначительно, порядка на 5…7 %.
При низких температурах (ниже 0,2 Тпл) протекает первая стадия возврата — отдых, когда происходит уменьшение точечных дефектов (вакансий) и перераспределение дислокаций без образования субграниц. При нагреве вакансии поглощаются дислокациями, которые двигаются к границам зерен. Часть дислокаций противоположного знака уничтожается.
Вторая стадия возврата — полигонизация, под которой понимают дробление (фрагментацию) кристаллов на субзерна (полигоны). При нагреве беспорядочно распределенные дислокации одного знака выстраиваются в дислокационные стенки, что приводит к образованию в монокристалле или в зерне поликристалла субзерен (полигонов), свободных от дислокаций и отделенных дислокационными границами (рисунок 21).
Этот процесс протекает обычно при небольших деформациях при температуре (0,25…0.3)Тпл, и им создаются условия для образования в структуре металла зародышей новых зерен.
Рисунок 21 — Схема процесса полигонизации
Стадия первичной рекристаллизации в деформированном металле происходит при его нагреве выше 0,3Тпл. При высоких температурах подвижность атомов возрастает и образуются новые равноосные зерна.
Образование новых, равноосных зерен вместо ориентированной волокнистой структуры деформированного металла называется первичной рекристаллизацией.
В деформированном металле на участках с повышенной плотностью дислокаций образуются и растут зародыши. Образуется совершенно новое зерно, по размерам отличающееся от исходного до деформации. Наклеп практически полностью снимается, и свойства приближаются к их исходным значениям.
Температура, при которой начинается процесс рекристаллизации называется температурным порогом рекристаллизации.
Температурный порог рекристаллизации (Тр) связан с температурой плавления металла зависимостью А.А.Бочвара:
где Тпл — абсолютная температура плавления, К;
а — коэффициент, зависящий от чистоты металла.
Для металлов высокой чистоты а = 0,1…0,2; для технически чистых металлов а=0,4; для сплавов твердых растворов а = 0,5…0,6.
Для некоторых металлов значение температурного порога рекристаллизации приведено в таблице 2.
Рекристаллизационный отжиг малоуглеродистых сталей проводят при 600…700 0 С, латуней и бронз при 560…700 0 С, алюминиевых сплавов при 350…450 0 С, титановых сплавов при 550…750 0 С.
Собирательная рекристаллизация проходит после завершения первичной рекристаллизации в процессе дальнейшего нагрева. Она заключается в росте образовавшихся новых зерен. Движущей силой собирательной рекристаллизации является поверхностная энергия зерен. При укрупнении зерен общая протяженность их границ становится меньше, что соответствует переходу металла в более равновесное состояние.
Таблица 2 — Температура начала рекристаллизации технически чистых металлов
Металл | Температура плавления, 0 С | Температура рекристаллизации, 0 С |
Вольфрам | 3400 | 1200 |
Молибден | 2625 | 900 |
Железо | 1539 | 450 |
Медь | 1083 | 200 |
Алюминий | 660 | 100 |
Особенность собирательной рекристаллизации состоит в том, что рост происходит не в результате слияния нескольких мелких зерен в одно более крупное зерно, а одни зерна растут за счет других зерен, ”поедая” их вследствие перехода атомов через границы раздела. Зерна с вогнутыми границами растут за счет зерен с выпуклыми границами (рисунок 22). Атом на вогнутой поверхности имеет большее число соседей и, следовательно, меньшую энергию, по сравнению с атомами на выпуклой поверхности. Малые зерна постепенно исчезают. Собирательная рекристаллизация, вызывающая образование крупного зерна и разнозернистости, способствует снижению механических свойств металлов и поэтому чаще всего недопустима для наклепанного металла.
Рисунок 22 — Схема роста зерен при собирательной рекристаллизации
На свойства металла большое влияние оказывает размер зерен, получившихся при рекристаллизации. Основными факторами, определяющими величину зерен металла при рекристаллизации, являются температура, продолжительность выдержки при нагреве и степень производительной пластической деформации (рисунок 23).
Величина зерна возрастает с повышением температуры нагрева и времени выдержки. При температурах Т1 и Т2 (выше Тр) образование рекристаллизованного зерна происходит не сразу, а через некоторый отрезок времени t1 и t2, который называется инкубационным.
Рисунок 23 — Влияние температуры (а), продолжительности нагрева (б) и степени деформации (в) на величину рекристаллизованного зерна
Наиболее крупные зерна образуются после незначительной предварительной деформации, обычно порядка 3…15 %, такую степень деформации называют критической.
Критической называют такую минимальную степень деформации, выше которой при нагреве становится возможной первичная рекристаллизации.
Процессы при нагреве деформированного металла
Рекристаллизация является диффузионным процессом и протекает неравномерно, одни зерна зарождаются и растут раньше, другие позднее. После рекристаллизации металл состоит из новыхравноосных зерен. Более высокий нагрев приводит к развитию собирательной рекристаллизации, т. е. к росту одних рекристаллизованных зерен за счет других, более мелких. Чем выше температура нагрева, тем интенсивнее идет собирательная рекристаллизация, так как с повышением температуры диффузионные процессы протекают быстрее и создаются условия для образования крупнозернистого металла. Собирательная рекристаллизация также протекает неравномерно и практически начинается значительно раньше, чем закончится рекристаллизация обработки.
Рисунок 1 – Схема влияния на величину рекристаллизованного зерна
температуры (а) и продолжительности нагрева (б)
Размер рекристаллизованного зерна оказывает большое влияние на свойства металла. Наилучшее сочетание прочности и пластичности наблюдается в мелкозернистых сталях. На величину рекристаллизованного зерна оказывает влияние температура рекристаллизационного отжига (рисунок1, а), продолжительность процесса (рисунок 1, б), степень предварительной деформации и химический состав металла. Чем выше температура отжига и длительнее процесс, тем больше размеррекристаллизованного зерна.
Рисунок 1 – Схема влияния температуры на механические свойства и
структуру деформированного металла
При нагреве по достижении температуры начала рекристаллизации (tнр) предел прочности и особенно предел текучести резко снижаются, а пластичность увеличивается. В процессе собирательной рекристаллизации механические свойства практически не изменяются. Более высокий нагрев сопровождается дальнейшим ростом зерна и уменьшением пластичности вследствие перегрева.
Деформированный металл по сравнению с недеформированным имеет повышенный запас энергии и находится в неравновесном, термодинамически неустойчивом состоянии. В таком металле даже при комнатной температуре могут самопроизвольно протекать процессы, приводящие его в более устойчивое состояние. Однако, если деформированный металл нагреть, то скорость этих процессов возрастает. Небольшой нагрев (для железа 300-400°С) ведет к снятию искажений кристаллической решетки, но микроструктура остается без изменений, зерна по-прежнему вытянуты. Прочность при этом несколько; снижается, а пластичность повышается. Такая обработка называется возвратом или отдыхом.
При дальнейшем повышении температуры подвижность атомов возрастает и среди вытянутых зерен идет интенсивное зарождение и рост новых равноосных свободных от напряжений зерен. Зародыши новых зерен возникают в участках с наиболее искаженной кристаллической решеткой, с повышенным уровнем свободной энергии, термодинамически наименее устойчивых. Новые зерна растут за счет старых, вытянутых, до их столкновения друг с другом и до полного исчезновения вытянутых зерен. Это явление называется рекристаллизацией (первичной).
Рекристаллизация является диффузионным процессом и протекает неравномерно, одни зерна зарождаются и растут раньше, другие позднее. После рекристаллизации металл состоит из новых равноосных зерен. Более высокий нагрев приводит к развитию собирательной рекристаллизации, т. е. к росту одних рекристаллизованных зерен за счет других, более мелких. Чем выше температура нагрева, тем интенсивнее идет собирательная рекристаллизация, так как с повышением температуры диффузионные процессы протекают быстрее и создают условия для образования крупнозернистого металла.
6. Диаграмма состояния железо-цементит
В системе железо — цементит существуют следующие фазы: жидкая фаза, феррит, аустенит, цементит, графит.
1. Жидкая фаза. В жидком состоянии железо хорошо растворяет углерод в любых пропорциях с образованием однородной жидкой фазы.
2. Феррит — Твёрдый раствор внедрения углерода в α-железе с ОЦК (объёмно-центрированной кубической) решёткой.
Феррит имеет переменную предельную растворимость углерода: минимальную — 0,006 % при комнатной температуре (точка Q), максимальную — 0,02 % при температуре 727 °C (точка P). Атомы углерода располагаются в центре грани или (что кристаллогеометрически эквивалентно) на середине рёбер куба, а также в дефектах решетки.
При температуре выше 1392 °C существует высокотемпературный феррит, с предельной растворимостью углерода около 0,1 % при температуре около 1500 °C (точка I)
Свойства феррита близки к свойствам чистого железа. Он мягок (твердость — 130 НВ) и пластичен, магнитен (при отсутствии углерода) до 770 °C.
3. Аустенит (γ) — твёрдый раствор внедрения углерода в γ-железе с ГЦК (гране-центрированной кубической) решёткой.
Атомы углерода занимают место в центре гранецентрированной кубической ячейки.
Предельная растворимость углерода в аустените — 2,14 % при температуре 1147 °C (точка Е).
Аустенит имеет твёрдость 200—250 НВ, пластичен, парамагнитен.
При растворении других элементов в аустените или в феррите изменяются свойства и температурные границы их существования.
4. Цементит (Fe3C) — химическое соединение железа с углеродом (карбид железа), со сложной ромбической решёткой, содержит 6,67 % углерода. Он твёрдый (свыше 1000 HВ), и очень хрупкий. Цементит фаза метастабильная и при длительным нагреве самопроизвольно разлагается с выделением графита.
7. Классификация и маркировка сталей и чугунов
низкоуглеродистые, с содержанием углерода до 0,25 %;
среднеуглеродистые, с содержанием углерода 0,3…0,6 %;
высокоуглеродистые, с содержанием углерода выше 0,7 %
– углеродистые стали обыкновенного качества:
в мартеновских печах;
в кислородных конверторах;
в электрических печах: электродуговых, индукционных и др.
конструкционные – применяются для изготовления деталей машин и механизмов;
инструментальные – применяются для изготовления различных инструментов;
специальные – стали с особыми свойствами: электротехнические, с особыми магнитными свойствами и др.
8. Диаграмма изотермического превращения аустенита
Изотермическое превращение аустенита - это превращение переохлаждённого аустенита при постоянной температуре.
Превращение аустенита в перлит заключается в распаде аустенита - твёрдого раствора углерода б у-железег на почти чистое а-железо и цементит.
При температуре равновесия A1 превращение аустенита в перлит невозможно, так как при этой температуре свободные энергии исходного аустенита и конечного перлита равны. Превращение может начаться лишь при некотором переохлаждении.
На рисунке показано время превращения аустенита в перлит в зависимости от степени переохлаждения, т.е. превращение переохлаждённого аустенита при постоянной температуре. Поэтому такие диаграммы обычно называютдиаграммами изотермического превращения аустенита. Кривые на диаграммеизотермического превращения аустенита имеют вид буквы С: поэтому их часто называют С-образными или просто С-кривыми. Горизонтальная линия М показывает температуру начала бездиффузного мартенситного превращения.
Свойства и строение продуктов превращения аустенита зависят от температуры, при которой происходил процесс его распада.
Связь между характеромизотермического превращения аустенита, содержанием углерода и температурой показывает обобщённая диаграмма превращения переохлаждённого аустенита в углеродистой стали.
В зависимости от содержания углерода и степени переохлаждения мы имеем такиеобласти превращений аустенита:
- превращение аустенит — перлит:
- предварительное выделение феррита и затем превращение аустенит —> перлит;
- предварительное выделение цементита и затем превращение аустенит —► перлит;
- превращение аустенит —► бейнит;
- превращение аустенит —► мартенсит и распад остаточного аустенита с образованием бейнита;
- превращение аустенит —► мартенсит:
- переохлаждённый аустенит сохраняется без превращения.
После рассмотрения процесса превращения аустенита при постоянной температуре и разных степенях переохлаждения можно перейти к рассмотрению процесса распада аустенита при непрерывном охлаждении, когда сталь, нагретая до аустенитного состояния, охлаждается с разной скоростью.
Диаграмма изотермического распада аустенита строится в координатах температура-время; в этих же координатах изображаются и кривые охлаждения.
Для более точной оценки превращений, совершающихся при непрерывно меняющейся температуре, пользуются так называемыми теркмокинетическими или анизотер.мическими диаграммами превращений аустенита, диаграммами, характеризующими превращение аустенита при различных скоростях охлаждения.
Хотя диаграммыизотермического превращения аустенита дают много сведений о характере превращений, на практике изотермичность превращения достигается далеко не всегда.
Для полной информации о превращении аустенита той или иной марки стали необходимы как диаграммы изотермического превращения аустенита, так и анизотермического превращения, а также ряд дополнительных сведений: марка стали, температура нагрева, размер зерна аустенита, а также свойства (хотя бы твёрдость') продуктов распада и соотношение структурных составляющих.
Читайте также: