Угол трения сталь по бронзе
Обновлено: 03.05.2024
Основным критерием работоспособности винтовых механизмов (работы [2, 3, 4]) является износостойкость, поэтому материалы винта в гайки должны представлять антифрикционную пару, т. е. быть износостойкими и иметь малый коэффициент трения. Выбор марки материала зависит от назначения передачи, условий работы и способа обработки резьбы.
Для винтов применяют стали 45, 50, 40ХГ, У10 и др. (табл. 1). В ответственных передачах для повышения износостойкости применяют закалку винтов с последующей шлифовкой резьбы. Закалка стали позволяет
повысить величину допустимых удельных давлений [p] (табл. 2),что важно
для уменьшения размеров пары.
Гайки ответственных передач изготовляют из оловянных бронз БрО10Ф1, БрОбЦбСЗ и др., а в тихоходных передачах — из антифрикционных чугунов АЧВ-1, АЧК-1 и др. Остальные детали изготовляют из Ст.З.
Допускаемые напряжения для расчета деталей передачи винт-гайка скольжения принимают по следующим рекомендациям:
1) допускаемое давление в резьбе: сталь по чугуну [р] изн = 5.. .6 Н/мм 2 ; сталь по бронзе [р] изн = 8. 10 Н/мм 2 ; закаленная сталь по бронзе
[р] изн =10. 12 Н/мм 2 . Для винтов домкратов и прессов, т. е. сравнительно редко работающих механизмов, значения [р] изн повышают на 30. 40%;
2) допускаемое напряжение [σ ] на растяжение или сжатие стальных винтов вычисляют по формуле [σ ] p = σ т /[s]T при [s]T = 3;
3) допускаемые напряжения для материала гайки: на смятие бронзы и чугуна по чугуну или стали [σ ] см = 42. 55 Н/мм 2 ; на растяжение: для бронзы [σ ] p = 34. 44 Н/мм 2 , для чугуна [σ ] p = 20. 24 Н/мм 2 .
Механические характеристики материалов
Марка стали | Предел прочнос- ти σ в, МПа | Предел текучести σ т, МПа | Предел выносли- вости σ -1р, МПа | Марка стали | Предел прочнос- ти σ в, МПа | Предел текучести σ т, МПа | Предел выносли- вости, σ -1р, МПа |
СтЗ и 10 | 30Х | ||||||
ЗОХГСА | |||||||
ВТ16 | — |
Теоретическое решение задачи Н.Е.Жуковским о распределении осевой нагрузки по виткам резьбы (10 витков) приведено в литературе [2, 3, 4]. Установлено, что нагрузка по виткам резьбы распределяется неравномерно.
С учетом износа сопряженных винтовых поверхностей расчетный средний диаметр резьбы, в случае неравномерного распределения нагрузки по виткам резьбы определяют по условию износостойкости:
(1)
где Fa – расчетная осевая сила;
A – площадь изнашиваемой поверхности резьбы;
K нр – коэффициент, учитывающий неравномерность распределения нагрузки по виткам резьбы;
K н р = 1.0 при упоре гайки буртом в корпусе;
K н р=1,3…1,5 при отношении временных сопротивлений разрыва материалов винта и гайки σв в/ σв г > 1,3;
K нр= 1,65…1,8 при σв в/ σв г ≤ 1,3 в случае упора гайки в противоположный от бурта торец (работа [3]).
Площадь изнашиваемой поверхности резьбы с числом витков zв
где d 2 – средний диаметр резьбы; H 1 – рабочая высота профиля резьбы;
zв - число витков резьбы, выражаемое через параметры высоты гайки
H г, и шаг резьбы Р как zв= H г/ Р .
Перепишем выражение (1):
Введем обозначения:
Ψ H = H Г /d 2 – коэффициент высоты гайки; Ψ H = 1,2…1,5;
Ψ h =H 1 /P – коэффициент рабочей высоты профиля резьбы: для трапецеидальной и прямоугольной резьбы Ψ h = 0,5; для упорной резьбы Ψ h = 0,75.
С учетом введенных обозначений расчетный средний диаметр резьбы
где [р] изн – допускаемое удельное давление в резьбе (табл.2).
Значение допускаемых удельных давлений [p] изн в резьбе для различных
типов пар винт-гайка [4], Н/мм 2
Материал пары винт-гайка | Закаленная сталь-бронза | Незакаленная сталь-бронза | Незакаленная сталь-чугун | Незакаленная сталь – антифрик- ционный чугун |
[р] | 11…13 | 8…10 | 4…6 | 10…12 |
По полученному значению расчетного среднего диаметра резьбы d׳2 выбирают размеры соответствующего типа резьбы (табл.3, 4):
d׳2; P ; d ; d 3.
Грузовые винты применяются для создания больших осевых сил. При знакопеременной нагрузке винты имеют трапецеидальную резьбу, при большой односторонней нагрузке – упорную. Гайки грузовых винтов цельные. В домкратах для большего выигрыша в силе и обеспечения самоторможения применяют однозаходную резьбу с малым углом подъема.
Трапецеидальная резьба (рис. 1). Это основная резьба в передаче винт-гайка. Ее профиль — равнобочная трапеция, угол профиля a = 30°, угол наклона боковой стороны профиля g = 15°. Шаг может быть крупным, средним и мелким. Характеризуется малыми потерями на трение, технологичностью.
КПД трапецеидальной резьбы выше, чем у резьб с треугольным профилем. Её применяют для передачи реверсивного движения под нагрузкой (ходовые винты станков, прессов, домкратов и т. п.).
Стандартные размеры резьбы приведены в табл. 3,4. Преимущественно используются трапецеидальные резьбы со средними шагами. Мелкий шаг назначают для получения осевых перемещений высокой точности, а крупный — в целях увеличения износостойкости.
P |
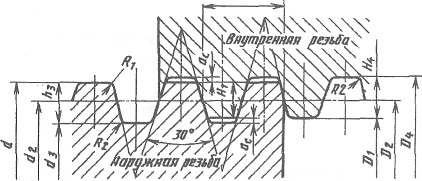
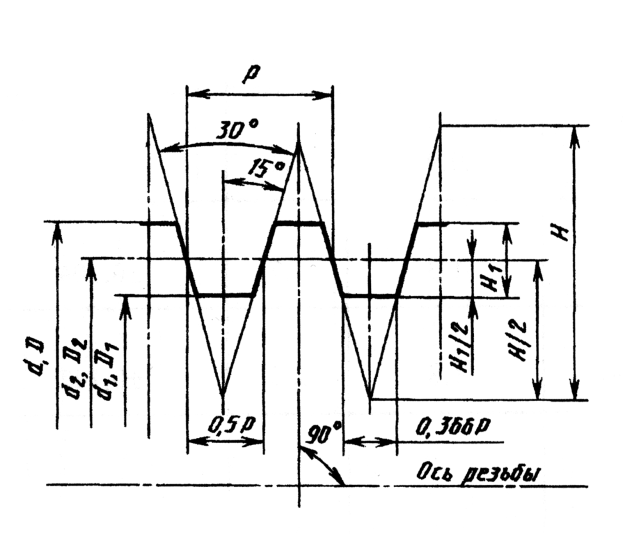
Рис. 1. Основной и номинальные профили наружной и внутренней трапецеидальной резьбы (по гост 9484-81):
d - наружный диаметр резьбы (винта); D - наружный диаметр внутренней резьбы (гайки); d 2 - средний диаметр наружной резьбы; D 2 - средний диаметр внутренней резьбы; d 1 - внутренний диаметр наружной резьбы;
D 1- внутренний диаметр внутренней резьбы; Р - шаг резьбы; Н - высота исходного треугольника; Н 1 - рабочая высота профиля; h 3 - высота профиля наружной резьбы; Н 4 - высота профиля внутренней резьбы; d 3 - внутренний диаметр наружной резьбы; D 4 - наружный диаметр внутренней резьбы;
R1 - радиус скругления по вершине наружной резьбы; R 2 - радиус скругления во впадине наружной и внутренней резьбы; а с - зазор по вершине резьбы.
Пример условного обозначения трапецеидальной однозаходной резьбы номинальным диаметром 20 мм, шагом 4 мм и полем допуска среднего диаметра 7е: Тr 20 х 4 - 7е.
Таблица 3
Диаметры и шаги трапецеидальной однозаходной резьбы (ГОСТ 24738—81).
Номинальные диаметры d | Шаг Р | Номинальные диаметры d | Шаг Р | ||
Ряд 1 | Ряд 2 | Ряд 1 | Ряд 2 | ||
– | – – | 1,5; 2* 1,5; 2 1,5; 2 | — — | – | 3; 8; 12 |
— – | – | 2; 3 2; 3 2; 3 | — | — — | 3; 8; 12 8; 9; 12; 14 0; 9; 12; 14 |
— | – – | 2; 4 2; 4 2; 4 | — – | — | 4; 10; 16 |
– — | — | 2*; 3; 5; 8 2*; 3; 5; 8 2*; 3; 5; 8 | — — | 4; 10; 16 4; 5*; 12;18; 20 4; 5*; 12; 18; 20 | |
– | — – | 2*; 3; 5; 8 3; 6; 10 3; 6; 10 | – | 4; 5*;12; 18; 20* 4; 5*; 12; 20 4; 5*; 12; 20 | |
– — | — | 3; 6; 10 3; 6; 10 6*;7; 10 | – | – – | 6; 14; 16*; 22; 24* 6; 14; 16*; 22; 24* 6; 14; 16*; 24 |
— | — — | 3; 6; 7; 10 3; 6; 7; 10 3; 7; 8; 10 | – — | – | 6; 16; 24 6; 8*; 16; 24*; 28 6; 8*; 16; 24*, 28 |
Примечания : 1. В ГОСТе приведены диаметры резьб до 640 мм и шаги до 48 мм. 2. Шаги, заключенные в рамки, являются предпочтительными при разработке новых конструкций. 3. Шаги, обозначенные звездочкой, не следует применять при разработке новых конструкций. |
Размеры элементов профиля трапецеидальной резьбы (рис. 1) рассчитывают по следующим зависимостям:
d2 = D2 = d - 0,5Р; H = 1,866P;
d3 = d - 2h3; D1 = d - P;
Зазор по вершине резьбы аc определяется шагом (мм):
Р . 1,5 2…5 6…12 14…40
аc. 0,15 0,25 0,5 1
Например, для значений номинального диаметра 40 и 52 мм.
Резьба трапецеидальная (выборка). Размеры, мм (рис. 1)
Номинальный диаметр резьбы d | Шаг резьбы Р | Средний диаметр d 2 | Внутренний диаметр резьбы винта d 3 |
6* 7** | 38,5 36,5 | 36,5 33 | |
3 8** 12 | 50,5 48 46 | 48,5 43 39 |
Примечания : * — шаги не следует применять при разработке новых конст-
рукций;
** — шаги, предпочтительные при разработке новых конструкций.
Для создания значительных односторонних нагрузок применяют упорную резьбу с несимметричным трапецеидальным профилем по
ГОСТ 10177—82 (рис. 2). Очень малый угол наклона рабочей стороны профиля (3°) обеспечивает возможность изготовления резьбы фрезерованием. КПД выше, чем у трапецеидальной резьбы. Закругление впадин повышает сопротивление усталости винта.
Рис. 2. Основные геометрические параметры упорной резьбы
(по ГОСТ 10177-82):
d и D – наружные диаметры соответственно наружной резьбы (винта) и внутренней резьбы (гайки);
d 1 и D 1 – внутренние диаметры соответственно наружной и внутренней резьбы;
D 2 и d 2 – средние диаметры соответственно наружной и внутренней резьбы;
Р – шаг резьбы;
Н – высота исходного треугольника; H 1 – рабочая высота профиля;
d 3 – внутренний диаметр наружной резьбы;
h 3 – высота профиля наружной резьбы;
ас – зазор по вершине резьбы;
R – радиус закругления по впадине наружной резьбы.
Закругления во впадинах наружной резьбы способствуют снижению концентрации напряжений в опасных сечениях и увеличению динамической прочности. Номинальные диаметры и шаги упорной резьбы даны в табл. 5.
Геометрические параметры рассчитывают по формулам:
d 2 = D 2 = d - 0,75Р ; d 3 = d - 1,735534P ; D 1 = d - 1,5P ;
H = 1,587911P ; H 1=0,75P ; h 3 = 0,867767P ; R = 0,124271P.
Условие самоторможения для резьбы: ψ ≤ φ ׳, где ψ – угол подъема резьбы; φ ׳ – приведенный угол трения в резьбе.
Угол подъема резьбыПриведенный угол трения в резьбе φ׳= arctgf ׳, где f ׳– приведенный коэффициент трения в резьбе для трапецеидальной резьбы: f ׳= f /cos 15 o ;
для упорной f ׳= f /cos 3 o , f – коэффициент трения, f = 0,1.
Число витков резьбы гайки
Проверка числа витков резьбы гайки по условию прочности на срез проводится по формуле
где d – наружный диаметр резьбы винта;
k – коэффициент, учитывающий тип резьбы;
k = 0,65 – трапецеидальная и упорная, резьба;
H Г – высота гайки: H Г = P z В;
[t] – допускаемое напряжение среза;
[t] = 0,6σ T/ S , где σ T – предел текучести материала гайки; S – коэффициент запаса прочности, который принимаем S = 3– при расчете на прочность ходового винта, гайки и корпуса, в остальных случаях S =1,5.
[t] = 25…30 Н/мм 2 для гайки из бронзы;
[t] = 70…75 Н/мм 2 для гайки из стали.
ВЫБОР МАТЕРИАЛОВ ПРИ КОНСТРУИРОВАНИИ УЗЛОВ ТРЕНИЯ
Выбор материалов в этом случае представляет собой трудную задачу, так как зависит от конструкции и назначения узлов, технологии производства, условий эксплуатации, от требований к общей прочности деталей, сроку их службы и надежности при учете стоимости материала и эксплуатационных расходов.
Связь некоторых из перечисленных факторов с выбором материалов проследим сначала на примере поршневых колец и цилиндров двигателей внутреннего сгорания. Газоуплотнитель-ные поршневые кольца рабочих цилиндров малооборотных судовых дизелей с низкой тепловой нагрузкой изготовляют из перлитного серого чугуна массовой или индивидуальной отливки, когда цилиндр изготовлен из перлитного чугуна, отливаемого в землю. При надлежащих химическом составе, структуре, технологии отливки и обработке эти материалы обеспечивают высокую износостойкость пары цилиндр — поршневое кольцо. При высоких тепловых нагрузках кольца, например, в автомобильных двигателях, где значительную роль играет коррозионное изнашивание цилиндропоршневой группы, цилиндры и поршневые кольца изготовляют из легированного чугуна. На некоторых двигателях в верхней части цилиндров устанавливают короткие гильзы из нерезита — аустенитного чугуна с высоким содержанием никеля. Нерезит обладает высоким сопротивлением коррозионному изнашиванию, хорошо обрабатывается резцом. Недостатком такой конструкции цилиндра является образование при эксплуатации ступеньки между основным цилиндром и нерези-товой вставкой вследствие разной износостойкости их материалов, что вызывает повышенный износ поршневых колец.
В авиационных поршневых двигателях воздушного охлаждения, со свойственной им высокой тепловой и общей напряженностью работы, относительно тонкостенные цилиндры для обеспечения их высокой износостойкости изготовляют из азотируемой стали. Поршневые кольца, которые при средней температуре порядка 300—400°С должны сохранять значительную упругость и высокую твердость, делают из теплостойкого чугуна ХТВ, легированного хромом, титаном и вольфрамом.
Литые коленчатые валы имеют преимущества по сравнению с валами из кованой стали: экономия металла, снижение трудоемкости, сокращение технологического цикла. Большие возможности имеются в отношении совершенствования конструкции литого вала.
Сплавы, применяемые для. коленчатых валов, можно разделить на содержащие в своей структуре графит (чугуны, графи-тизированная сталь) и не содержащие графит (углеродистая и легированная стали). Сплавы первой группы более износостойки. Поточность производственного процесса легче осуществить при изготовлении чугунных валов. Если за единицу принять стоимость вала, изготовленного из высококачественного чугуна с пластинчатым графитом без термообработки, то стоимость вала из перлитного ковкого чугуна будет 2,5—3,0; из чугуна с шаровидным графитом без термообработки—1,25, с термообработкой— 1,5; из углеродистой стали — 2,5; из легированной етали — 2,5; из графитизированной стали — 3,0—3,3.
Углеродистая сталь уступает чугунам с шаровидным графитом: при почти одинаковых механических свойствах стали и чугуна плавка и разливка последнего проще; в чугунах образуется меньше трещин, износостойкость коленчатых валов, изготовленных из них без термообработки, не ниже, чем валов из углеродистой стали, шейки которых закалены ТВЧ. В литых валах из легированной стали вероятность образования флокенов меньше, чем в валах из кованой стали того же состава. Дендриты, расположенные перпендикулярно к поверхности шейки вала, делают литые валы более износостойкими, чем кованые. Графитизиро-ванная сталь, в структуре которой имеются включения графита, по свойствам близка к чугуну с шаровидным графитом, обладая, однако, более высокими механическими свойствами. Из модифицированных чугунов с пластинчатым графитом, имеющих меньший модуль упругости, можно изготовлять коленчатые валы, менее чувствительные к нарушению правильности осевой линии, чем стальные валы. Этим чугунам свойственны высокие динамические характеристики материала.
Чугун с шаровидным графитом и металлической основой из пластинчатого или зернистого перлита — наиболее распространенный материал для изготовления коленчатых валов двигателей автомобилей, тракторов, комбайнов, тепловозов и других
машин. В простейшем случае термообработка вала ограничивается старением его материала, что позволяет механически обрабатывать валы с минимальной правкой для ликвидации коробления. Для увеличения прочности прибегают к термообработке или к легированию N1, Сг, Мо, Си. Для повышения циклической вязкости материала создают чугун со смешанной формой графита — в литье до 25% его находится в пластинчатой форме. С целью повышения износостойкости чугуна иногда применяют азотирование.
Перлитный ковкий чугун, как материал для изготовления коленчатых валов, занимает в зарубежном производстве второе место после стали. Это объясняется в частности, ускоренным отжигом ковкого чугуна за счет добавки к жидкому чугуну висмута и бора (А. А. Горшков, М. М. Волощенко). Отметим, что для тормозных барабанов чугун с шаровидным графитом не имеет никаких преимуществ перед другими чугунами вследствие пониженной теплопроводности.
Применение того или иного смазочного материала в узле трения может повлечь за собой необходимость замены материала по крайней мере одной из трущихся деталей, что связано с изменением вида изнашивания и, как следствие, с иным расположением пар трения по износостойкости. В некоторых амортизационных устройствах шасси самолетов в качестве рабочей жидкости применяли спиртоглицериновую смесь, при использовании которой в качестве смазочного материала буксы из бронзы БрАЖМц в паре со стальной поверхностью быстро изнашивались. Бронза интенсивно обогащалась медью, налипала на стальную поверхность, наращивалась на ней толстым слоем и отлущивалась, частично при этом налипая на поверхность буксы. Бронзы других марок вследствие избирательного переноса при трении во много раз более износостойки. Переход на бронзу БрОФ является здесь целесообразным. Однако существенной разницы в износостойкости безоловянной бронзы БрАЖМц и бронзы БрОФ при трении по стали и смазывании АМГ-10 не установлено. Для букс амортизаторов, работающих на этой жидкости, рентабельнее использовать бронзу БрАЖМц.
Для большей надежности деталей приходится подбирать материал, поступаясь его износостойкостью. В плунжерах топливной аппаратуры двигателей широко применяют пару трения закаленная сталь — закаленная сталь. Между тем такое сочетание материалов для ротора лопастного насоса и лопатки оказалось катастрофическим по причине возникновения задиров и последующего заедания. При использовании бронзовых лопаток ухудшается износостойкость пары, но зато повышается надежность ее работы.
На выбор материалов могут оказать влияние физико-химические явления на поверхностях трения, зависящие от условий работы. Например, высокомарганцовистая сталь — так называемая сталь Гатфильда, из которой изготовляют крестовины рельсов, щеки-камнедробилок, зубья ковшей экскаваторов, броневые плиты шаровых мельниц, желоба для агломерата, воронки для приемки шихты, дозировочные столы и другие детали, в исходном литом состоянии имеет аустенитную структуру с некоторым количеством мартенсита при наличии включений карбидов. После закалки, фиксирующей аустенитную структуру, сталь приобретает высокую прочность при значительной вязкости (ов = 80. Ю0 МПа, ударная вязкость ак = 200. 300 Н-м/см 2 , НВ 200—220) и высокую износостойкость в деталях, подвергающихся изнашиванию при больших давлениях и ударных нагрузках. Большая износостойкость стали обусловлена ее способностью к наклепу, которая тем больше, чем выше удельная нагрузка. Пластическая деформация повышает твердость стали до НВ 500. Наклеп вызывается в меньшей степени превращением аустенита в мартенсит и в большей степени — выделением карбидов, за которым следует измельчение кристаллитов, что повышает сопротивление сплава пластической деформации. Удары при трении приходятся, таким образом, по твердой корке на вязком основании; при износе корка возобновляется.
При эксплуатации тракторов на песчаной почве быстро изнашивались проушины звеньев гусениц, изготовленных из литой стали Гатфильда. По данным лабораторных испытаний в условиях абразивного изнашивания эта сталь не имеет преимуществ перед среднеуглеродистой сталью. Более того, изнашиваемые детали, не испытывающие существенных динамических нагрузок, изготовленные из высокомарганцовистой.стали, служат меньший срок, чем детали из углеродистой стали, как, например, броневые плиты коксовых воронок (данные М. А. Тылкина и В. И. Си-вака). Это можно объяснить следующим: 1) в стали Гатфильда под нагрузкой повышается предел текучести, что сопровождается значительно меньшим повышением сопротивления разрушению при абразивном изнашивании; 2) процесс упрочнения (наклепа) под нагрузкой, обусловленный наличием абразивных частиц, протекает медленнее, чем процесс изнашивания. Высокомарганцовистая сталь слабо сопротивляется коррозии и непригодна для использования при температуре свыше 260°С.
Аналогично обстоит дело с фрикционным материалом — рети-наксом (ФК-16Л), состоящим из фенолформальдегидной смолы, модифицированной канифолью, и наполнителя из барита и асбеста с мелкими отрезками латунной проволоки. Под действием высокой температуры и давления на ретинаксе при трении образуется фрикционный слой, генерируемый по мере изнашивания. Слой состоит из коксообразных продуктов разложения смолы, сернистых соединений, образовавшихся в результате окислительно-восстановительных реакций барита с газообразными продуктами разложения смолы и латуни. Латунь размягчается, размазывается по поверхности трения и поглощает некоторое количество теплоты. Сернистые соединения обладают противозадирны-ми свойствами. Ретинакс целесообразно применять при высокой нагруженности тормозного устройства. При малой его нагружен-ности указанные процессы не происходят и использование рети-накса не дает преимуществ.
При одних и тех же химическом составе и механических свойствах материалы могут значительно различаться по износостойкости, что связано с различием их структур. Например, крупнозернистые сплавы более пластичны и легко прирабатываются, но они менее износостойки. Наличие легко выкрашивающихся твердых или крупных мягких составляющих, склонных к схватыванию с материалом сопряженной детали, является дефектом структуры материалов трущихся деталей. Крупные карбиды в чугунных отливках способствуют образованию сетки термических трещин при работе деталей. Это единичные примеры связи структуры сплава с износостойкостью.
Сложность задачи подбора рациональной структуры материала можно показать на подшипниковых сплавах. Основное требование к структуре антифрикционных сплавов было впервые сформулировано в 1897 г. Г. Шарпи. Согласно правилу Г. Шарпи хорошо работающие антифрикционные сплавы должны иметь равномерно распределенные в пластичной основе твердые зерна с низким коэффициентом трения и малой склонностью к задирам. Действительно, этому правилу удовлетворяли в свое время все известные тогда подшипниковые сплавы. Однако в последующем были разработаны сплавы (например, свинцовая бронза), у которых мягкие включения свинца распределялись в твердой матрице, не говоря уже об однородных антифрикционных материалах, таких, как серебро, полиамиды и др.
В некоторых подвижных сочленениях, как, например, в зубчатых муфтах, в силу небольших взаимных смещений детали изготовляют из незакаленных сталей, как известно, плохо работающих в парах трения. Небольшие перемещения деталей в узле трения часто не вызывают у конструктора опасений относительно износостойкости. Между тем, при недостаточной твердости материалов долговечность изделий может оказаться недостаточной.
Фрикционные материалы должны противостоять термической усталости: на поверхности трения не должно возникать трещин в результате многократного совместного воздействия теплового и силового нагружения. Наиболее стойка к термической усталости графитизированная сталь благодаря стабильности структуры и механических свойств при многократных и быстрых тепловых колебаниях.
Фрикционные материалы не должны при работе повреждать контртело (тормозной барабан), их продукты изнашивания не должны гореть, дымить и выделять неприятные запахи. Эти материалы не должны также вызывать коррозию сопряженных деталей и корродировать сами во влажной атмосфере и при температуре от —60 до +60°С [28, 56]
РАСЧЕТ РЕЗЬБЫ
Коэффициенты трения покоя и трения качения
Сила трения качения описывается как: Fтр=kтр(Fn/r) , где kтр- коэффициент трения а Fn - прижимающая сила, а r - радиус колеса. Размерность коэффициента трения качения, естественно, [длина]. Ниже приводится таблица полезных диапазонов коэффициентов трения качения для различных пар материалов в см.
Коэффициенты трения скольжения для различных материалов
Трущиеся поверхности | k |
Бронза по бронзе | 0,2 |
Бронза по стали | 0,18 |
Дерево сухое по дереву | 0,25 — 0,5 |
Деревянные полозья по снегу и льду | 0,035 |
то же, но полозья обиты стальной полосой | 0,02 |
Дуб по дубу вдоль волокон | 0,48 |
тоже поперек волокон одного тела и вдоль волокон другого | 0,34 |
Канат пеньковый мокрый по дубу | 0,33 |
Канат пеньковый сухой по дубу | 0,53 |
Кожаный ремень влажный по металлу | 0,36 |
Кожаный ремень влажный по дубу | 0,27 — 0,38 |
Кожаный ремень сухой по металлу | 0,56 |
Колесо со стальным бандажом по стальному рельсу | 0,16 |
Лед по льду | 0,028 |
Медь по чугуну | 0,27 |
Металл влажный по дубу | 0,24-0,26 |
Металл сухой по дубу | 0,5-0,6 |
Подшипник скольжения при смазке | 0,02-0,08 |
Резина (шины) по твердому грунту | 0,4-0,6 |
Резина (шины) по чугуну | 0,83 |
Смазанный жиром кожаный ремень по металлу | 0,23 |
Сталь (или чугун) по феродо* и райбесту* | 0,25-0,45 |
Сталь по железу | 0,19 |
Сталь по льду (коньки) | 0,02-0,03 |
Сталь по стали | 0,18 |
Сталь по чугуну | 0,16 |
Фторопласт по нержавеющей стали | 0,064-0,080 |
Фторопласт-4 по фторопласту | 0,052-0,086 |
Чугун по бронзе | 0,21 |
Чугун по чугуну | 0,16 |
Примечание. Звездочкой отмечены материалы, применяемые в тормозных и фрикционных устройствах. |
Таблица коэффициентов трения покоя (коэффициентов сцепления) для различных пар материалов.
Материал
Ксц
Химически чистые металл по металлу
Сплавы, по стали
Стальные поверхности высокой твердости при смазке:
Неметаллические материалы
Коэффициенты трения качения.
Сила трения качения описывается как:
Fтр=kтр(Fn/r) , где kтр- коэффициент трения а Fn - прижимающая сила, а r - радиус колеса.
Размерность коэффициента трения качения, естественно, [длина].
Ниже приводится таблица полезных диапазонов коэффициентов трения качения для различных пар материалов в см.
Стальное колесо по стали | 0,001-0,05 |
Дереянное колесо по дереву | 0,05-0,08 |
Стальное колесо по дереву | 0,15-0,25 |
Пневматичекая шина по асфальту | 0,006-0,02 |
Деревянное колесо по стали | 0,03-0,04 |
Шарикоподшипник (подшипник качения) | 0,001-0,004 |
Роликоподшипник (тоже качения) | 0,0025-0,01 |
Шарик твердой стали по стали | 0,0005-0,001 |
Сила трения скольжения — силы, возникающие между соприкасающимися телами при их относительном движении. Если между телами отсутствует жидкая или газообразная прослойка (смазка), то такое трение называется сухим. В противном случае, трение называется «жидким». Характерной отличительной чертой сухого трения является наличие трения покоя.
Опытным путём установлено, что сила трения зависит от силы давления тел друг на друга (силы реакции опоры), от материалов трущихся поверхностей, от скорости относительного движения и не зависит от площади соприкосновения. (Это можно объяснить тем, что никакое тело не является абсолютно ровным. Поэтому истинная площадь соприкосновения гораздо меньше наблюдаемой. Кроме того, увеличивая площадь, мы уменьшаем удельное давление тел друг на друга.) Величина, характеризующая трущиеся поверхности, называется коэффициентом трения, и обозначается чаще всего латинской буквой «k» или греческой буквой «μ». Она зависит от природы и качества обработки трущихся поверхностей. Кроме того, коэффициент трения зависит от скорости. Впрочем, чаще всего эта зависимость выражена слабо, и если большая точность измерений не требуется, то «k» можно считать постоянным.
В первом приближении величина силы трения скольжения может быть рассчитана по формуле:
=k cdot N!" />
, где
По физике взаимодействия трение принято разделять на:
- Сухое, когда взаимодействующие твёрдые тела не разделены никакими дополнительными слоями/смазками — очень редко встречающийся на практике случай. Характерная отличительная черта сухого трения — наличие значительной силы трения покоя.
- Сухое с сухой смазкой (графитовым порошком)
- Жидкостное, при взаимодействии тел, разделённых слоем жидкости или газа (смазки) различной толщины — как правило, встречается при трении качения, когда твёрдые тела погружены в жидкость;
- Смешанное, когда область контакта содержит участки сухого и жидкостного трения;
- Граничное, когда в области контакта могут содержатся слои и участки различной природы (окисные плёнки, жидкость и т. д.) — наиболее распространённый случай при трении скольжения.
В связи со сложностью физико-химических процессов, протекающих в зоне фрикционного взаимодействия, процессы трения принципиально не поддаются описанию с помощью методов классической механики.
При механических процессах всегда происходит в большей или меньшей степени преобразование механического движения в другие формы движения материи (чаще всего в тепловую форму движения). В последнем случае взаимодействия между телами носят названия сил трения.
Опыты с движением различных соприкасающихся тел (твёрдых по твёрдым, твёрдых в жидкости или газе, жидких в газе и т. п.) с различным состоянием поверхностей соприкосновения показывают, что силы трения проявляются при относительном перемещении соприкасающихся тел и направлены против вектора относительной скорости тангенциально к поверхности соприкосновения. При этом всегда происходит нагревание взаимодействующих тел.
Силами трения называются тангенциальные взаимодействия между соприкасающимися телами, возникающие при их относительном перемещении. Силы трения возникающие при относительном перемещении различных тел, называются силами внешнего трения.
Силы трения возникают и при относительном перемещении частей одного и того же тела. Трение между слоями одного и того же тела называется внутренним трением.
В реальных движениях всегда возникают силы трения большей или меньшей величины. Поэтому при составлении уравнений движения, строго говоря, мы должны в число действующих на тело сил всегда вводить силу трения F тр.
Тело движется равномерно и прямолинейно, когда внешняя сила уравновешивает возникающую при движении силу трения.
Для измерения силы трения, действующей на тело, достаточно измерить силу, которую необходимо приложить к телу, чтобы оно двигалось без ускорения.
Читайте также: